Where Are Aluminum Alloy Parts Used In Automobiles?
At present, the United States, Japan, and Germany are the countries that use the most aluminum alloys for automobiles. For example, the Audi A8 and A2 of Volkswagen in Germany and the NXS of Japan use 80% of aluminum alloys for the body. Except for the aluminum alloy used by Shanghai Santana, FAW Audi and Jetta (all of which are imported production lines), my country's automobiles have more red flags, about 80-100kg. Some data show that replacing the traditional steel structure with aluminum alloy structure can reduce the quality of automobiles by 30%-40%, manufacturing engines can reduce 30%, and manufacturing wheels can reduce 50%. The use of aluminum alloys is one of the important ways for automobiles to be lightweight, environmentally friendly, energy-saving, speed-up and efficient in transportation. Therefore, research and development of aluminum alloy cars is now very necessary. The main advantages of aluminum alloy are light weight and good heat dissipation. With the development of engine technology, valve structure has become the mainstream design trend of engines.
Compared with a two-valve engine, a cylinder head with four valves per cylinder generates more heat than a cylinder head with two valves per cylinder. Using an all-aluminum alloy cylinder head is the best solution. At present, not only the piston, radiator, oil pan and cylinder block of car engine parts are made of aluminum alloy, but also the cylinder head and crankshaft
The box also uses this material. Under the current situation, it has become a mainstream trend to use aluminum alloy instead of cast iron in engines. The aluminum cylinder liner of French cars has reached 100%, and the aluminum cylinder block has reached 45%. In the next few years, with the successful development of high-strength and high-quality aluminum alloy materials and the continuous improvement of manufacturing processes, aluminum alloy materials will be more and more used to manufacture this type of parts. Aluminum alloys for automobiles can be divided into cast aluminum alloys and deformed aluminum alloys. Cast aluminum alloys are the most used in automobiles, accounting for more than 80%, which are divided into gravity castings, low-pressure castings and other special casting parts. Deformed aluminum alloys include plates, foils, extruded materials, forgings, etc. Although there are certain differences in the variety and composition of industrial aluminum alloy materials in various countries in the world, they are generally the same. Its variety composition: castings account for about 80%, forgings account for 1% to 3%, and the rest are processed materials. Wrought aluminum alloy accounts for a large proportion of the US automobile industry, reaching 36%.
The Application Of Casting Aluminum Alloy
Cast aluminum alloy has excellent casting properties. The suitable alloy and suitable casting method can be selected according to the requirements of the purpose of use, the shape of the part, the dimensional accuracy, the quantity, the quality standard, the mechanical performance and the economic benefits. Cast aluminum alloy is mainly used for casting engine cylinder blocks, clutch housings, rear axle housings, steering gear housings, transmissions, valve trains, oil pumps, water pumps, rocker covers, wheels, engine frames, brake calipers, cylinders and Non-engine components such as brake discs.
Aluminum Alloy For Engine
The aluminum alloy used in automobile engines is the most lightweight, generally reducing weight by more than 30%. In addition, the cylinder block and cylinder head of the engine require the material to have good thermal conductivity and strong corrosion resistance, and aluminum alloy has outstanding characteristics in these aspects. Therefore, various automobile manufacturers have carried out research and development of engine aluminum. At present, many foreign automobile companies have adopted all-aluminum engine cylinder blocks and cylinder heads. For example, General Motors in the United States has adopted all-aluminum cylinder liners; French automobile company aluminum cylinder liners have reached 100%, and aluminum cylinder blocks have reached 45%; Japanese Nissan VQ and Toyota’s Lexus IMZ-FEV6 have adopted cast aluminum engine oil. Bottom shell; Chrysler's new V6 engine cylinder block and cylinder head are made of aluminum alloy materials.
The German Volkswagen’s advanced 6.0L W12 engine is basically made of aluminum-magnesium alloy. The Audi A8L 6.0 quattro sedan adopts the W12 engine, which reduces the vehicle weight to 1980kg, which is lower than all other models. The W12 engine has 450 horsepower and 560Nm of strong power, so that its unit horsepower needs to accelerate the weight of only 4.7kg, which is comparable to high-performance sports cars.
The Polaris series engine is GM's top-notch engine except for the LS engine series. It is the first V8 aluminum alloy engine with overhead camshafts in the United States. Its cylinder liner is made of all aluminum alloy die-casting. The 4.6-liter engine currently widely used in Cadillac has a maximum power of 320 horsepower and a maximum torque of 427Nm. The supercharged models used in the high-performance V series can even reach 476 horsepower/606Nm.
Aluminum Alloy For Wheel Hub
Aluminum wheels are gradually replacing steel wheels because of their light weight, good heat dissipation, and good appearance. In the past 10 years, the global aluminum alloy automobile wheels have grown at an annual growth rate of 7.6%. According to analysis, by 2010, the aluminization rate of automobile wheels will reach 72% to 78%. A365 is a cast aluminum alloy, which has good casting properties and high comprehensive mechanical properties. Cast aluminum alloy wheels all over the world are produced by this type of alloy. The Southwest Aluminum Processing Plant of my country and the Japanese Light Metal Co., Ltd. jointly developed A6061 aluminum alloy wheels. Aluminum wheels widely used in automobiles are an example of the application of aluminum alloys to automobiles. Almost all new models use aluminum alloy wheels.
Application of wrought aluminum alloy
Deformed aluminum alloys are mainly used in automobiles to manufacture body panels such as doors and trunks, bumpers, engine hoods, wheel spokes, hub covers, wheel exterior covers, protective covers for brake assemblies, muffler covers, and anti-lock brakes. Structural parts such as brake systems, heat exchangers, body frames, seats, and floor panels, as well as decorative parts such as dashboards.
Aluminum Alloy For Body Panels
The application proportion of plates in cars continues to rise. For example, 6000 series (AI-Mg-Si series) aluminum alloy plates that have been heat-treated (such as T4, T6, T8) can well meet the requirements of automobiles for shells. Make body frame materials. The body sheet metal parts of Audi A8 adopt this series of alloy aluminum materials. In addition, 2000 series (AI-Cu-Mg series), 5000 series (AI-Mg series) and 7000 series (AI-Mg-Zn-Cu series) aluminum alloys can also be applied to body materials. In recent years, 6000 series and 7000 series high-strength aluminum alloys have been used to develop thin plates and hollow profiles in the shape of "口", "日", "目" "田", which are not only light in weight, high in strength, and good in crack resistance. , And good molding performance, has been widely used in automobiles.
Other Aluminum Alloy Structural Parts
Aluminum alloy is also widely used in other parts of the car, such as: General Motors uses 7021 aluminum sheet to make Smure car bumper reinforcement bracket, Ford uses 7021 aluminum sheet to make Lincoln Town car bumper reinforcement bracket. Aluminum alloy materials are also applied to automobile suspension parts, which effectively reduce the quality of corresponding parts and improve the smoothness and stability of automobile driving, such as disc brake jaws and power transmission frames produced from 6061 forgings. In addition, aluminum alloys are also widely used in automotive air conditioning systems. For example, Japan uses 6595 aluminum alloy for automotive radiators and refrigerator radiators.
The Application Of New Aluminum Alloys In Automobiles
Rapid Solidification Aluminum Alloy
Under the condition of rapid solidification (cooling rate of 104~109℃/S), the material will cause some new features in the structure: ultra-fine microstructure; increase the solid solubility limit of the alloy; the composition is highly uniform, less segregated or no Segregation; formation of new metastable equivalence. Based on these characteristics, rapid solidification aluminum alloys will inevitably be used in the automotive industry. Sumitomo Electric Company uses rapidly solidified PM AI-Si-X high-silicon aluminum alloy instead of sintered steel to manufacture automobile air-conditioning compressor rotors and blades in large quantities, reducing the weight of the rotor by 60% and the weight of the entire compressor by 40%; Yamaha Motor Manufacturing Company The rapidly solidified high-silicon aluminum alloy piston is also put on the market. Compared with ordinary cast iron, this piston has a weight reduction of 20%, a life span of 30%, and significantly reduces noise and pollution; Mazda Motor Company uses spray deposition of Al -Si-Fe-Cu-Mg alloy makes a new type of engine rotor, which improves engine efficiency and can save fuel by 20%.
Aluminum Matrix Composite
Ceramic fibers, whiskers, particles, etc. are used as reinforcing materials to produce aluminum-based composite materials. The specific strength, specific elastic modulus, heat resistance, wear resistance, etc. are greatly improved, and they can be used as engine parts, such as powder metallurgy. The successfully developed Al-Si alloy pistons reinforced by Al2O3 or SiC particles (whiskers) can further improve the strength, wear resistance, heat resistance and fatigue resistance of the piston while retaining the advantages of Al-Si alloy pistons. Used in automobile engines; in addition, particle-reinforced aluminum-based composite materials can also be used to manufacture cylinder blocks, pistons and connecting rods of vehicle engines.
Foam Aluminum Alloy
Aluminum foam is a porous material with numerous bubbles distributed in the metal matrix. This material has a lighter weight, higher strength-to-weight ratio, and has high energy absorption characteristics, high damping characteristics and vibration absorption characteristics. The sandwich panel made by filling foam aluminum between two high-strength outer panels can increase rigidity, lighten weight and improve thermal insulation performance when used in the car body roof panel. It is used in bumpers, longitudinal beams and some pillar parts. It can increase the impact energy absorption capacity when it is up, and it improves the impact safety while reducing the weight.
Development Prospects Of Aluminum Alloy In Automobiles
Among the lightweight metals, although the density of magnesium alloy is smaller than that of aluminum alloy, the cost of magnesium ingot is higher, and there are many technical obstacles in the manufacturing process of parts, such as lack of high-temperature die-casting alloy and design data, poor surface treatment technology, and low level of bonding Therefore, the current use in automobiles is quite limited; while titanium alloys used in aerospace have high mechanical strength, but the manufacturing process is difficult and the manufacturing cost is expensive, which makes titanium alloys unable to be used in automobile production in large quantities. Aluminum alloy has good comprehensive performance in terms of cost, manufacturing technology, mechanical properties, sustainable development (the most aluminum content in the earth's crust, accounting for 8.1%) and other aspects. Therefore, aluminum alloy is the preferred light metal material in the automotive industry now and in the future.
Every 1 kg of aluminum used in a car can reduce its own weight by 2.25 kg, with a weight reduction effect of up to 125%, and can reduce exhaust emissions by 20 kg during the entire life cycle of the car. In addition, aluminum recycling is simple, except for steel. It can be seen from the above table that every 1 kg of aluminum used in a car can reduce its own weight by 2.25 kg, with a weight reduction effect of up to 125%, and can reduce exhaust emissions during the entire life cycle of the car. kg. In addition, aluminum is easy to recycle, and it is a material that can be recycled to the maximum extent except for steel. Almost 90% of aluminum used in automobiles can be recycled and recycled. Aluminum has good physical and chemical properties. It can be applied to the casting, forging and punching processes in industrial production. It is one of the few metal materials that can be used to manufacture parts by a variety of casting processes. It is most suitable for a wide range of pressure casting processes. . However, the cost of aluminum alloy is still higher than that of steel materials. Recycled materials, almost 90% of automotive aluminum can be recovered and recycled. Aluminum has good physical and chemical properties. It can be applied to the casting, forging and punching processes in industrial production. It is one of the few metal materials that can be used to manufacture parts by a variety of casting processes. It is most suitable for a wide range of pressure casting processes. . However, the cost of aluminum alloy is still higher than that of steel materials. The weight of the car body is about 30% of the total weight of the car, so the lightweight of the car body plays an important role. On the inner and outer panels of the car
Using aluminum alloy plates instead of steel plates can reduce the weight of the body by about 40%-50%; if the aluminum alloy covering parts are used to reduce the weight of the whole vehicle by 10%-15%, it can be seen that the weight reduction effect of using aluminum alloy body plates is very significant. Aluminum alloy provides a good application foundation and market prospects in automotive lightweight applications, which will inevitably bring greater opportunities for the application of aluminum alloy automotive panels. Therefore, the use of aluminum alloy plates to replace steel plates to manufacture body panels is also an inevitable way to reduce the weight of automobiles. The entire body of the German Audi A8 premium sedan is made of aluminum, the frame is a three-dimensional frame structure, and the cover is stamped from aluminum. Compared with the steel body, this kind of aluminum body has a 30-50% reduction in mass and a 5-8% reduction in fuel consumption.
At present, my country's automobile production volume ranks fourth in the world after the United States, Japan, and Germany. In terms of auto aluminization rate, my country's technology is still relatively backward. At present, the use of aluminum in automobiles in developed countries has reached 138kg, and the aluminization rate has reached 12%. However, the use of aluminum in automobiles in my country is far behind foreign countries. The average aluminum consumption is only 60kg, and the aluminization rate is less than 5%. Therefore, the development prospect of my country's automotive aluminum alloy market is very broad.
Four Major Obstacles To The Application Of Aluminum Alloys
Expanding the application of aluminum alloy in automobiles will produce huge economic and social benefits, but there are still the following urgent solutions:
- The performance of aluminum alloy sheet needs to be improved
- Establish a database of aluminum alloys for automobiles
- Development of design methods, structural calculation methods, and forming processes for aluminum alloy parts
- Computer simulation and welding process method
- Study the surface morphology of aluminum alloy materials, pretreatment before painting, and prevention after painting.
- Corrosion effects and other issues, the accumulated data provides basic data for the formulation of the process for aluminum alloy application
- The repair market lacks experience and methods for the restoration and recovery principles of aluminum alloy structural parts and covering parts after collision, and repair welding after cracking.
Please keep the source and address of this article for reprinting: Where Are Aluminum Alloy Parts Used In Automobiles?
Minghe Die Casting Company are dedicated to manufacture and provide quality and high performance Casting Parts(metal die casting parts range mainly include Thin-Wall Die Casting,Hot Chamber Die Casting,Cold Chamber Die Casting),Round Service(Die Casting Service,Cnc Machining,Mold Making,Surface Treatment).Any custom Aluminum die casting, magnesium or Zamak/zinc die casting and other castings requirements are welcome to contact us.
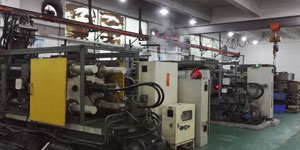
Under the control of ISO9001 and TS 16949,All processes are carried out through hundreds of advanced die casting machines, 5-axis machines, and other facilities, ranging from blasters to Ultra Sonic washing machines.Minghe not only has advanced equipment but also have professional team of experienced engineers,operators and inspectors to make the customer’s design come true.
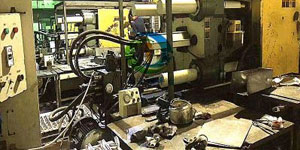
Contract manufacturer of die castings. Capabilities include cold chamber aluminum die casting parts from 0.15 lbs. to 6 lbs., quick change set up, and machining. Value-added services include polishing, vibrating, deburring, shot blasting, painting, plating, coating, assembly, and tooling. Materials worked with include alloys such as 360, 380, 383, and 413.
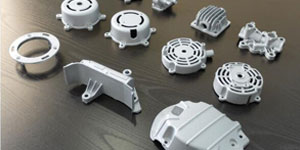
Zinc die casting design assistance/concurrent engineering services. Custom manufacturer of precision zinc die castings. Miniature castings, high pressure die castings, multi-slide mold castings, conventional mold castings, unit die and independent die castings and cavity sealed castings can be manufactured. Castings can be manufactured in lengths and widths up to 24 in. in +/-0.0005 in. tolerance.
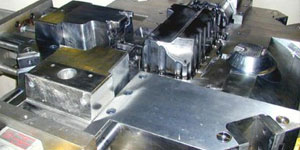
ISO 9001: 2015 certified manufacturer of die cast magnesium, Capabilities include high-pressure magnesium die casting up to 200 ton hot chamber & 3000 ton cold chamber, tooling design, polishing, molding, machining, powder & liquid painting, full QA with CMM capabilities, assembly, packaging & delivery.
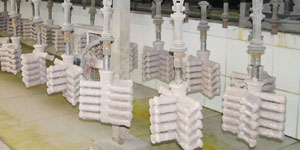
ITAF16949 certified. Additional Casting Service Include investment casting,sand casting,Gravity Casting, Lost Foam Casting,Centrifugal Casting,Vacuum Casting,Permanent Mold Casting,.Capabilities include EDI, engineering assistance, solid modeling and secondary processing.
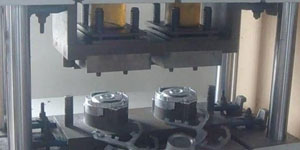
Casting Industries Parts Case Studies for: Cars, Bikes, Aircraft, Musical instruments, Watercraft, Optical devices, Sensors, Models, Electronic devices, Enclosures, Clocks, Machinery, Engines, Furniture, Jewelry, Jigs, Telecom, Lighting, Medical devices, Photographic devices, Robots, Sculptures, Sound equipment, Sporting equipment, Tooling, Toys and more.
What Can we help you do next?
∇ Go To Homepage For Die Casting China
→Casting Parts-Find out what we have done.
→Ralated Tips About Die Casting Services
By Minghe Die Casting Manufacturer |Categories: Helpful Articles |Material Tags: Aluminum Casting, Zinc Casting, Magnesium Casting, Titanium Casting, Stainless Steel Casting, Brass Casting,Bronze Casting,Casting Video,Company History,Aluminum Die Casting |Comments Off