What Is Pressure Die Casting? What Is Die-Casting Process?
High pressure casting is a kind of special casting method with less cutting and no cutting which has developed rapidly in modern metal processing technology. It is a process in which molten metal is filled into a mold under high pressure and high speed, and crystallized and solidified under high pressure to form a casting. High pressure and high speed are the main characteristics of high pressure casting. The commonly used pressure is tens of megapascals, the filling speed (inner gate speed) is about 16-80 m/s, and the time for molten metal to fill the mold cavity is extremely short, about 0.01-0.2 seconds. Because the products produced by this method have the advantages of high production efficiency, simple procedures, higher tolerance levels of castings, good surface roughness, and high mechanical strength, it can save a lot of machining procedures and equipment, save raw materials, etc., so it has become a casting An important part of the industry.
The Main Process Parameters Of The Die-Casting Process
1. Introduction to Die Casting Process
- A: Die-casting process is a process of organic combination of the three elements of die-casting machine, die-casting mold, and die-casting alloy.
- B: The process of metal filling the cavity during die-casting is a process of dynamically balancing process factors such as pressure, speed, temperature and time.
- C: These process factors both restrict each other and complement each other. Only by correctly selecting and adjusting these factors to make them coordinated can the expected results be obtained. In the die casting process, not only the processability of the casting structure, but also the advanced nature of the mold, can be obtained. The performance and structure of the die-casting machine are excellent, the adaptability of the die-casting alloy selection and the standardization of the smelting process. More attention should be paid to the important effect of pressure, speed, and time on the quality of castings.
2. Pressure
The existence of pressure is the main feature that distinguishes the die-casting process from other casting methods. Pressure is the factor that makes the castings obtain compact structure and clear outline; pressure can be expressed in injection force and specific pressure.
2.1 Injection force
Injection force is the force that pushes the movement of the injection piston in the injection mechanism of the die casting machine. Injection force is a main parameter reflecting the function of die casting machine. The size of the injection force is determined by the cross-sectional area of the injection cylinder and the pressure of the working fluid in the injection chamber. The formula of injection force is as follows: F pressure = P liquid XA cylinder
2.2 Specific Pressure
The pressure of the molten metal in the pressure chamber per unit area is called the specific pressure. The specific pressure is the ratio of the injection force to the cross-sectional area of the pressure chamber. The calculation formula is as follows: P ratio = P injection / A chamber
The specific pressure is the expression method of the actual force of the molten metal at each stage of the filling process, and reflects the concept of the force of the molten metal at each stage of the filling and when the metal flows through different cross-sectional areas. The specific pressure during filling is called the filling specific pressure or injection specific pressure. The specific pressure in the boost phase is called the boost specific pressure. The magnitudes of the two specific pressures are also determined according to the injection force.
2.3 The Role And Influence Of Pressure
- A: The filling specific pressure is to overcome the flow resistance in the gating system and the cavity, especially the resistance at the inner gate, so that the metal liquid flow can reach the required inner gate speed.
- B: The boost pressure and the specific pressure determine the pressure on the solidified metal and the bulging force formed at this time. The influence of the specific pressure on the mechanical properties of the casting: increased specific pressure, fine crystals, and increased fine-grained layers Thicker, due to improved filling characteristics, improved surface quality, reduced pore effects, and improved tensile strength.
- C: Effect on filling conditions: The alloy melt fills the cavity under high specific pressure, the alloy temperature rises, and the fluidity improves, which is beneficial to the improvement of the quality of castings.
3. Speed
During the die-casting process, the injection speed is directly affected by the pressure, and together with the pressure, it plays an important role in the internal quality, surface requirements and contour clarity of the casting. Pressure is the basic speed representation of speed is divided into two types: punch speed and ingate speed.
3.1 The relationship between punch speed and intercourse speed
According to the principle of continuity, at the same time, the volume of the metal flow flowing through the alloy liquid with the cross-sectional area of the pressure chamber F1 at the speed V1 should be equal to the volume of the alloy liquid flowing through the inner gate with the cross-sectional area F2 at the speed V2 F1 chamber V1 shot = Within F2 and within V2. Therefore, the higher the injection speed of the injection hammer, the higher the metal flowing through the gate.
3.2 Injection speed
- A: The injection speed is divided into two levels. The first level injection speed is also called slow injection speed. This level of speed refers to the movement speed of the punch from the initial movement until the punch sends the molten metal in the room into the inner gate. At this stage, it is required to fill the pressure chamber with the molten metal in the pressure chamber, under the principle of not reducing the temperature of the alloy liquid too much, but also helping to eliminate the gas in the pressure chamber.
- B: The secondary injection speed is also called the fast injection speed. This speed is determined by the characteristics of the die-casting machine. The maximum injection speed given by the die-casting machine is generally within the range of 4-5 m/s.
3.3 The Role And Influence Of Fast Injection Speed
The effect and influence of fast injection speed on the mechanical properties of alloys, increase the injection speed, convert kinetic energy into heat energy, improve the fluidity of the alloy melt, help eliminate defects such as flow marks, cold barriers, and improve mechanical properties and surface quality , But when the speed is too fast, the alloy melt will be misty and mixed with gas, resulting in serious entrapment and degradation of mechanical properties.
3.4 Inner Gate Speed
The linear velocity when the molten metal enters the inner gate and is introduced into the cavity is called the inner gate speed; the usual range of the inner gate speed is 15-70 m/s. The speed of the inner gate has a great influence on the mechanical properties of the casting. If the speed of the inner gate is too low, the strength of the casting decreases; the speed increases, the strength increases; the speed is too high, and the strength decreases.
4. Temperature
In the die casting process, temperature plays an important role in the thermal state of the filling process and the efficiency of the operation. The temperature referred to in die casting refers to pouring, temperature and mold temperature. Temperature control is an important industrial factor for obtaining good castings. The pouring temperature of molten metal refers to the average temperature when it enters the cavity from the pressure chamber. Because it is inconvenient to measure the temperature of the molten metal in the filling chamber, it is generally expressed as the temperature of the holding furnace.
4.1 The Role And Influence Of Pouring Temperature
The influence of alloy temperature on the mechanical properties of castings. As the alloy temperature increases. The mechanical performance has improved, but after a certain limit, the performance deteriorates, the main reasons are:
- A: The solubility of gas in the alloy increases with the increase of temperature. Although the gas dissolved in the alloy, it is difficult to precipitate during the die-casting process, which affects the mechanical properties.
- B: The iron content increases with the increase of alloy temperature, which reduces fluidity, coarse crystals, and deteriorates performance
- C: Aluminum and magnesium alloys become more oxidized with increasing temperature, oxidizing inclusions, and deteriorating the properties of the alloy.
4.2 The Role And Influence Of Mold Temperature
During the die casting process, the mold requires a certain temperature. The temperature of the mold is another important factor in the die casting process, which plays an important role in improving production efficiency and obtaining high-quality castings.
During the filling process, the mold temperature has a great influence on the metal liquid temperature, viscosity, fluidity, filling time, direct filling flow state, etc. When the mold temperature is too low, the surface layer is condensed and the high-speed liquid flow breaks again, resulting in a surface layer Defects, even if the molding temperature is too high, although it is beneficial to obtain a smooth surface of the casting, it is easy to shrink and dent
The mold temperature has a significant effect on the cooling rate, crystalline state, and shrinkage stress of the alloy melt.
If the mold temperature is too low, the shrinkage stress will increase, and the casting is prone to cracks.
Mold temperature has a great influence on mold life. Intense temperature changes form a complex stress state, and frequent stress changes cause early cracks.
The mold temperature has an effect on the dimensional tolerance level of the casting. If the mold temperature is stable, the dimensional shrinkage of the casting is also stable, and the dimensional tolerance level is also improved.
5. Time
The "time" in the die-casting process is the filling time, pressure build-up time, pressure holding time and mold retention time. These "times" are all three factors of pressure, speed, and temperature, plus the physical properties of molten metal. , Casting structure (especially wall thickness), mold structure (especially pouring system and overflow system) and other comprehensive results.
5.1 Filling Time
The time required for the molten metal to enter the cavity under pressure until it is filled is called the filling time. The filling time of galvanized parts is 0.02S, and the filling time of fuel injection parts is 0.04S.
5.2 Filling Time
The boost pressure build-up time refers to the boost phase of the molten metal in the filling process, starting from the instant when the cavity is filled, until the boost pressure reaches a predetermined value, that is, from the injection specific pressure rise to the increase The time it takes for the pressure to build up
5.3 Holding Time
After the molten metal fills the cavity, the period of time during which the molten metal is solidified under the action of the boost pressure is called the holding time. The function of the holding time is to make the injection punch transfer the pressure through the unsolidified remaining material and the unsolidified metal in the gate part to the cavity, so that the solidified metal will crystallize under the pressure to obtain a dense casting.
3. Die Casting Design
In order to fundamentally prevent the occurrence of defective products and mass-produce die-casting parts at low cost, the design of die-casting parts must be suitable for die-casting production. A good die-casting design can ensure the life, production, and production reliability of the mold. With a good yield rate, the following will explain the design principles and requirements from the structure and process of die castings.
1. Avoid inner concave and minimize the number of side core pulls when designing
2. Design of the wall thickness of die castings
The wall thickness of die castings is generally 2-5 mm. It is generally considered that a wall thickness of 7 mm or more is not good because its strength decreases with the increase of the wall thickness. In addition, the design of wall thickness should follow the principle of equal wall thickness as much as possible, mainly to prevent the large difference between the shrinkage stress generated by local hot joints and different thicknesses from causing internal pores, deformation, cracks and other defects.
3. Round corner design of die casting
Except for special matching requirements, all parts of the casting should be designed with rounded corners. The function of rounded corners is to avoid stress concentration and cracking, and at the same time extend the life of the mold. In addition, when the parts have surface treatment requirements, the rounded corners can be evenly coated. Floor.
4. Design of draft angle of die casting
The role of the draft angle is to make the product demold smoothly, reduce the tightening force of the parts and avoid the parts from straining. The minimum inclination of the die-cast parts is listed in the following table, and the largest inclination should be taken if it is allowed. , The general range is 1-3 degrees on one side.
5. The design of the ejection position of the die casting process
After the mold is opened in the die-casting process, the product is wrapped on the movable mold and must be ejected by the ejector pin of the mold. Therefore, the product must have enough space to place the ejector pin. The diameter of the ejector pin of the die-cast product is generally above 5 mm and below 5 mm. It is often broken during production, so it is not recommended. When designing die-cast products, consider whether there is enough ejection space and position. Try to avoid using special-shaped thimble and use round thimble. At the same time, pay attention to the position of thimble and the wall. Sufficient distance, generally greater than 3 mm.
6. Reduce the design of subsequent processing of die castings
Die-casting parts can achieve high dimensional accuracy, so most surfaces and parts do not require mechanical processing and can be directly assembled and used. At the same time, mechanical processing is not supported for the following two reasons. One is that the surface of the casting is hard and wear-resistant, and it will be lost after processing. This chilled layer, the second is that there are usually pores inside the die casting. The dispersed small pores do not affect the use. After processing, the pores are exposed to affect the appearance and use function. Even if there are special requirements that require mechanical processing, it should be used. Reasonably control the machining allowance, reduce the machining time and the chance of leaking air holes. Generally, the machining allowance is controlled below 0.8. In order to minimize the mechanical processing, it is required to formulate the tolerance of the drawing reasonably to ensure the installation of the parts. Inappropriate tolerance range will increase subsequent machining. Second, reasonable design reduces the shrinkage and deformation of parts. Third, angled mounting holes can be considered for butt-shaped holes.
7. Embedded design in die casting design
Metal or non-metal inserts can be cast into die-casting parts, mainly to improve local strength and wear resistance or form difficult-to-form inner cavities. The part where the insert is embedded in the metal should be designed to prevent rotation and prevent axial movement. Consider the convenience of inserting the insert into the mold and the stability of withstanding the impact of molten metal
5. Cases of solving the quality problems of die castings.
The problem of not seeing light in the processing of 100 faces from the shell
1.1 Status survey
1.2 The reason why the processing does not see the light
1.2.1 When processing the shell, first use the B1, B2, and B3 end faces as the reference surface to process the moving die surface, and then use the processed moving die surface as the reference surface to process the static die surface. After measuring the invisible part, it is found that the movable mold surface is a bevel after processing (as shown in the figure below). Compared with the normal processed part, the movable mold surface of the invisible part is locally processed by 1mm more. It is caused by improper clamping of B2 datum plane or deformation of the datum plane during processing.
1.3. Reasons for deformation of B2 datum hole
1.3.1 The thickness of the partial type burr causes the end face of the B2 reference hole to become higher. The wall thickness of the invisible part B2 is 8mm, and the two wall thicknesses of the normal processed part B are the same. The thickness of the wall changes little. The thickness of the burr is not the reason for the increase of the end surface of the B2 reference hole.
1.3.2 The cores of holes B1, B2, and B3 on the mold have been fixed, and no core retreat has been found. The core retreat problem can be eliminated.
1..3 The bump at the B2 hole causes its deformation. Observe the returned faulty part. There are serious bumps at the B2 hole, and it is not a new bump. The bump is the main cause of the deformation at the B2 hole.
1.4 Conclusion
Conclusion: Due to the collision, the B2 hole is deformed to the static mold side, which makes the B2 higher when the movable mold surface is processed. The movable mold surface is processed into a bevel, and the local processing is 1mm more; when processing the static mold surface, the movable mold surface is used as the reference plane , The static mold part corresponding to the multi-processing position of the movable mold has no processing amount, which causes the static mold side processing to be invisible.
1.5 Improvement measures
1.5.1 When placing the parts in the die-casting workshop and the cleaning workshop, place them carefully and place them neatly to avoid knocking the castings and strictly follow the process. Put two layers of cardboard between each layer of castings. Storage and transportation department. During the turnover, prevent the forklift from hitting the parts, and prevent the parts from bumping due to inappropriate fork transportation methods and excessive transportation speed.
1.5.2 Clean the parting burrs in time to avoid too thick parting burrs.
2.2 Reason analysis
2.2.1 The hole diameter of the part where the pores appear in the 701# hole of Lishell is q26, the hole diameter after processing is p27.9, the machining allowance is 0.95mm, the machining allowance is large, and pores are easy to appear.
2.3 Conclusion
Conclusion: The 701# core temperature is too high, it is in the deep cavity and the exhaust is poor, and the machining allowance is too large, which causes the 701# hole to be prone to pores after processing.
2.4 Improvement measures
2.4.1 The technical department designed to add water to the 701# hole to reduce the core temperature; change the mold drawing, add an overflow groove at the 701# hole to strengthen the exhaust effect; change the core drawing, and change the 701# hole machining allowance Reduced from 0.9mm to 0.7mm.
Please keep the source and address of this article for reprinting: What Is Pressure Die Casting? What Is Die-Casting Process?
Minghe Die Casting Company are dedicated to manufacture and provide quality and high performance Casting Parts(metal die casting parts range mainly include Thin-Wall Die Casting,Hot Chamber Die Casting,Cold Chamber Die Casting),Round Service(Die Casting Service,Cnc Machining,Mold Making,Surface Treatment).Any custom Aluminum die casting, magnesium or Zamak/zinc die casting and other castings requirements are welcome to contact us.
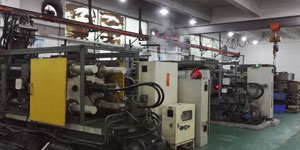
Under the control of ISO9001 and TS 16949,All processes are carried out through hundreds of advanced die casting machines, 5-axis machines, and other facilities, ranging from blasters to Ultra Sonic washing machines.Minghe not only has advanced equipment but also have professional team of experienced engineers,operators and inspectors to make the customer’s design come true.
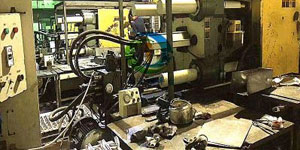
Contract manufacturer of die castings. Capabilities include cold chamber aluminum die casting parts from 0.15 lbs. to 6 lbs., quick change set up, and machining. Value-added services include polishing, vibrating, deburring, shot blasting, painting, plating, coating, assembly, and tooling. Materials worked with include alloys such as 360, 380, 383, and 413.
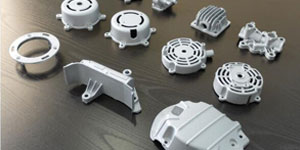
Zinc die casting design assistance/concurrent engineering services. Custom manufacturer of precision zinc die castings. Miniature castings, high pressure die castings, multi-slide mold castings, conventional mold castings, unit die and independent die castings and cavity sealed castings can be manufactured. Castings can be manufactured in lengths and widths up to 24 in. in +/-0.0005 in. tolerance.
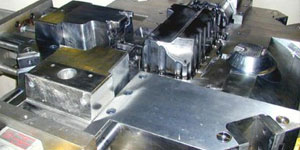
ISO 9001: 2015 certified manufacturer of die cast magnesium, Capabilities include high-pressure magnesium die casting up to 200 ton hot chamber & 3000 ton cold chamber, tooling design, polishing, molding, machining, powder & liquid painting, full QA with CMM capabilities, assembly, packaging & delivery.
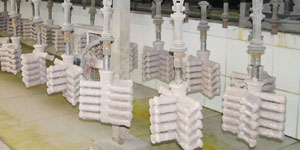
ITAF16949 certified. Additional Casting Service Include investment casting,sand casting,Gravity Casting, Lost Foam Casting,Centrifugal Casting,Vacuum Casting,Permanent Mold Casting,.Capabilities include EDI, engineering assistance, solid modeling and secondary processing.
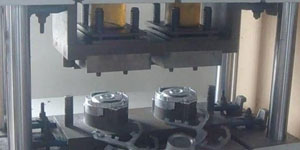
Casting Industries Parts Case Studies for: Cars, Bikes, Aircraft, Musical instruments, Watercraft, Optical devices, Sensors, Models, Electronic devices, Enclosures, Clocks, Machinery, Engines, Furniture, Jewelry, Jigs, Telecom, Lighting, Medical devices, Photographic devices, Robots, Sculptures, Sound equipment, Sporting equipment, Tooling, Toys and more.
What Can we help you do next?
∇ Go To Homepage For Die Casting China
→Casting Parts-Find out what we have done.
→Ralated Tips About Die Casting Services
By Minghe Die Casting Manufacturer |Categories: Helpful Articles |Material Tags: Aluminum Casting, Zinc Casting, Magnesium Casting, Titanium Casting, Stainless Steel Casting, Brass Casting,Bronze Casting,Casting Video,Company History,Aluminum Die Casting |Comments Off