Lost Foam Casting
What is Lost Foam Casting
Lost Foam Casting (also known as Solid Casting) is to combine paraffin wax or foam models similar in size and shape to the castings to form clusters. After brushing and drying refractory coatings, they are buried in dry quartz sand for vibration modeling. It is a new type of casting method that makes the model gasify, liquid metal occupies the position of the model, and solidifies and cools to form a new casting method.
Since the binderless dry sand often collapses during the pouring process, A. Wittemoser in Germany adopted the so-called "magnetic casting" in 1967. In 1971, Nagano of Japan invented the V method (vacuum casting method). Inspired by this, today's lost foam casting also uses vacuum to fix the sand in many places. Therefore, the lost foam casting technology has developed rapidly all over the world in the past 20 years.
The Advantages Of Lost Foam Casting
1. High Casting Precision
Lost foam casting is a new process with almost no margin and precise molding. This process does not require mold taking, no parting surface, no sand core, so the casting has no flash, burr and draft angle, and reduces the core The size error caused by the combination. The surface roughness of the castings can reach Ra3.2 to 12.5μm; the dimensional accuracy of the castings can reach CT7 to 9; the machining allowance is up to 1.5 to 2mm, which can greatly reduce the cost of machining. Compared with the traditional sand casting method, it can be reduced by 40 % To 50% of machining time.
2. Flexible Design
It provides sufficient freedom for the design of casting structure. Highly complex castings can be cast by combining foam plastic molds.It is not only suitable for large castings, mechanized operations, but also for manual splicing models of small batch products.
3. No Sand Core In Traditional Casting
Therefore, there will be no uneven wall thickness of the casting caused by the inaccurate size of the sand core or the inaccurate position of the lower core in the traditional sand casting.
4. Cleaner Production
There is no chemical binder in the molding sand, foam plastic is harmless to the environment at low temperature, and the recovery rate of old sand is more than 95%.
5. Reduce Investment And Production Costs
Reduce the weight of the casting blank, and the machining allowance is small.The dry sand buried model can be reused, with less industrial waste, no burrs, cleaning time can be reduced by more than 80%, and the cost is significantly reduced.
6.Wide Range Of Applications
It can not only cast iron, ductile iron, but also cast steel at the same time, so the transfer is flexible and widely used. It is not only suitable for small and medium-sized parts, but also for large-scale castings, such as machine tools, large-diameter pipe fittings, large-scale cold mold parts, large-scale mining equipment parts, etc.
7. Disadvantages And Limitations
The lost foam casting process is the same as other casting processes, with its shortcomings and limitations. Not all castings are suitable for production using the lost foam process, so a specific analysis is required. Mainly based on the following factors to consider whether to use this process.
- - The batch size of castings: the larger the batch size, the greater the economic benefits.
- - Casting material: the order of good applicability and poor applicability is roughly: gray cast iron-non-ferrous alloy-ordinary carbon steel-ductile iron-low carbon steel and alloy steel; pass the necessary preparations so as not to cause process experiments , The debugging cycle is too long.
- - Casting size: Mainly consider the use range of corresponding equipment (such as vibrating table, sand box).
- - Casting structure: The more complex the casting structure, the more it can reflect the superiority and economic benefits of the lost foam casting process. For the structure with narrow internal cavity channels and interlayers, it is necessary to conduct experiments in advance before using the lost foam process. produce.
Founded in 1995, China Minghe Casting is an industry standard formulation unit for pattern forming molds for lost foam casting. Minghe is located in the world's industrial capital-Dongguan, China. It is a high-tech enterprise in Guangdong Province. It has a production workshop with a construction area of 18,000 square meters. It is equipped with equipment for research and development, design, casting, machining, assembly, and surface treatment. It is the Dongguan R&D center and Technology Center. Minghe Casting now has 6 invention patents and 20 utility model patents. It is a trademark enterprise in Guangdong Province. The company has more than 230 employees, including 36 mold design engineers and 39 technicians; it has 40 CNC processing equipment and general processing equipment. 28 units, 3 coordinate measuring machines, and 1 reverse scanner. Using computer three-dimensional design, programming, computer-aided processing technology, using FM method to cast aluminum mold blanks, combined with Minghe Casting created TEFLON (TEFLON) surface coating technology and subsidiary Minghe Powder Coating Factory, so that mold quality, precision, efficiency, The service life can meet the requirements of customers. The company's technical staff guide the mold assembly, use, trial production, free maintenance, and can provide a full set of lost foam casting technology according to customer needs.
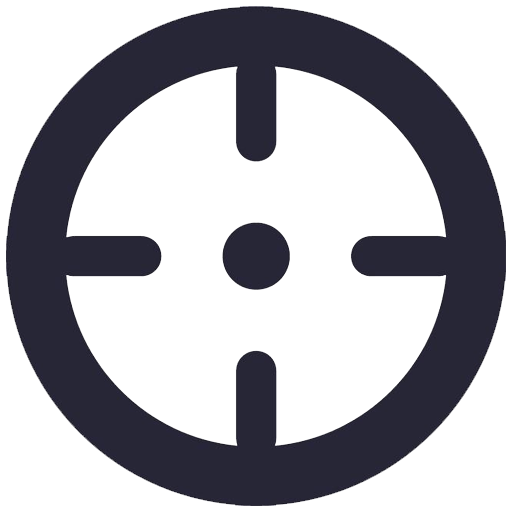
Our Lost Foam Casting Customization Process
Minghe Casting, as a designing unit of pattern forming molds for lost foam casting, produces molds that are widely used. After years of development and innovation, Minghe Casting has become a mold supplier for many lost foam casting companies.The Customization Process of Lost Foam Casting can be summarized as follows:
- – Customer consultation: please contact us for discount.
- – Production plan: We will tailor a mold solution for you.
- – Plan review: The plan will be strictly reviewed by expert engineers.
- – Sign the contract: Sign a cooperation agreement and start preparing products for you.
- – Mold design: 3D design and graphic inspection of parts.
- – CNC machining: CNC machining of aluminum mold blanks.
- – Assembly and testing: mold assembly, testing and test work meet the qualification standards.
- – Pass the test: Test to make sure the product has no problems.
- – Coating treatment: Then carry out the coating treatment of the mold surface.
- – Factory inspection: factory inspection, as well as product packaging and delivery to you.
- – Installation and debugging: mold installation and debugging and after-sales service handover work.
- – Mould delivery: Finally, provide products that satisfy you.
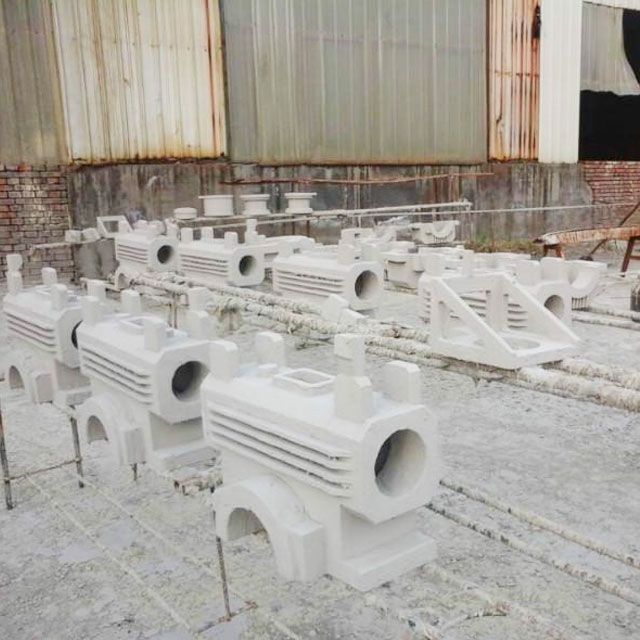
Different Types Production Scenario Of Lost Foam Casting
Minghe always adheres to the customer's requirements and the company's service standards. In any link of mold design, mold assembly, mold debugging, mold trial production, casting process, etc., there are dedicated engineers to keep you on the phone;
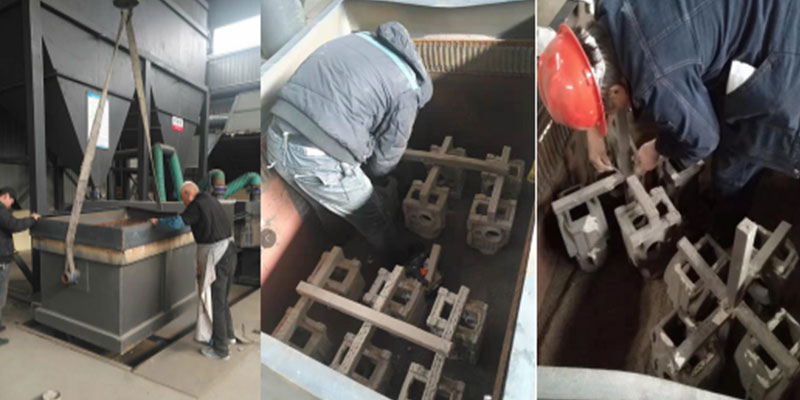
The Scenario Of Manufacturing Lost Foam Casting1 ▶ |
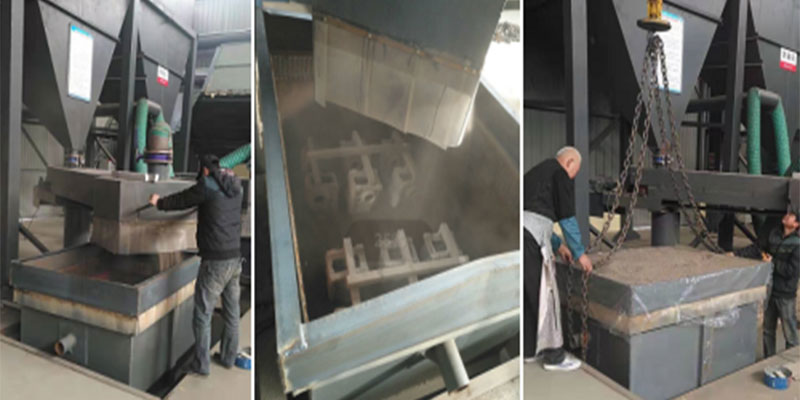
The Scenario Of Manufacturing Lost Foam Casting2 ▶ |
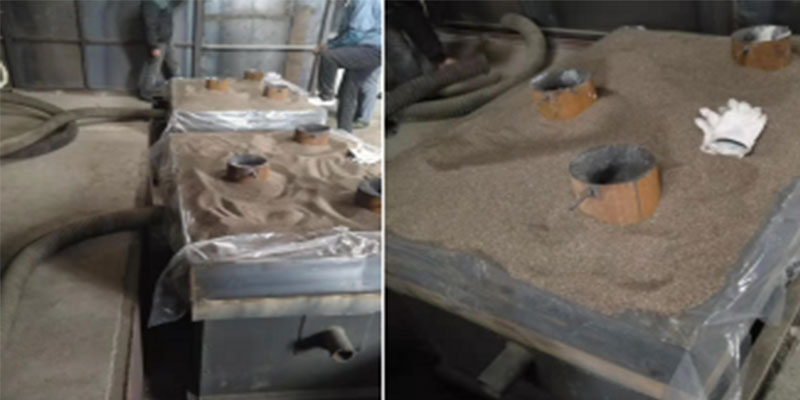
The Scenario Of Manufacturing Lost Foam Casting3 ▶ |
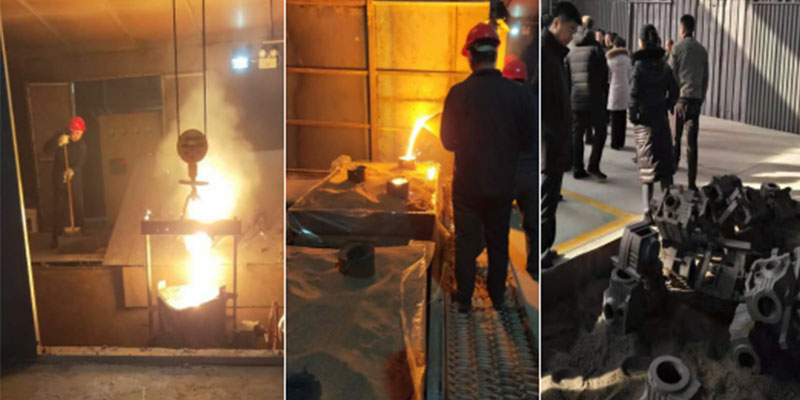
The Scenario Of Manufacturing Lost Foam Casting4▶ |
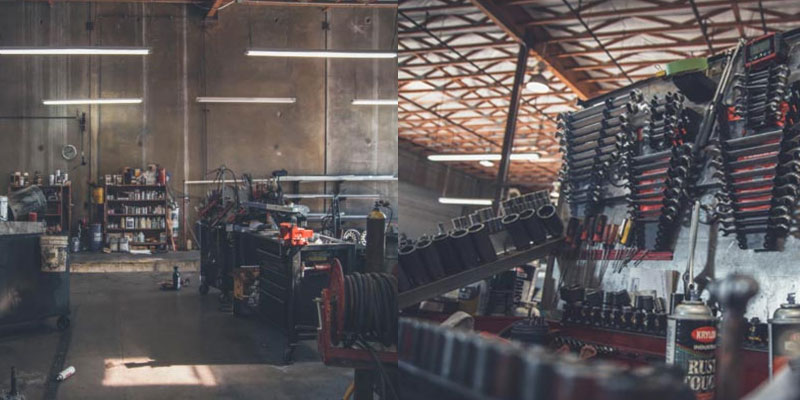
The Scenario Of Manufacturing Lost Foam Casting5▶ |
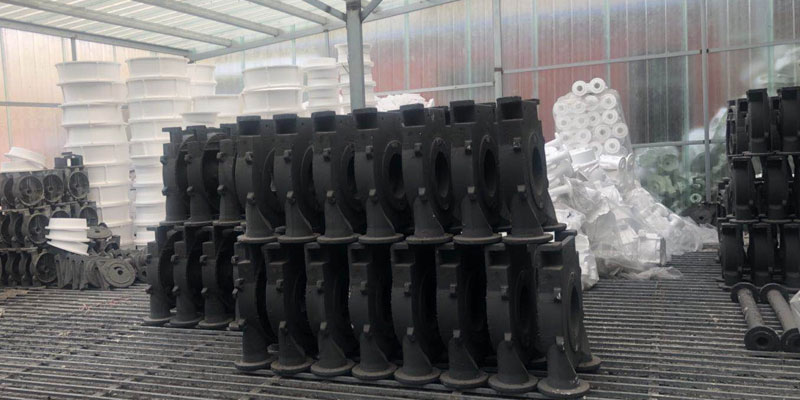
The Scenario Of Manufacturing Lost Foam Casting6▶ |
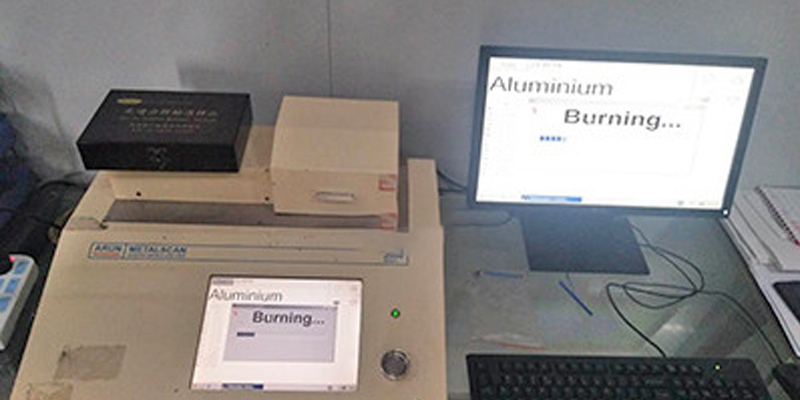
The Scenario Of Manufacturing Lost Foam Casting7 ▶ |
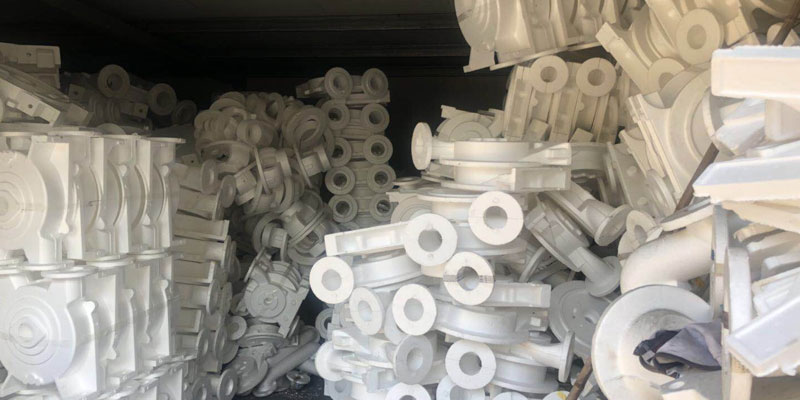
The Scenario Of Manufacturing Lost Foam Casting8▶ |
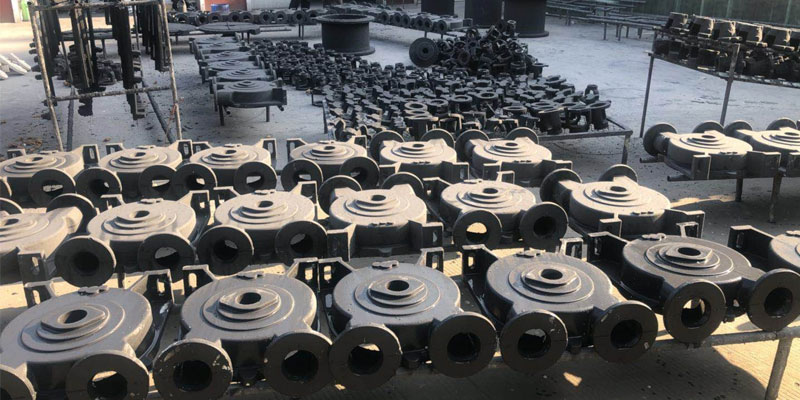
The Scenario Of Manufacturing Lost Foam Casting9 ▶ |
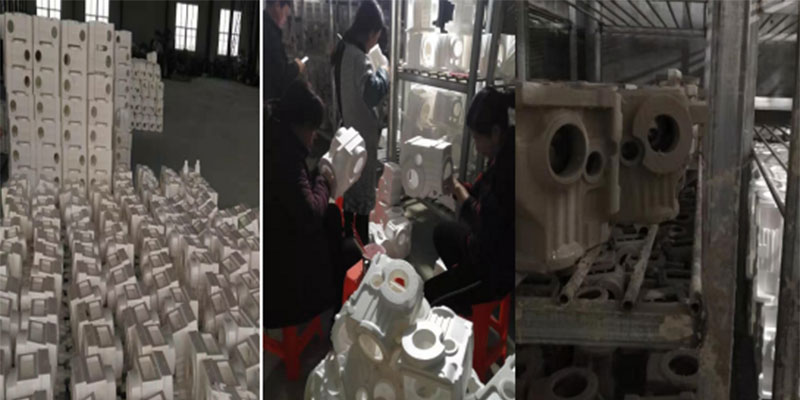
The Scenario Of Manufacturing Lost Foam Casting10▶ |
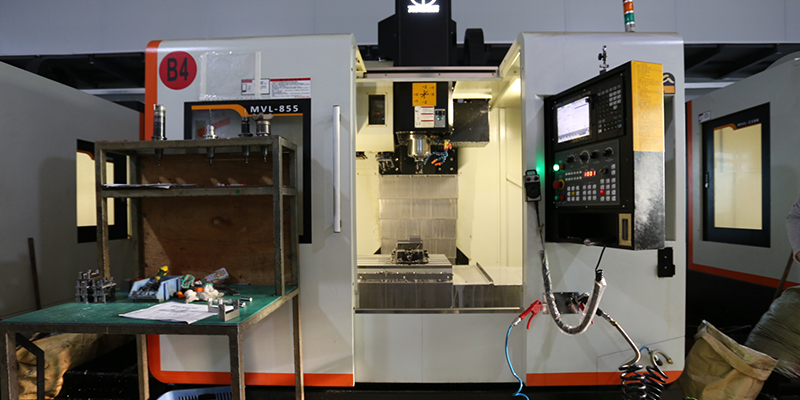
The Scenario Of Manufacturing Lost Foam Casting11 ▶ |
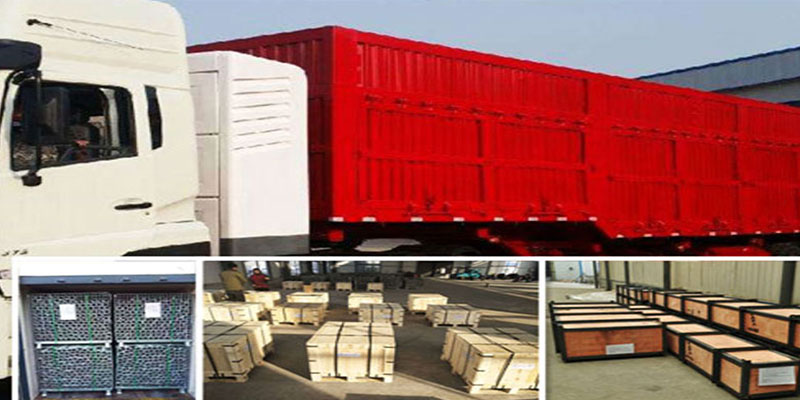
The Scenario Of Manufacturing Lost Foam Casting12▶ |
The Minghe Case Studies Of Lost Foam Casting
Minghe Casting fabrication services are available for both design to reality and low to high volume production runs of your die casting parts,sand casting parts,investment casting parts,metal casting parts, lost foam casting parts and more.
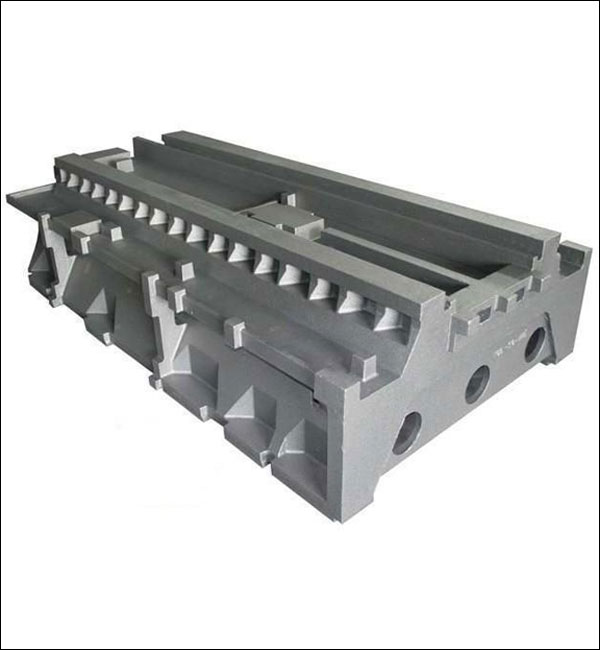
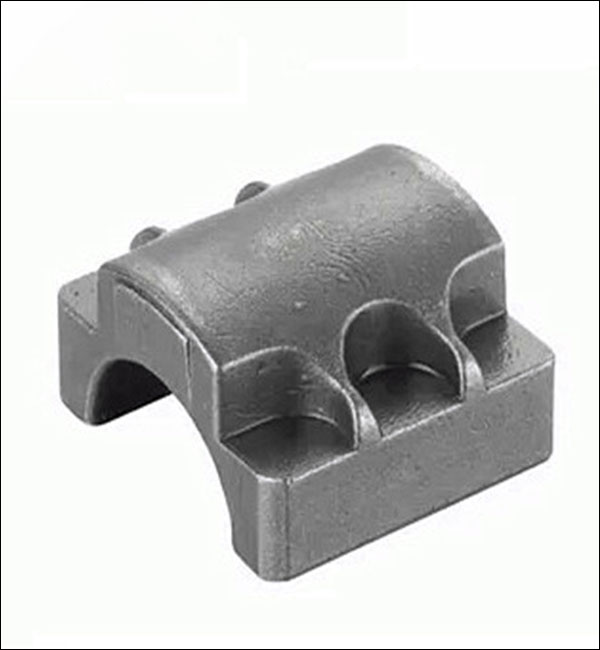
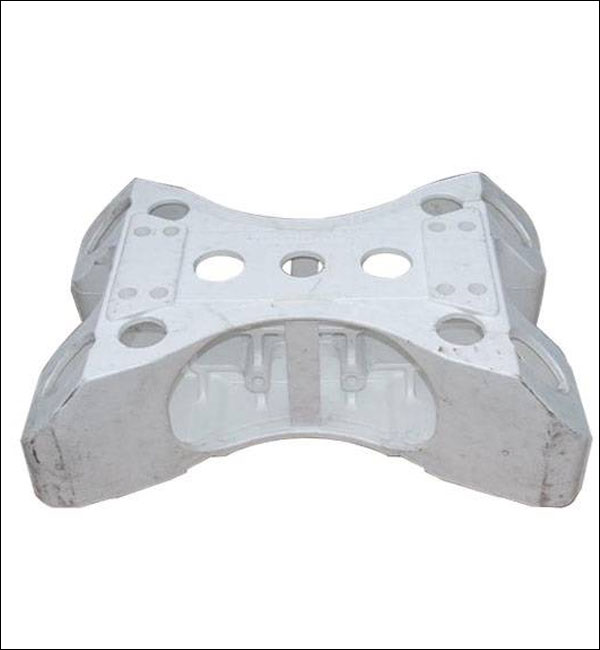
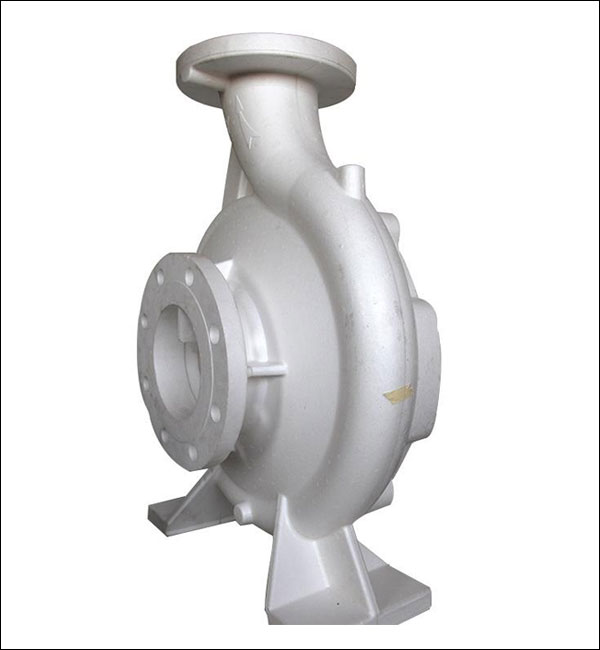
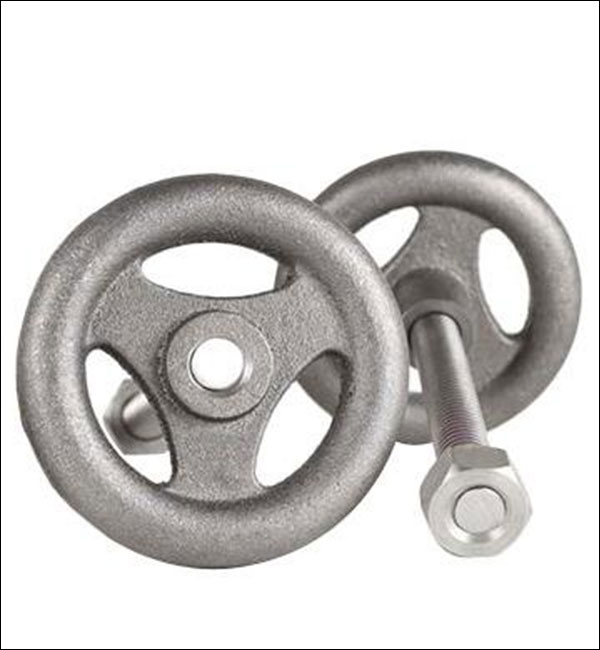
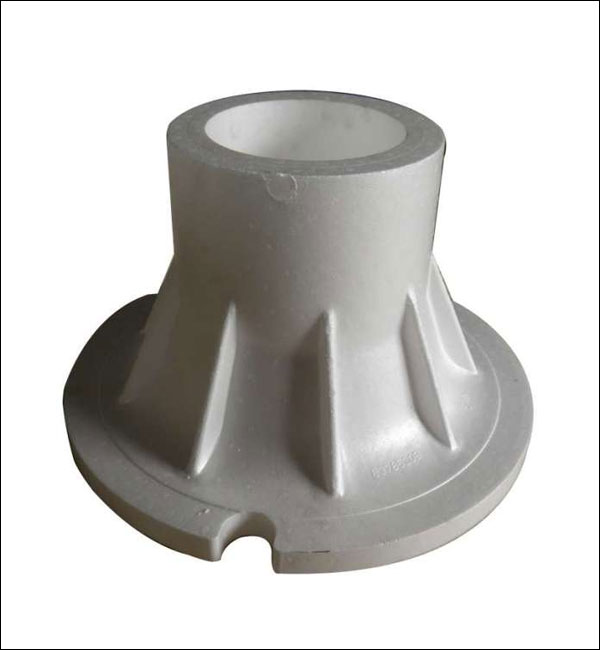
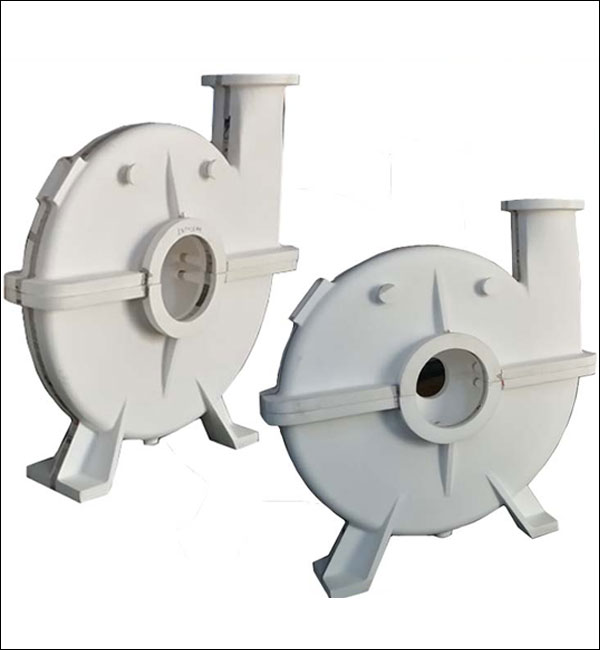
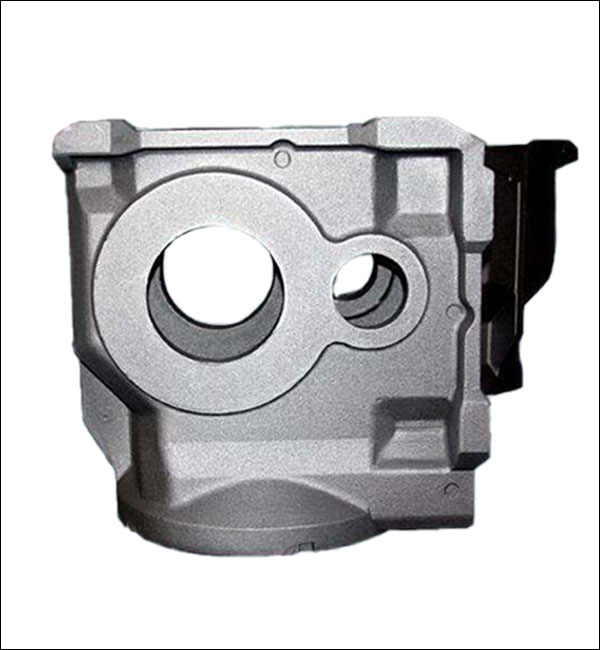
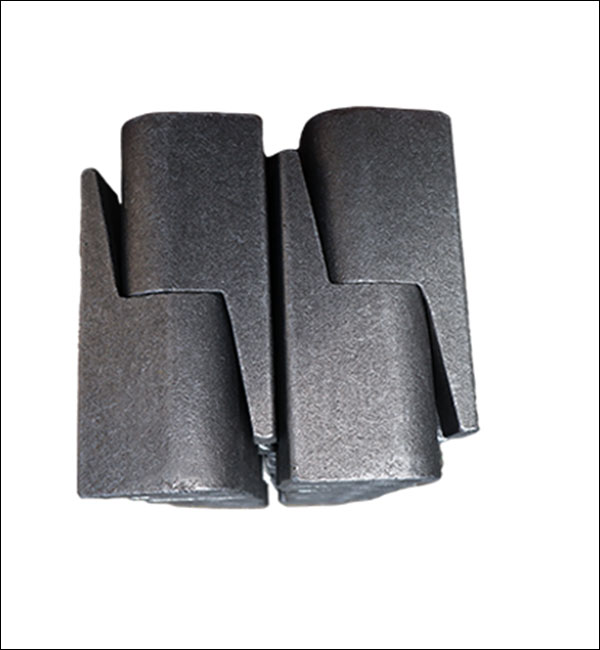
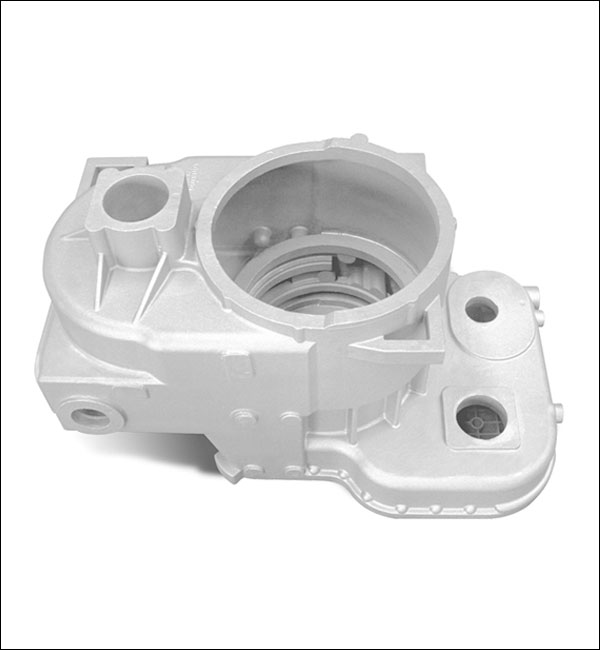
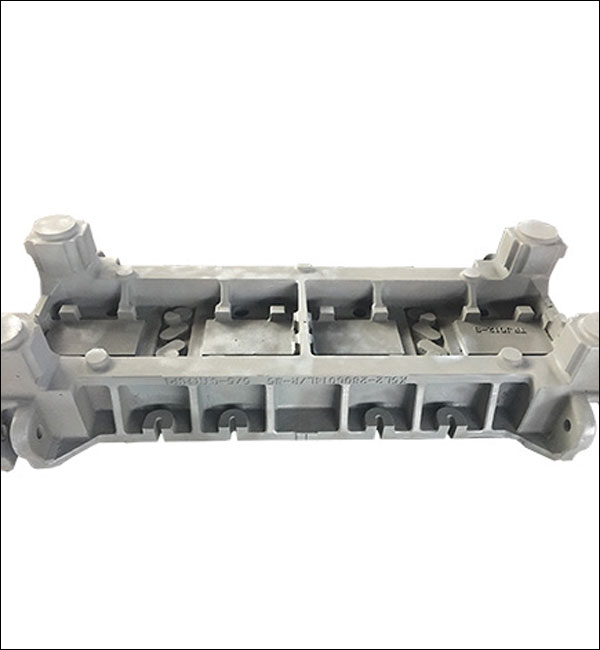
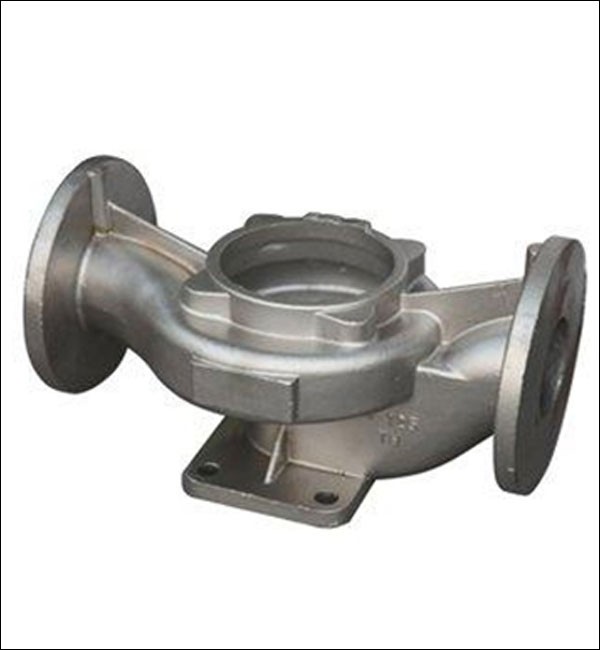
Go To View More Casting Parts Cases Studies >>>
Choose the Best Lost Foam Casting Supplier
Currently, our lost foam casting parts are exported to America, Canada, Australia, United Kingdom, Germany, France, Sout Africa, and many other countries all over the world. We are ISO9001-2015 registered and also certified by SGS.
Our custom lost foam casting fabrication service provides durable and affordable castings that meet your specifications for automotive, medical, aerospace, electronics, food, construction, security, marine, and more industries. Fast to send your inquiry or submit your drawings to get a free quote in the shortest time.Contact us or Email sales@hmminghe.com to see how our people, equipment and tooling can bring the best quality for the best price for your lost foam casting project.
We Provide Casting Services Include:
Minghe Casting services working with sand casting、metal casting 、investment casting lost foam casting, and more.

Sand Casting
Sand Casting is a traditional casting process that uses sand as the main modeling material to make molds. Gravity casting is generally used for sand molds, and low-pressure casting, centrifugal casting and other processes can also be used when there are special requirements. Sand casting has a wide range of adaptability, small pieces, large pieces, simple pieces, complex pieces, single pieces, and large quantities can be used.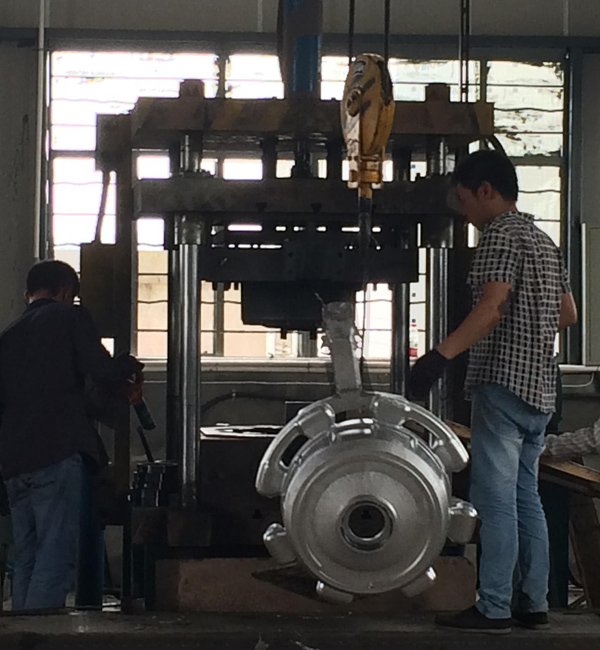
Permanent Mold Casting
Permanent Mold Casting have a long life and high production efficiency, not only have good dimensional accuracy and smooth surface, but also have higher strength than sand castings and are less likely to be damaged when the same molten metal is poured. Therefore, in the mass production of medium and small non-ferrous metal castings, as long as the melting point of the casting material is not too high, metal casting is generally preferred.
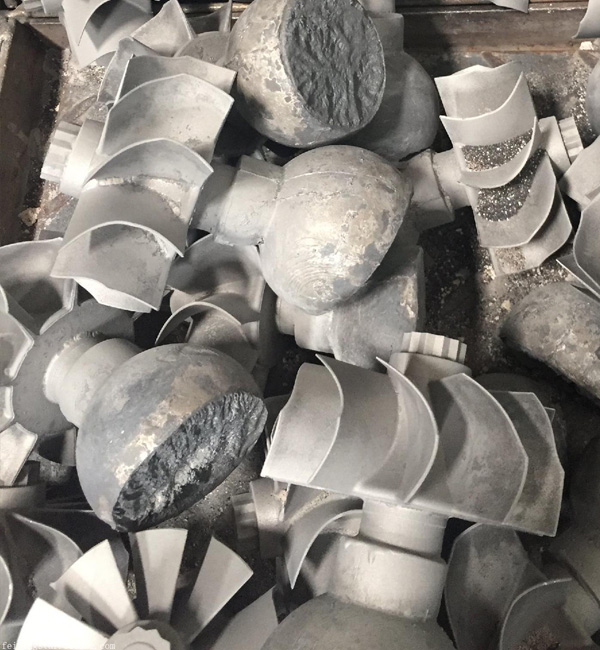
Investment Casting
The biggest advantage of investment casting is that because investment castings have high dimensional accuracy and surface finish, they can reduce machining work, but leave a little machining allowance on the parts with higher requirements. It can be seen that the use of investment casting method can save a lot of machine tool equipment and processing man-hours, and greatly save metal raw materials.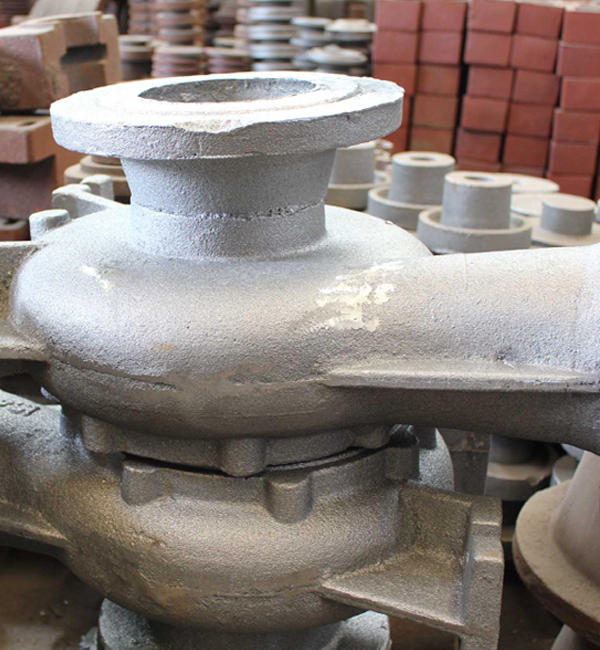
Lost Foam Casting
Lost foam casting is to combine paraffin wax or foam models similar to the casting size and shape into model clusters. After brushing and drying refractory coatings, they are buried in dry quartz sand for vibration modeling, and poured under negative pressure to gasify the model. , The liquid metal occupies the position of the model and forms a new casting method after solidification and cooling.

Die Casting
Die casting is a metal casting process, which is characterized by applying high pressure to the molten metal using the cavity of the mold. Molds are usually made of higher-strength alloys, and this process is somewhat similar to injection molding. Most die castings are iron-free, such as zinc, copper, aluminum, magnesium, lead, tin, and lead-tin alloys and their alloys. Minghe has been China's top die casting service since 1995.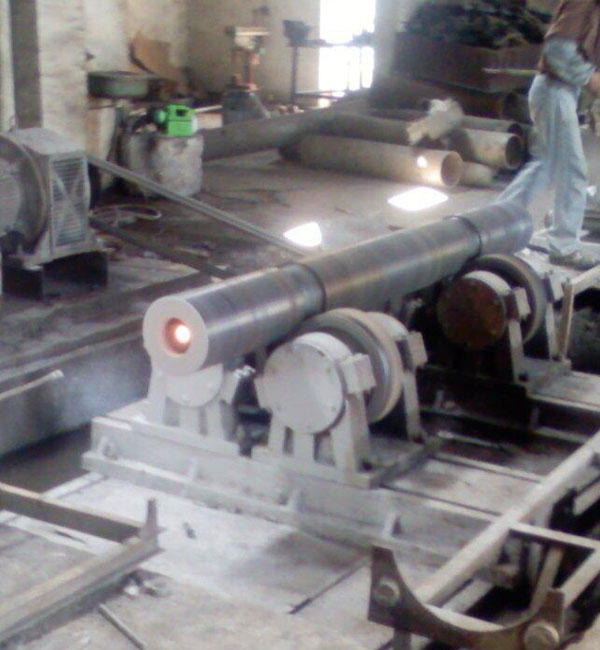
Centrifugal Casting
Centrifugal Casting is a technique and method of injecting liquid metal into a high-speed rotating mold, so that the liquid metal is centrifugal motion to fill the mold and form a casting. Due to the centrifugal movement, the liquid metal can fill the mold well in the radial direction and form the free surface of the casting; it affects the crystallization process of the metal, thereby improving the mechanical and physical properties of the casting.
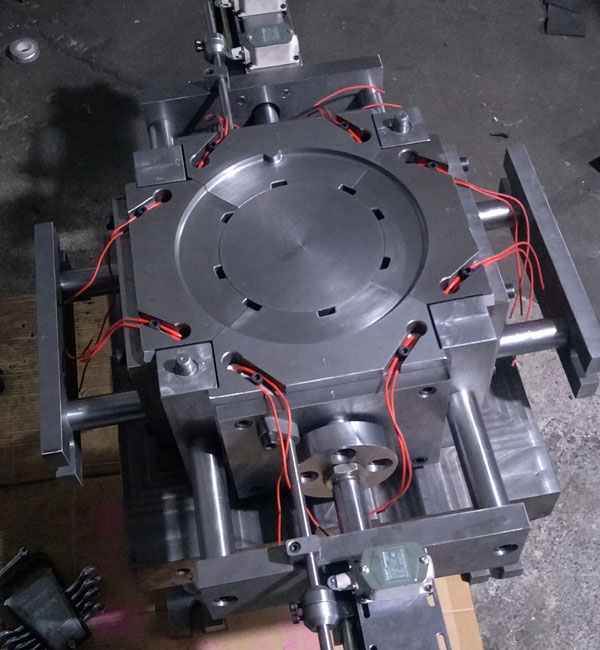
Low Pressure Casting
Low Pressure Casting means that the mold is generally placed above a sealed crucible, and compressed air is introduced into the crucible to cause a low pressure (0.06~0.15MPa) on the surface of the molten metal, so that the molten metal rises from the riser pipe to fill the mold and control Solidified casting method. This casting method has good feeding and dense structure, easy to cast large thin-walled complex castings, no risers, and a metal recovery rate of 95%. No pollution, easy to realize automation.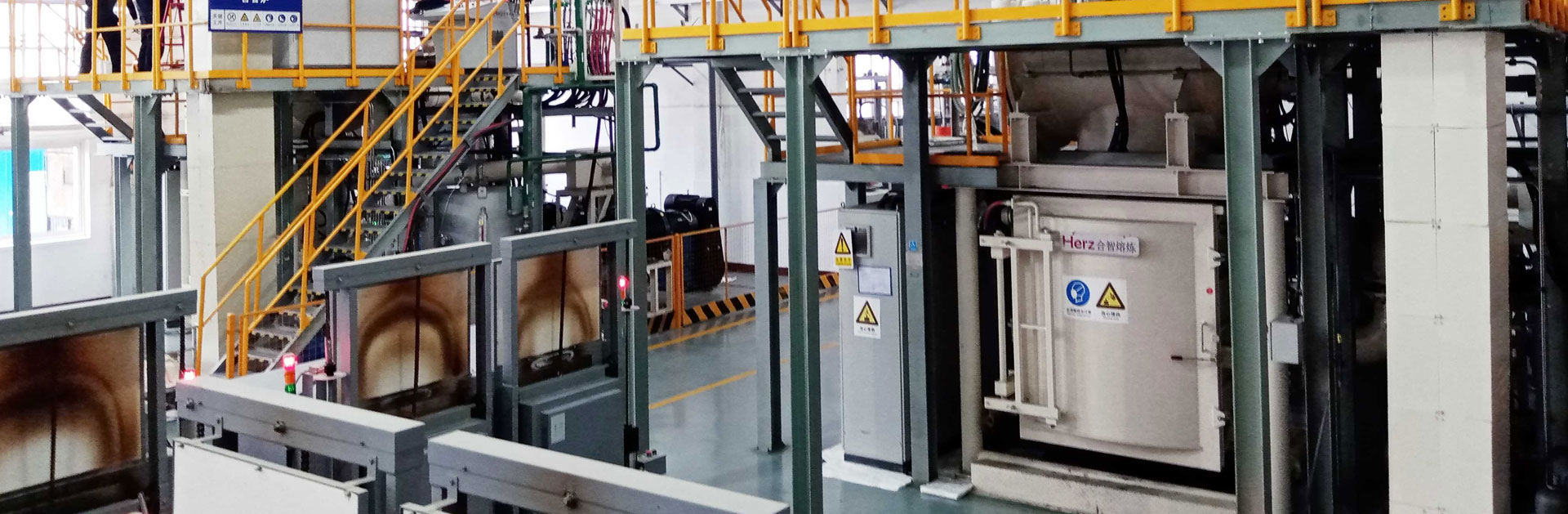