Led Display Cabint
LED DISPLAY CABINT Solutions By Casting &Cnc Machining
IATF 16949 CERTIFIED CAST MANUFACTURING AND CNC MACHINING FOR LED DISPLAY CABINT
The LED display is a flat panel display, composed of small LED module panels, used to display text, images, videos and other information equipment. LED electronic display screen integrates microelectronic technology, computer technology, and information processing. It has the advantages of bright colors, wide dynamic range, high brightness, long life, stable and reliable work. LED displays are widely used in commercial media, cultural performance markets, stadiums, information dissemination, press releases, securities trading, etc., to meet the needs of different environments.
The shell of the LED display cabint is manufactured by a die-casting process.
Minghe provides all customized size solution for diverse requiments. We can offer draft drawing for your rough idea and make optmized solution for you with reasonable cost.
For your creative thoughts, we have strong developing ability to make a unique LED display die casting enclosure for you. We ensure your OEM, ODM cooperation complete in the fastest pre-planing and drawing draft, high quality, good price and quick delivery.
For your special installation, we also give you best enclosure die casting custom solution to make installation easy. Considering the cost, we can offer the most optimized solution for every clients.
On every project, we come up with custom solutions, with designers, consultants to make creative LED displays enclosure for special environment . Our R&D team, with their 35 years' rich experience, help you to create unique and unforgettable experience

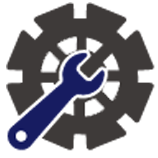
Contact our LED DISPLAY CABINT engineer today to discuss the specifics of your complex projects.
1.Commonly LED DISPLAY CABINT Applications.
MINGHE’s experience is unrivaled in the design, development, and manufacture of precision die cast and cnc machining solutions for a wide range of LED DISPLAY CABINT applications, including but not limited to:
- LED Digital DISPLAY CABINT
- LED Dot Matrix Graphic DISPLAY CABINT
- Indoor DISPLAY CABINT
- Outdoor DISPLAY CABINT
- Synchronous LED DISPLAY CABINT
- Asynchronous LED DISPLAY CABINT
2.Why Choose Us For Your DISPLAY CABINT Projects
Minghe has over 30 years of experience assisting display cabint manufacturers design cost-effective mechanical components. When you partner with Minghe you can receive the following benefits from our die casting process:
- Minghe’s die casting operation features 40 presses ranging from 250 to 3000 ton. We accommodate some of the most demanding display cabint runs in terms of volume, part size, and complexity. Because of our engineering and modeling capabilities, we are known by our clients as a company that can reduce part complexity, and make the manufacturing process more efficient.
- Minghe can help consolidate your supply chain by offering the complete package of die casting services in addition to engineering support, mold design and troubleshooting, machining, and logistics.
- Minghe is an ISO Certified Die Casting Manufacturer and has extensive experience in designing and manufacturing zinc and aluminum parts to display cabint quality specifications.
- With presses ranging from large to small, we have the capability to manufacture heat sink parts of all sizes, from a Indoor screen to Outdoor screen encolsure for led display.
- We are ITAF 16949 certified and can provide part manufacturing for military and telecom applications.
- Our technology facilitates and streamlines production. Our suite of technology includes AutoCAD, Pro-E, MAGMAsoft®, CAD/CAM and EDI compatibility, and FARO Laser Scanning.
3.Other Manufacturing Service For Custom DISPLAY CABINT
In addition, Minghe also provides CNC machining, investment casting, sand casting and other services related to customized DISPLAY CABINT.
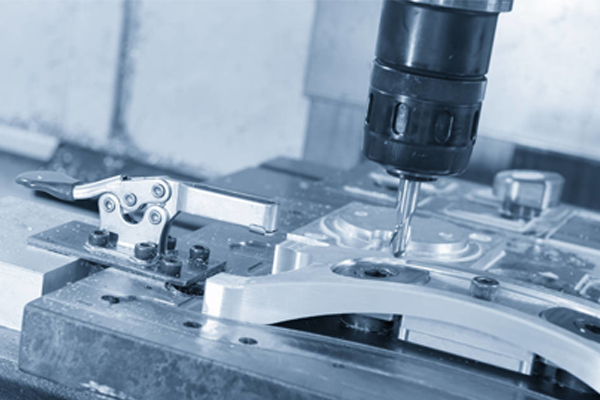
Cnc Machining DISPLAY CABINT |
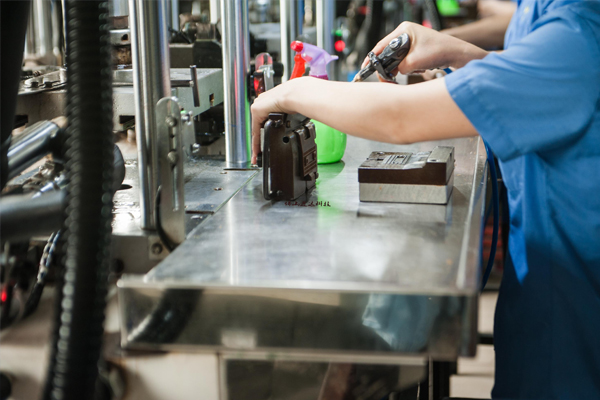
Investment Casting DISPLAY CABINT |
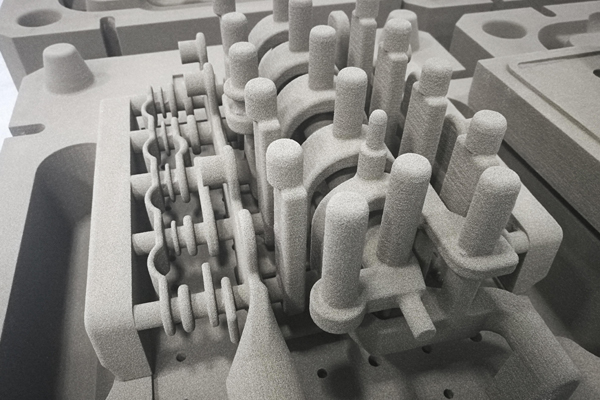
Sand Casting DISPLAY CABINT |
4.Capabilities of Our Precision Manufacturing for DISPLAY CABINT
In addition, Minghe also provides CNC machining, investment casting, sand casting and other services related to customized DISPLAY CABINT.
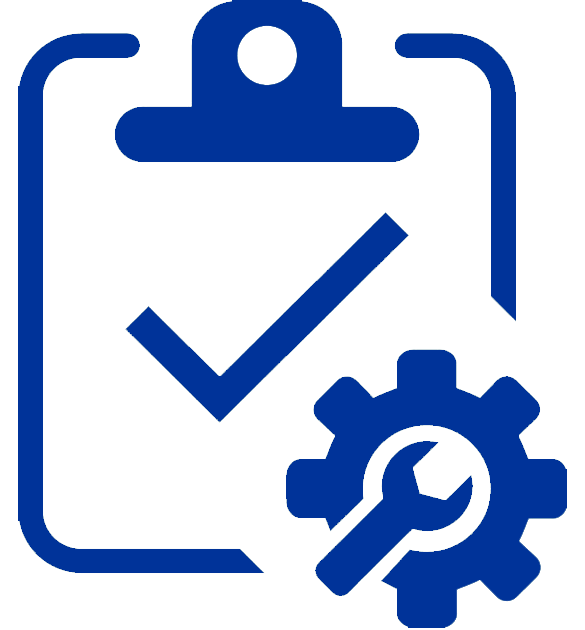
AL360, AL380, AL383, and AL413, ZA-8, ZA-12, ZA-27,Aluminium A356,
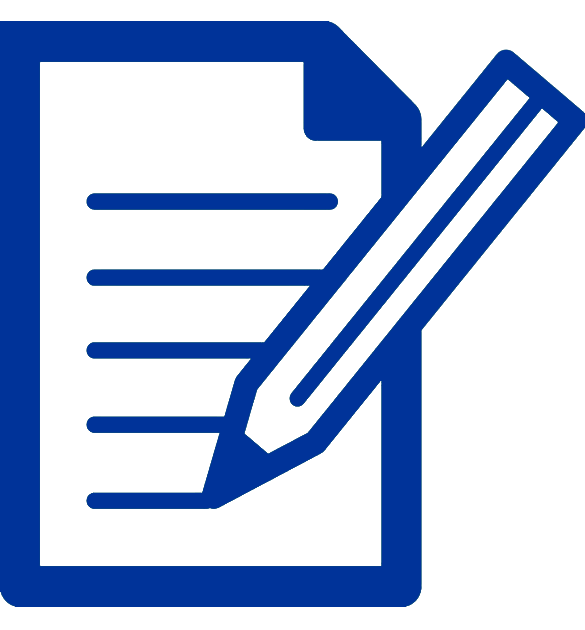
Black, White, Silver, Red, Natural, Blue, Green and different colors as client requirements
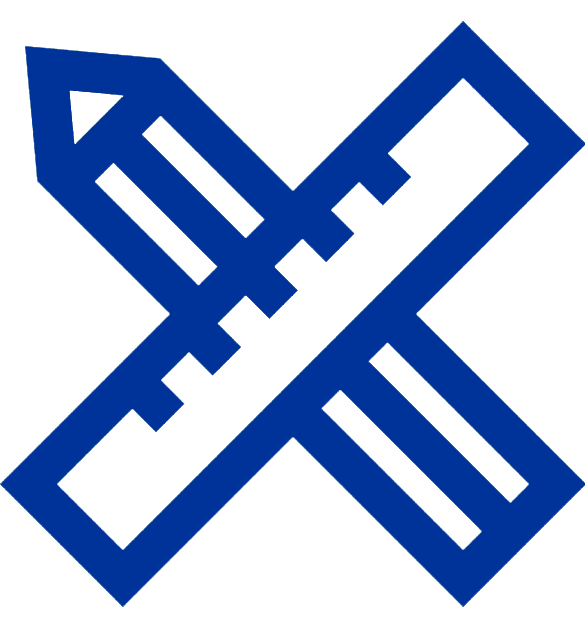
Sand blasting, shot blasting, polishing, anodizing, oxidation, electrophoresis, chromate, powder coating and painting
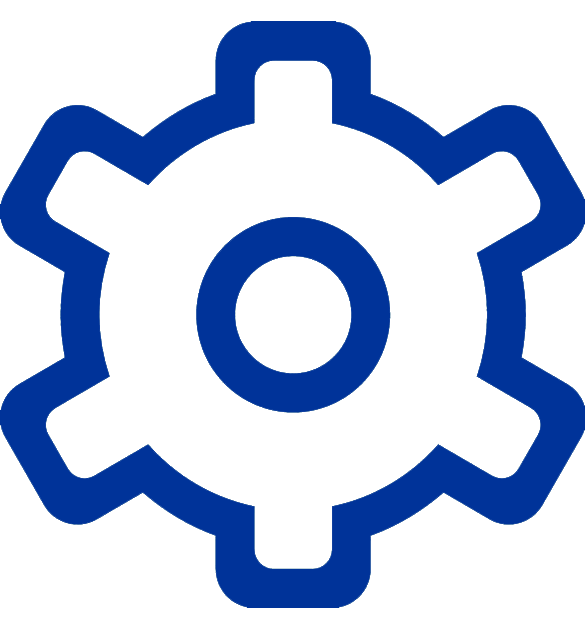
Die Casting,Mold Manufacturing,CNC milling, CNC turning, CNC drilling
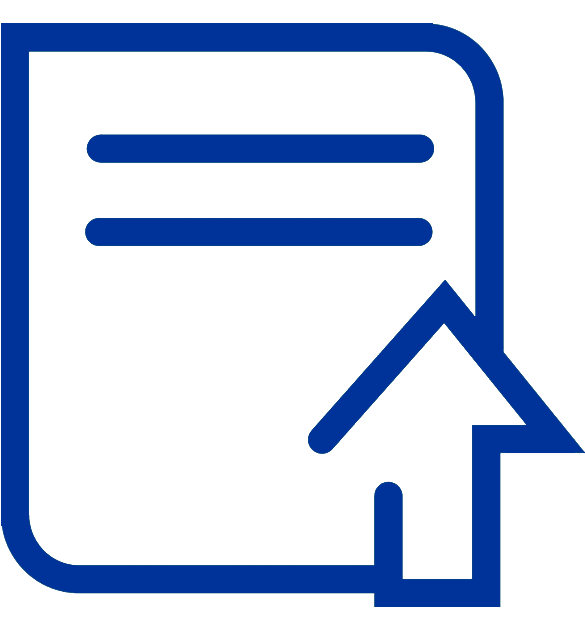
LED Digital DISPLAY CABINT;LED Dot Matrix Graphic DISPLAY CABINT;
The Minghe Case Studies Of Led Display Cabint Casting
You have a complex part design, Minghe Casting Company can help you turn it into a reality. With the right equipment, strong technical knowledge, and a focus on quality.. From tool design to finishing and then on to shipment, Minghe Casting ensure that every project is completed to a high standard and that your orders are delivered on time, every time.








Go To View More Casting Parts Cases Studies >>>
Choose The Best Led Display Cabint Casting Service
Currently, our Led Display Cabint casting parts are exported to America, Canada, Australia, United Kingdom, Germany, France, Sout Africa, and many other countries all over the world. We are ISO9001-2015 registered and also certified by SGS.
Custom china die casting service provides durable and affordable castings that meet your specifications for automotive, medical, aerospace, electronics, food, construction, security, marine, and more industries. Fast to send your inquiry or submit your drawings to get a free quote in the shortest time.Contact us or Email sales@hmminghe.com to see how our people, equipment and tooling can bring the best quality for the best price for your Led Display Cabint casting project.
We Provide Casting Services Include:
Minghe Casting services working with sand casting、metal casting 、investment casting lost foam casting, and more.

Sand Casting
Sand Casting is a traditional casting process that uses sand as the main modeling material to make molds. Gravity casting is generally used for sand molds, and low-pressure casting, centrifugal casting and other processes can also be used when there are special requirements. Sand casting has a wide range of adaptability, small pieces, large pieces, simple pieces, complex pieces, single pieces, and large quantities can be used.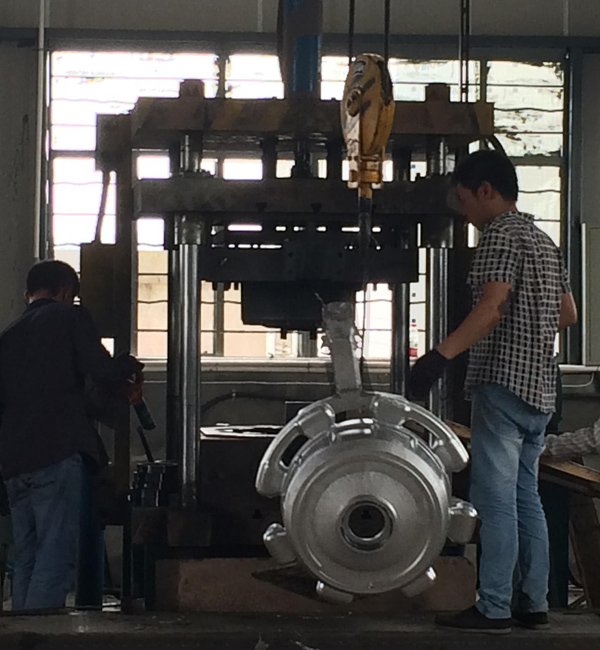
Permanent Mold Casting
Permanent Mold Casting have a long life and high production efficiency, not only have good dimensional accuracy and smooth surface, but also have higher strength than sand castings and are less likely to be damaged when the same molten metal is poured. Therefore, in the mass production of medium and small non-ferrous metal castings, as long as the melting point of the casting material is not too high, metal casting is generally preferred.
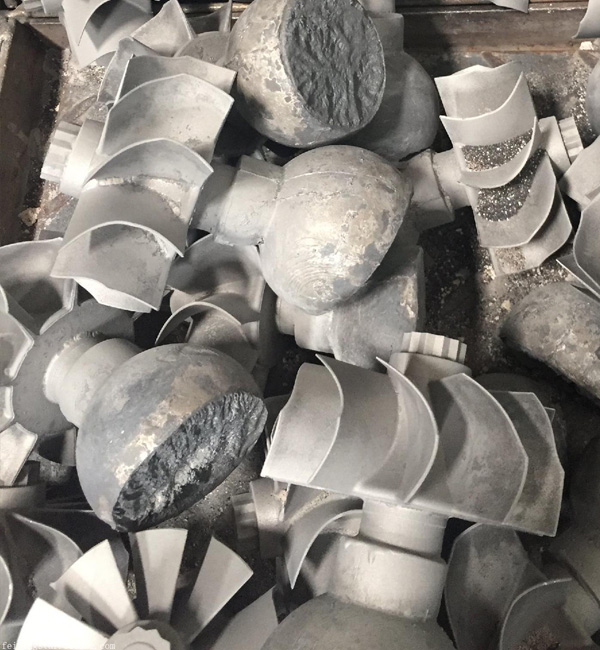
Investment Casting
The biggest advantage of investment casting is that because investment castings have high dimensional accuracy and surface finish, they can reduce machining work, but leave a little machining allowance on the parts with higher requirements. It can be seen that the use of investment casting method can save a lot of machine tool equipment and processing man-hours, and greatly save metal raw materials.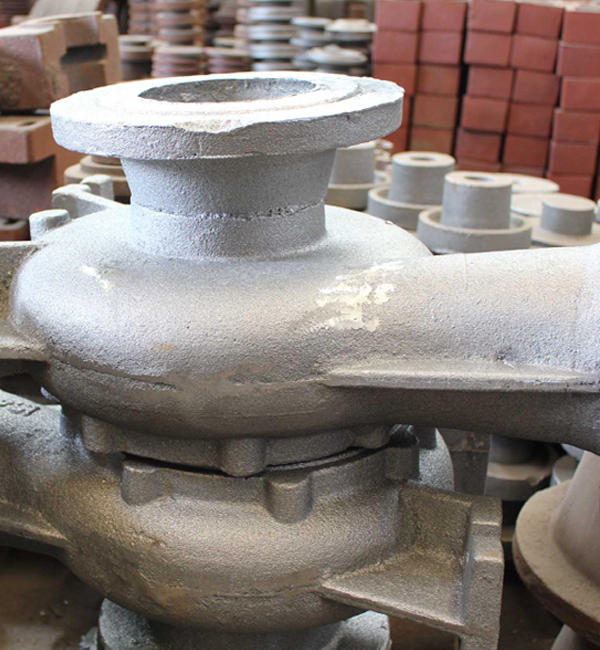
Lost Foam Casting
Lost foam casting is to combine paraffin wax or foam models similar to the casting size and shape into model clusters. After brushing and drying refractory coatings, they are buried in dry quartz sand for vibration modeling, and poured under negative pressure to gasify the model. , The liquid metal occupies the position of the model and forms a new casting method after solidification and cooling.

Die Casting
Die casting is a metal casting process, which is characterized by applying high pressure to the molten metal using the cavity of the mold. Molds are usually made of higher-strength alloys, and this process is somewhat similar to injection molding. Most die castings are iron-free, such as zinc, copper, aluminum, magnesium, lead, tin, and lead-tin alloys and their alloys. Minghe has been China's top die casting service since 1995.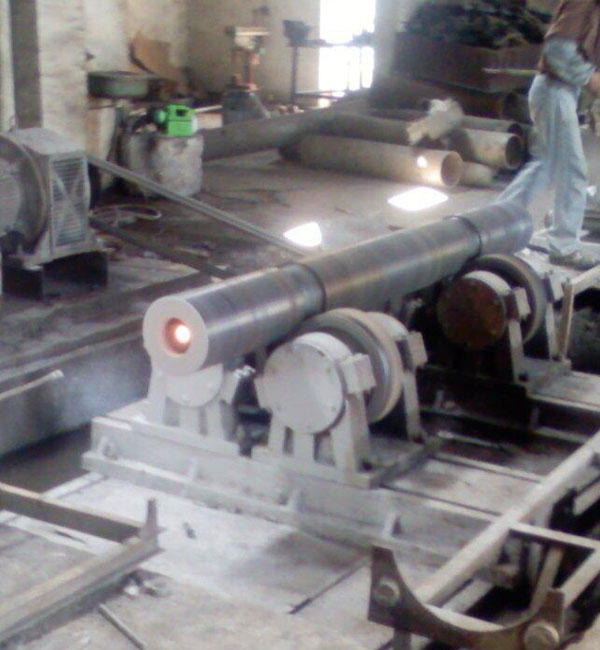
Centrifugal Casting
Centrifugal Casting is a technique and method of injecting liquid metal into a high-speed rotating mold, so that the liquid metal is centrifugal motion to fill the mold and form a casting. Due to the centrifugal movement, the liquid metal can fill the mold well in the radial direction and form the free surface of the casting; it affects the crystallization process of the metal, thereby improving the mechanical and physical properties of the casting.
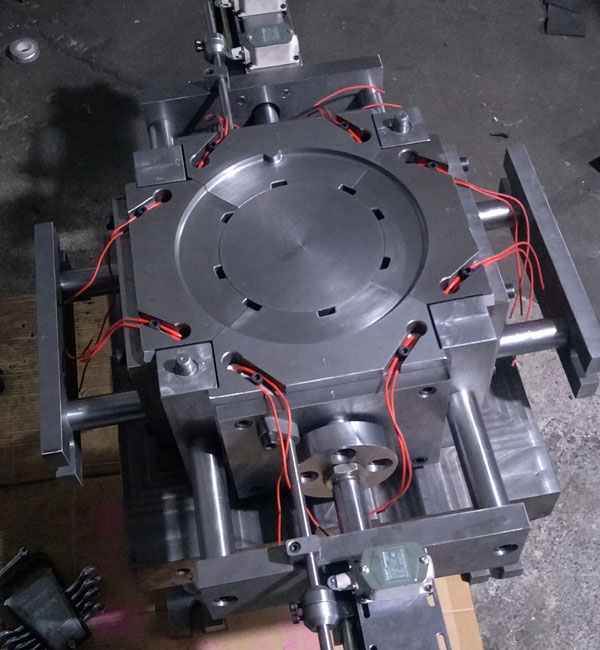
Low Pressure Casting
Low Pressure Casting means that the mold is generally placed above a sealed crucible, and compressed air is introduced into the crucible to cause a low pressure (0.06~0.15MPa) on the surface of the molten metal, so that the molten metal rises from the riser pipe to fill the mold and control Solidified casting method. This casting method has good feeding and dense structure, easy to cast large thin-walled complex castings, no risers, and a metal recovery rate of 95%. No pollution, easy to realize automation.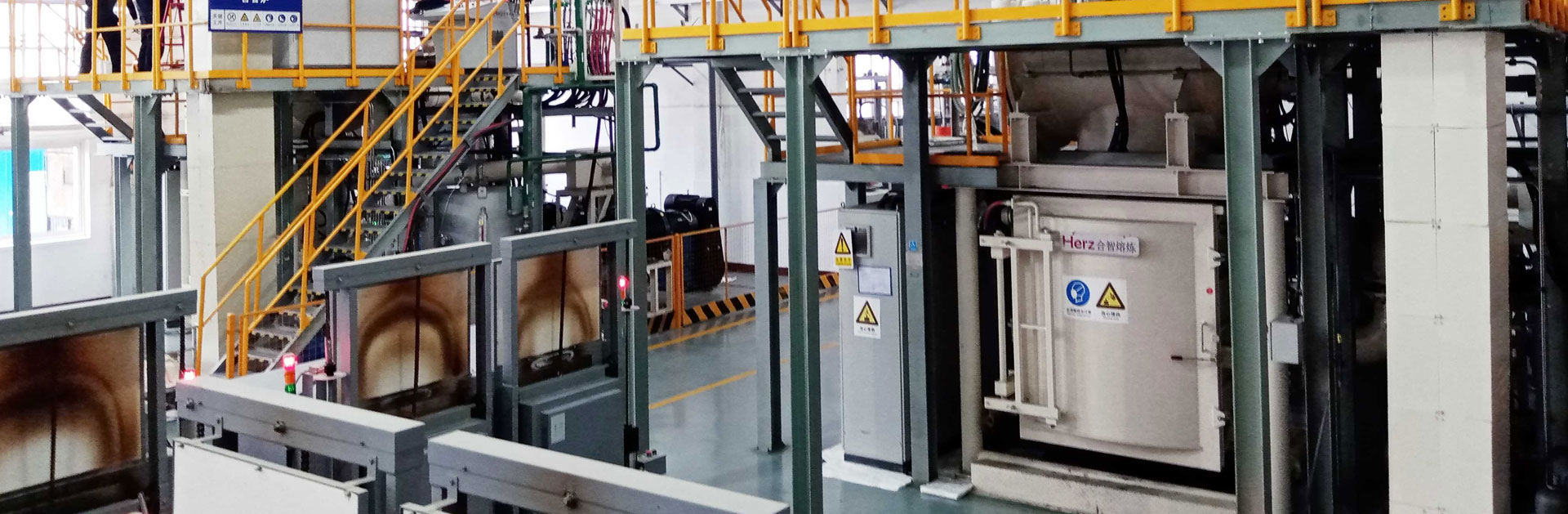