What Is Catastrophic Stress Corrosion
Stress is very common in our life and work. I believe that everyone is familiar with it. Corrosion can be seen everywhere, but when the two are superimposed together, the accidents brought about are destructive and irreparable. If it is on the mold, it will often cause the mold to crack and scrap. If it is on the bridge, airplane, container pipe, it will cause the bridge to collapse, airplane crash, container pipe leakage and other huge loss of property and life. The reason why stress corrosion leads to failure is inconspicuous because at the time of failure, the stress (usually static stress, tensile stress) is also very low, and the corrosion is also very slight. Both of them will cause cracks to occur quickly and under certain conditions. Expansion, so it often leads to accidents.
Each different material has a different specific stress corrosion medium. Specific media for carbon steel and low alloys include NaOH solution, containing nitrate, hydrogen sulfide aqueous solution, sea water, marine atmosphere and industrial atmosphere, sulfuric acid-nitric acid mixture, ferric chloride solution, wet CO-CO2, air; high strength The specific medium of steel includes distilled water, humid atmosphere, chloride solution, and hydrogen sulfide. It can be seen from this specific medium that chloride is the specific corrosive medium of high-strength steel. Wet atmosphere is also relatively common. This specific medium is ours. The mold is easily satisfied during use.
Stress corrosion is the most harmful corrosion. According to statistics, the proportion of various types of corrosion is as follows. It can be seen that the proportion of stress corrosion is very large, and the static tensile stress mainly comes from the following aspects:
- The resistance formed by the applied load on the component under working condition;
- Internal stress caused by processing, manufacturing, and heat treatment;
- Internal stress caused by assembly and installation;
- Thermal stress caused by temperature difference;
- The wedge effect in the crack due to the volume effect of corrosion products can also produce the stress required for crack propagation
The entire stress corrosion cracking process is as follows, with the following characteristics:
- The crack formation time accounts for about 90% of the entire time
- After the crack reaches the critical size, the crack breaks instantaneously by pure mechanical action. The entire process time is related to the material, the stress and the corrosion rate.
- The crack originates from surface corrosion, the direction of crack propagation is perpendicular to the direction of tensile stress, and the crack is generally dendritic (see the figure shown in item d)
- The path of cracks is generally along the crystal type, through the crystal type and mixed type
- The crack growth rate is fast, and the corrosion of the crack tip will accelerate the crack growth
- Fracture fractured by stress corrosion, its color is dark and there are often corrosion products on the surface
- Generally brittle fracture, no obvious plastic deformation
- Pure metals generally do not undergo stress corrosion, only those containing impurities or alloys will occur
To Sum Up
Comprehensive stress and corrosion mechanisms, there are four main factors that produce stress corrosion: environment, electrochemistry, mechanics, and metallurgy.
Precaution
- a) Material selection: Choose less impurities, uniform material, and make appropriate adjustments to the material according to the environment and corrosive medium used
- b) Stress relief: Improve structural design, reduce stress concentration and avoid accumulation of corrosive media, eliminate residual stress by heat treatment, surface shot peening, etc., and try to avoid large residual stress during processing, manufacturing and assembly, such as cooling Stress corrosion cracking at the blockage of the waterway is the most common in mold use
- c) Improve the medium environment: control or reduce harmful components; add corrosion inhibitors to the corrosive medium; or change the potential, promote film formation, prevent the adsorption of hydrogen or harmful substances, etc., which affect the electrochemical reaction kinetics and slow down Erosion; Sensitivity to change the environment
Minghe Die Casting Company Is Custom manufacturer of precision & non-ferrous die castings. Products include aluminum & zinc die castings. Aluminum die castings are available in alloys including 380 & 383. Specifications include plus /- 0.0025 tolerances & maximum molding weight of 10 lbs. Zinc die casting parts are available in standard alloys such as Zamak no. 3, Zamak no. 5 & Zamak no. 7 & hybrid alloys such as ZA-8 & ZA-27. Specifications include plus /- 0.001 tolerances & maximum molding weight of 4.5 lbs.
Please keep the source and address of this article for reprinting: What Is Catastrophic Stress Corrosion
Minghe Die Casting Company are dedicated to manufacture and provide quality and high performance Casting Parts(metal die casting parts range mainly include Thin-Wall Die Casting,Hot Chamber Die Casting,Cold Chamber Die Casting),Round Service(Die Casting Service,Cnc Machining,Mold Making,Surface Treatment).Any custom Aluminum die casting, magnesium or Zamak/zinc die casting and other castings requirements are welcome to contact us.
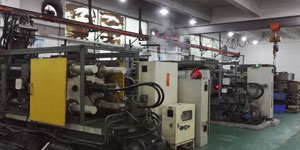
Under the control of ISO9001 and TS 16949,All processes are carried out through hundreds of advanced die casting machines, 5-axis machines, and other facilities, ranging from blasters to Ultra Sonic washing machines.Minghe not only has advanced equipment but also have professional team of experienced engineers,operators and inspectors to make the customer’s design come true.
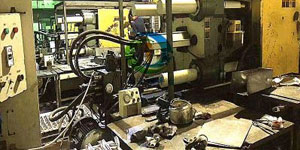
Contract manufacturer of die castings. Capabilities include cold chamber aluminum die casting parts from 0.15 lbs. to 6 lbs., quick change set up, and machining. Value-added services include polishing, vibrating, deburring, shot blasting, painting, plating, coating, assembly, and tooling. Materials worked with include alloys such as 360, 380, 383, and 413.
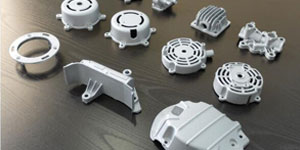
Zinc die casting design assistance/concurrent engineering services. Custom manufacturer of precision zinc die castings. Miniature castings, high pressure die castings, multi-slide mold castings, conventional mold castings, unit die and independent die castings and cavity sealed castings can be manufactured. Castings can be manufactured in lengths and widths up to 24 in. in +/-0.0005 in. tolerance.
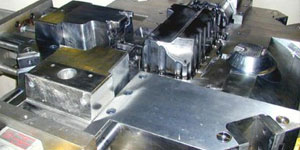
ISO 9001: 2015 certified manufacturer of die cast magnesium, Capabilities include high-pressure magnesium die casting up to 200 ton hot chamber & 3000 ton cold chamber, tooling design, polishing, molding, machining, powder & liquid painting, full QA with CMM capabilities, assembly, packaging & delivery.
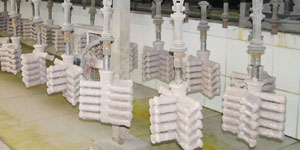
ITAF16949 certified. Additional Casting Service Include investment casting,sand casting,Gravity Casting, Lost Foam Casting,Centrifugal Casting,Vacuum Casting,Permanent Mold Casting,.Capabilities include EDI, engineering assistance, solid modeling and secondary processing.
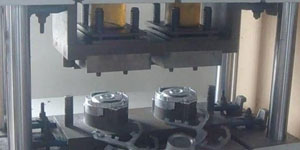
Casting Industries Parts Case Studies for: Cars, Bikes, Aircraft, Musical instruments, Watercraft, Optical devices, Sensors, Models, Electronic devices, Enclosures, Clocks, Machinery, Engines, Furniture, Jewelry, Jigs, Telecom, Lighting, Medical devices, Photographic devices, Robots, Sculptures, Sound equipment, Sporting equipment, Tooling, Toys and more.
What Can we help you do next?
∇ Go To Homepage For Die Casting China
→Casting Parts-Find out what we have done.
→Ralated Tips About Die Casting Services
By Minghe Die Casting Manufacturer |Categories: Helpful Articles |Material Tags: Aluminum Casting, Zinc Casting, Magnesium Casting, Titanium Casting, Stainless Steel Casting, Brass Casting,Bronze Casting,Casting Video,Company History,Aluminum Die Casting |Comments Off