What Is Coated Sand Casting Process
Coated sand casting has a long history in the foundry field, and the output of castings is also quite large; however, the use of coated sand casting to produce precision steel castings faces many problems: sticky sand (scarring), cold barriers, and pores. How to solve these problems remains for us to further explore.
Knowledge and understanding of coated sand (coated sand belongs to organic binder type, core sand)
- (1) Features of coated sand: suitable strength performance; good fluidity, the prepared sand molds and cores have clear contours and dense structures, which can produce complex sand cores; sand molds (cores) have good surface quality and rough surface The degree can reach Ra=6.3~12.5μm, the dimensional accuracy can reach CT7~CT9 grade; the collapsibility is good, and the casting is easy to clean.
- (2) Scope of application: coated sand can be used to make molds and cores. The molds or cores of coated sand can be used in conjunction with each other or with other sand molds (cores); not only can be used for metal gravity Casting or low-pressure casting can also be used for iron sand-coated casting and thermal centrifugal casting; it can be used not only for the production of cast iron and non-ferrous alloy castings, but also for the production of steel castings.
Preparation of coated sand
1. Composition of coated sand
It is generally composed of refractory materials, binders, curing agents, lubricants and special additives.
- (1) Refractories are the main body of coated sand. The requirements for refractory materials are: high refractoriness, less volatile matter, rounder particles, and firmness. Generally choose natural scrubbing silica sand. The requirements for silica sand are: high SiO2 content (cast iron and non-ferrous alloy castings are required to be greater than 90%, steel castings are required to be greater than 97%); mud content is not greater than 0.3% (for scrubbing sand)-[Water-washing sand mud content requirements Less than; particle size ①distributed on adjacent 3 to 5 sieve sizes; rounded grain shape, angular factor should not be greater than 1.3; acid consumption value is not less than 5ml.
- (2) Phenolic resin is generally used as the binder.
- (3) Urotropine is usually used as the curing agent; calcium stearate is generally used as the lubricant, which prevents the coating sand from agglomerating and increases fluidity. The main function of additives is to improve the performance of coated sand.
- (4) The basic proportion of coated sand is the proportion of distribution (mass fraction, %). Note: Raw sand 100 is scrubbing sand, phenolic resin is 1.0~3.0 accounting for the weight of raw sand, and urotropine (aqueous solution 2) is 10-15 The weight of calcium stearate is 5-7 for the weight of the resin, and the weight of the additive is 0.1-0.5 for the raw sand. 1:2) 10-15 accounted for resin weight, calcium stearate 5-7 accounted for resin weight, additive 0.1-0.5 accounted for raw sand weight.
2. Production process of coated sand
The preparation process of coated sand mainly includes cold coating, warm coating, and thermal coating. At present, almost all the production of coated sand adopts the hot coating method. The thermal coating process is to first heat the raw sand to a certain temperature, then mix and stir with the resin, urotropine aqueous solution and calcium stearate, then cool, crush and sieving. Due to the difference in formula, the mixing process is different. At present, there are many types of coated sand production lines in China. There are about 2,000 to 2,300 semi-automatic production lines for manual feeding, and nearly 50 computer-controlled automatic production lines have effectively improved production efficiency and product stability. For example, the automatic visual production line of xx Casting Co., Ltd., its feeding time is controlled to 0.1 second, the heating temperature is controlled to 1/10 ℃, and the sand mixing state can be observed through the video, and the production efficiency reaches 6 tons/hour.
3. The main product types of coated sand
- (1) Ordinary coated sand Ordinary coated sand is traditional coated sand. Its composition is usually composed of quartz sand, thermoplastic phenolic resin, urotropine and calcium stearate. No additives are added, and the amount of resin added is usually It is relatively high under certain strength requirements, and does not have the characteristics of high temperature resistance, low expansion, and low gas evolution. It is suitable for the production of castings with low requirements.
- (2) High-strength, low-gassing type coated sand features: high strength, low expansion, low gas evolution, slow gas evolution, anti-oxidation. Brief introduction: high-strength, low gas-generating coated sand is an updated product of ordinary coated sand. By adding relevant characteristic "additives" and adopting new The compounding process greatly reduces the amount of resin, its strength is more than 30% higher than that of ordinary coated sand, and the gas generation volume is significantly reduced, and can delay the gas generation speed, which can better meet the needs of casting production. This kind of coated sand is mainly used in the production of iron castings, small and medium steel castings and alloy steel castings. At present, there are three series of this kind of coated sand: GD-1 high-strength low-gassing coated sand; GD-2 high-strength, low-expansion, low-gassing coated sand; GD-3 high-strength, low-expansion, low-gassing and anti-oxidation coating .
- (3) High temperature resistant (type) coated sand (ND type) features: high temperature resistance, high strength, low expansion, low gas generation, slow gas generation, easy to collapse, anti-oxidation Introduction: high temperature resistant coated sand is produced through a special process formula technology with excellent high temperature performance (high strength at high temperature, A new type of coated sand with long heat resistance time, small thermal expansion, low gas evolution) and comprehensive casting performance. This type of coated sand is particularly suitable for the production of complex thin-walled precision cast iron parts (such as automobile engine cylinder blocks, cylinder heads, etc.) and high-demand steel castings (such as container corners and train brakes; middle shell parts, etc.) , Can effectively eliminate casting defects such as sand sticking, deformation, hot cracking and pores. At present, the coated sand has four series: VND-1 high temperature resistant coated sand. ND-2 high temperature resistant, low expansion and low gas generation coated sand ND-3 high temperature resistant, low expansion, low gas generation and oxidation resistant coated sand ND-4 High temperature resistant, high strength bottom, low expansion and low outgassing film
- (4) Easily collapsible coated sand has good strength and excellent low-temperature collapsibility performance, which is suitable for the production of non-ferrous metal castings.
- (5) Other special requirements coated sand In order to meet the needs of different products, a series of special coated sands have been developed, such as: coated sand for centrifugal casting, chilled coated sand, wet coated sand, anti-sticking sand, and Veining, anti-orange peel coated sand, etc.
The main process of core making with coated sand
The heating temperature is 200-300℃, the curing time is 30-150s, and the sand shooting pressure is 0.15-0.60MPa. The sand core with simple shape and the coated sand with good fluidity can choose lower sand shooting pressure, and the thin sand core chooses lower heating temperature. When the heating temperature is low, the curing time can be appropriately extended. The resin used for coated sand is phenolic resin. The advantages of the core-making process: suitable strength performance; good fluidity; good surface quality of the sand core (Ra=6.3-12.5μm); strong moisture absorption resistance of the sand core; good collapsibility and easy cleaning of castings.
1. Mold (mold) temperature
The mold temperature is one of the main factors affecting the thickness and strength of the shell. It is generally controlled at 220-260°C and selected according to the following principles: (1) Ensuring sufficient heat required for the softening and curing of the resin on the coated sand; ( 2) Ensure that the required shell thickness is formed and the surface of the shell (core) is not coked; (3) Try to shorten the crust and hardening time to improve productivity.
2. Sand shooting pressure and time
The sand shooting time is generally controlled within 3~10s. If the time is too short, the sand mold (core) cannot be formed. The sand shooting pressure is generally about 0.6MPa; when the pressure is too low, it is easy to cause insufficient shooting or looseness. 3. Hardening time: The length of hardening time mainly depends on the thickness of the sand mold (core) and the temperature of the mold, generally around 60-120s. If the time is too short, the shell layer will not be fully solidified and the strength will be low; if the time is too long, the surface layer of the sand mold (core) is easy to scorch and affect the quality of the casting. Examples of process parameters for coated sand modeling (core): serial number drawing number shell thickness (㎜) weight (㎏) mold temperature (℃) sand shooting time (s) hardening time (s) 1 (guide sleeve) DN80-05 8~ 10 2.5~2.6 220~240 2~3 60~80 2 (valve body) DN05-01 10~12 3.75~3.8 240~260 3~5 80~100
The problems existing in the application of coated sand and their solutions
There are many types of core-making methods, which can be divided into two categories: thermosetting methods and cold-setting methods. Coated sand core-making methods belong to the category of thermosetting methods.
Any core-making method has its own advantages and disadvantages, which mainly depend on the comprehensive factors such as product quality requirements, complexity, production batch, production cost, product price, etc. to determine which core-making method to use. It is very effective to use coated sand for sand cores with high requirements on the surface quality of the casting cavity, high dimensional accuracy, and complex shapes. For example: sand cores for intake and exhaust passages, water passage sand cores, and oil passage sand cores of car engine cylinder heads, water passage sand cores and oil passage sand cores for cylinder blocks, shell core sand cores for intake manifolds and exhaust manifolds, Runner sand core of hydraulic valve, air passage sand core of automobile turbocharger, etc. However, some problems are often encountered in the use of coated sand. Here I will only briefly talk about the experience in work.
1. The method of determining the strength and gas volume of coated sand
On the premise that the quality of raw sand and resin are certain, the key factor affecting the strength of coated sand is mainly the amount of phenolic resin added. If the amount of phenolic resin added is large, the strength will be improved, but the amount of outgassing will also increase, and the collapsibility will decrease. Therefore, in production and application, the strength of the coated sand must be controlled to reduce the amount of gas and improve the collapsibility. A balance point must be found when the strength standards are formulated. This balance point is to ensure the surface quality of the sand core and its strength under the premise of no deformation and no core breakage during pouring. In this way, the surface quality and dimensional accuracy of the castings can be guaranteed, the gas generation can be reduced, the pore defects of the castings can be reduced, and the sand production performance of the sand core can be improved. For the storage of sand cores, work station tools and sand core trolleys can be used in the transportation process, and 10mm-15mm thick sponges can be laid on them, which can reduce the loss rate of sand cores.
2. The storage period of coated sand cores
Any sand core will absorb moisture, especially in the southern area where the relative humidity is high. The storage period of the sand core must be specified in the process documents, and the lean production method of first-in first-out production is used to reduce the storage volume and storage period of the sand core. Each enterprise should determine the storage period of the sand core based on its own plant conditions and local climatic conditions.
3. Control the supply quality of coated sand
The coated sand must be accompanied by the supplier's quality assurance materials when it enters the factory, and the company shall inspect it according to the sampling standards, and only after the inspection is qualified can it be put into the warehouse. The quality assurance and technical department will make the processing result when the enterprise sampling test fails, and it is a concession to accept or return the goods to the supplier.
4. Qualified coated sand is found to be fractured and deformed during core making
The fracture deformation of the sand core during core making is usually considered to be caused by the low strength of the coated sand. In fact, the core fracture and deformation will involve many production processes. In the event of an abnormal situation, the real cause must be found to be completely resolved. The specific reasons are as follows:
- (1) The mold temperature and mold retention time during core making are related to whether the hardened thickness of the sand core crust meets the process requirements. The process parameters specified in the process need to have a range, and this range needs to be adjusted by the skill of the operator. When the mold temperature is at the upper limit, the mold retention time can take the lower limit, and when the mold temperature is at the lower limit, the mold retention time can take the upper limit. Operators need to be continuously trained to improve their operating skills.
- (2) Phenolic resin and sand particles will stick to the mold during core making. It must be cleaned in time and sprayed with release agent, otherwise the sand core will be broken or deformed when the mold is opened.
- (3) The spring ejector pin on the static mold of the hot core box mold will break or deform due to elastic failure due to long-term work under high temperature conditions. The spring must be replaced in time.
- (4) The movable mold and the static mold are not parallel or on the same center line. When the mold is closed, under the pressure of the oil cylinder or the air cylinder, the front end of the positioning pin has a certain slope, and the mold will still close tightly, but when the mold is opened, the movable mold and The static mold will still be restored to its original state and the sand core will be broken or deformed. In this case, sand will run out when sand is shot, and the size of the sand core will become larger. The solution is to adjust the parallelism and coaxiality of the mold in time.
- (5) When producing hollow sand cores on the shell core machine, when the unhardened coated sand is poured out of the core and needs to be reused, the unused coated sand must be sieved and mixed in a ratio of 3:7. , So as to ensure the surface quality and strength of the core sand core.
Please keep the source and address of this article for reprinting: What Is Coated Sand Casting Process
Minghe Die Casting Company are dedicated to manufacture and provide quality and high performance Casting Parts(metal die casting parts range mainly include Thin-Wall Die Casting,Hot Chamber Die Casting,Cold Chamber Die Casting),Round Service(Die Casting Service,Cnc Machining,Mold Making,Surface Treatment).Any custom Aluminum die casting, magnesium or Zamak/zinc die casting and other castings requirements are welcome to contact us.
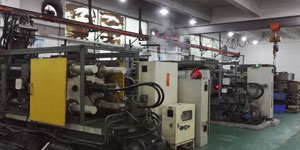
Under the control of ISO9001 and TS 16949,All processes are carried out through hundreds of advanced die casting machines, 5-axis machines, and other facilities, ranging from blasters to Ultra Sonic washing machines.Minghe not only has advanced equipment but also have professional team of experienced engineers,operators and inspectors to make the customer’s design come true.
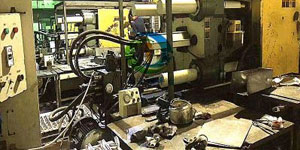
Contract manufacturer of die castings. Capabilities include cold chamber aluminum die casting parts from 0.15 lbs. to 6 lbs., quick change set up, and machining. Value-added services include polishing, vibrating, deburring, shot blasting, painting, plating, coating, assembly, and tooling. Materials worked with include alloys such as 360, 380, 383, and 413.
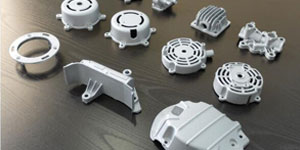
Zinc die casting design assistance/concurrent engineering services. Custom manufacturer of precision zinc die castings. Miniature castings, high pressure die castings, multi-slide mold castings, conventional mold castings, unit die and independent die castings and cavity sealed castings can be manufactured. Castings can be manufactured in lengths and widths up to 24 in. in +/-0.0005 in. tolerance.
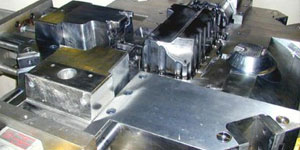
ISO 9001: 2015 certified manufacturer of die cast magnesium, Capabilities include high-pressure magnesium die casting up to 200 ton hot chamber & 3000 ton cold chamber, tooling design, polishing, molding, machining, powder & liquid painting, full QA with CMM capabilities, assembly, packaging & delivery.
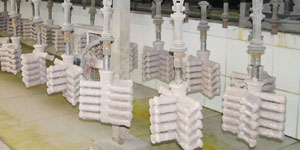
ITAF16949 certified. Additional Casting Service Include investment casting,sand casting,Gravity Casting, Lost Foam Casting,Centrifugal Casting,Vacuum Casting,Permanent Mold Casting,.Capabilities include EDI, engineering assistance, solid modeling and secondary processing.
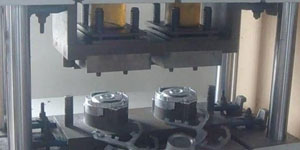
Casting Industries Parts Case Studies for: Cars, Bikes, Aircraft, Musical instruments, Watercraft, Optical devices, Sensors, Models, Electronic devices, Enclosures, Clocks, Machinery, Engines, Furniture, Jewelry, Jigs, Telecom, Lighting, Medical devices, Photographic devices, Robots, Sculptures, Sound equipment, Sporting equipment, Tooling, Toys and more.
What Can we help you do next?
∇ Go To Homepage For Die Casting China
→Casting Parts-Find out what we have done.
→Ralated Tips About Die Casting Services
By Minghe Die Casting Manufacturer |Categories: Helpful Articles |Material Tags: Aluminum Casting, Zinc Casting, Magnesium Casting, Titanium Casting, Stainless Steel Casting, Brass Casting,Bronze Casting,Casting Video,Company History,Aluminum Die Casting |Comments Off