What Is Mold Trial For Die Casting
Die-casting mold trial is a verification process of actual production and mold design, and it is also an important process of die-casting mold, equipment, process optimization and adjustment to mass production. This article mainly introduces the process of mold design to mold trial verification and subsequent optimization and adjustment.
In the stage of die-casting new product development and new mold trial, there will be more or less problems that lead to failure of the trial. And there are many factors that affect the failure of the model test. What are the relevant factors?
First of all, review and analysis of the casting structure and mold gating system design in the development stage. Secondly, the process parameters of die-casting production such as molten metal temperature, die-casting pressure, speed and fast switching point are reasonable. And so on, some factors are the key to directly affecting the internal and external quality of die castings.
But in most cases, mold design and production are closely related. Factors that affect the mold, including the number of cavities, the design of the gate system, the type of gate (position, area, direction), etc., for castings with large wall thickness differences, local high-pressure spot cooling and core cooling are also used. To achieve the purpose of balancing the mold temperature. Only with a good mold design can a wider range of process parameters be obtained, which is more conducive to the internal and external quality of the casting. For specific review and analysis, we have to use some auxiliary software. For example: mold flow analysis software, process parameter analysis software PQ 2 diagram and so on.
Theoretical Data Analysis
1) Analyze the initial design of the gate location, area and direction, the location of the slag bag exhaust, etc. through the mold flow software. Understand the entrainment, temperature distribution, flow path and velocity of the molten metal flowing in the cavity, as well as the slag collection and exhaust of the slag bag, and find out the problems to provide a basis for the next review and modification, so as to get Better gating system.
2) Using the PQ 2 diagram to insert the mold, equipment and other parameters analysis, we can initially set the process parameters and the rationality of the press tonnage selection, find out the problems in the process parameter settings and correct them in time; and we can also get the theory The above process parameters have guiding significance for the adjustment of the process parameters of the die casting machine.
Die Casting Mold Trial And Process Parameter Optimization
The main purpose of mold trial is to find out the optimized process parameters and mold modification plan. It is required that even if the materials, machine settings or environmental factors have changed, it can still ensure that the mold can stably and uninterruptedly produce qualified products in batches. Improve the "adaptability" of the mold to the limit, not just to get a few good test mold samples.
Preparatory work before mold test. According to the design drawings of the mold, perform a detailed inspection of the relevant dimensions (especially the size of the sprue bushing interface); figure out the action sequence of each movable part of the mold (core pulling and slider); confirm what is to be adopted The die casting machine model, injection position, tubing interface, pressure chamber diameter and interface size are consistent with the actual requirements of the mold. Special attention must be paid to the die-casting machine used in the trial mold must match the model of the die-casting machine used in the mass production of the mold, otherwise the mold may be unusable.
According to the theoretical process parameters obtained from the PQ2 chart, trial production is conducted to find the difference between actual and theoretical parameters. And continue to adjust and modify, until a well-formed casting with good internal quality is obtained. Among them, the performance of the press may be unstable, which makes it difficult for us to judge the problem. At this time, the "injection monitor" can be used to monitor the speed, pressure, displacement and other parameters in the injection process, and judge by the fluctuation of the curve. Help us accurately find the problem, effectively guide the correction of process parameters and understand the performance of the equipment. In the end, a set of optimal process parameters suitable for this equipment will be obtained.
The molds produced by the mold factory are often due to poor design considerations or improper processing in the production process. There are often some problems, such as over-tolerance, unsmooth local transitions, improper structure, and unreasonable cooling water layout. Large temperature difference, etc., resulting in unqualified castings or failure of mold trial production. Due to the difference between actual results and theory, mold trial is the simplest, direct and effective way to find out mold problems. You can also know the temperature distribution of the mold and whether the cooling water location is reasonable through the thermal imaging diagram, which is very helpful to extend the life of the mold. It also has guiding significance for spray adjustment.
In the trial mold process, the trial mold parts produced after the process parameters are stabilized require on-site review by product engineers, process technicians and quality engineers according to customer requirements. The main review contents are:
- Measurement of key dimensions and measurement of machining surface margin;
- Whether the molding of the appearance contour of the casting is intact, whether the parting line is wrong, whether there is strain, tear, shrinkage, etc.;
- Anatomy and X-ray inspection to check the porosity and shrinkage inside the casting. Understand the quality status of castings and mold problems through preliminary review, and provide basis and guidance for later rectification.
Die-casting mold trial is not only a process of theoretical and practical derivation and verification, but also a process of continuous error correction and improvement. Moreover, contemporary die-casting has more high-tech auxiliary software and equipment to help us test the mold more scientifically. Make a systematic analysis of the casting structure, mold structure, die-casting process and the performance of die-casting equipment to find out the differences and problems. After the problem is solved, the mold structure and process parameters are optimized. Make our molds more suitable for stable production and quality maintenance. This fully embodies the significance of die-casting mold trial.
Please keep the source and address of this article for reprinting: What Is Mold Trial For Die Casting
Minghe Casting Company are dedicated to manufacture and provide quality and high performance Casting Parts(metal die casting parts range mainly include Thin-Wall Die Casting,Hot Chamber Die Casting,Cold Chamber Die Casting),Round Service(Die Casting Service,Cnc Machining,Mold Making,Surface Treatment).Any custom Aluminum die casting, magnesium or Zamak/zinc die casting and other castings requirements are welcome to contact us.
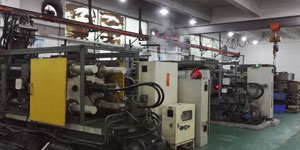
Under the control of ISO9001 and TS 16949,All processes are carried out through hundreds of advanced die casting machines, 5-axis machines, and other facilities, ranging from blasters to Ultra Sonic washing machines.Minghe not only has advanced equipment but also have professional team of experienced engineers,operators and inspectors to make the customer’s design come true.
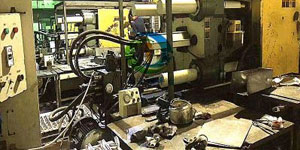
Contract manufacturer of die castings. Capabilities include cold chamber aluminum die casting parts from 0.15 lbs. to 6 lbs., quick change set up, and machining. Value-added services include polishing, vibrating, deburring, shot blasting, painting, plating, coating, assembly, and tooling. Materials worked with include alloys such as 360, 380, 383, and 413.
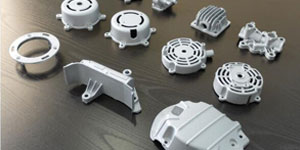
Zinc die casting design assistance/concurrent engineering services. Custom manufacturer of precision zinc die castings. Miniature castings, high pressure die castings, multi-slide mold castings, conventional mold castings, unit die and independent die castings and cavity sealed castings can be manufactured. Castings can be manufactured in lengths and widths up to 24 in. in +/-0.0005 in. tolerance.
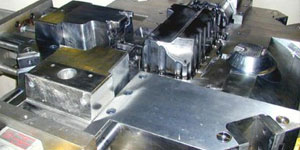
ISO 9001: 2015 certified manufacturer of die cast magnesium, Capabilities include high-pressure magnesium die casting up to 200 ton hot chamber & 3000 ton cold chamber, tooling design, polishing, molding, machining, powder & liquid painting, full QA with CMM capabilities, assembly, packaging & delivery.
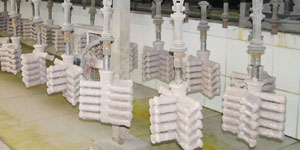
ITAF16949 certified. Additional Casting Service Include investment casting,sand casting,Gravity Casting, Lost Foam Casting,Centrifugal Casting,Vacuum Casting,Permanent Mold Casting,.Capabilities include EDI, engineering assistance, solid modeling and secondary processing.
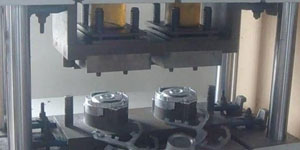
Casting Industries Parts Case Studies for: Cars, Bikes, Aircraft, Musical instruments, Watercraft, Optical devices, Sensors, Models, Electronic devices, Enclosures, Clocks, Machinery, Engines, Furniture, Jewelry, Jigs, Telecom, Lighting, Medical devices, Photographic devices, Robots, Sculptures, Sound equipment, Sporting equipment, Tooling, Toys and more.
What Can we help you do next?
∇ Go To Homepage For Die Casting China
→Casting Parts-Find out what we have done.
→Ralated Tips About Die Casting Services
By Minghe Die Casting Manufacturer |Categories: Helpful Articles |Material Tags: Aluminum Casting, Zinc Casting, Magnesium Casting, Titanium Casting, Stainless Steel Casting, Brass Casting,Bronze Casting,Casting Video,Company History,Aluminum Die Casting |Comments Off