Pump Valve Parts
Pump Valve Parts Solutions By Casting &Cnc Machining
IATF 16949 CERTIFIED CAST MANUFACTURING AND CNC MACHINING FOR PUMP VALVE PARTS
Pump is a machine that delivers fluid or pressurizes fluid. It transfers the mechanical energy of the prime mover or other external energy to the liquid to increase the liquid energy. The pump is mainly used to transport liquids such as water, oil, acid-base liquid, emulsion, suspension emulsion and liquid metal, as well as liquid, gas mixture and liquid containing suspended solids. The impeller is installed in the pump casing and fastened to the pump shaft, which is directly driven by the motor. There is a liquid suction pipe in the center of the pump housing. The liquid enters the pump through the bottom valve and the suction pipe. The liquid discharge port on the pump casing is connected with the discharge pipe.
Before the pump is started, the pump casing is filled with the liquid being transported; after starting, the impeller is driven by the shaft to rotate at a high speed, and the liquid between the blades must also rotate with it. Under the action of centrifugal force, the liquid is thrown from the center of the impeller to the outer edge and gains energy, leaving the outer edge of the impeller at a high speed into the volute pump casing. In the volute, the liquid decelerates due to the gradual expansion of the flow channel, and converts part of the kinetic energy into static pressure energy, and finally flows into the discharge pipe at a higher pressure and is sent to the place where it is needed. When the liquid flows from the center of the impeller to the outer edge, a certain vacuum is formed in the center of the impeller. Because the pressure above the liquid level of the storage tank is greater than the pressure at the inlet of the pump, the liquid is continuously pressed into the impeller. It can be seen that as long as the impeller rotates continuously, the liquid will be continuously sucked and discharged.
Pump valve is a collective term for pumps and valves. It is an industrial equipment used in liquid transportation. The reason why pumps and valves are often linked together is the occasion. In other words, there are usually valves where there are pumps, and pumps are often needed in some places. They are used in places where liquids are transported. Of course, valves are also used for gas. Vacuum pumps are also related to gas.
For pump-valve parts and products mass production manufacturing, MINGHE CASTING offers the highest degree of machining & casting service with a basis of 30+ years experience serving the pump-valve industry. Our pump-valve casting shop and experts deliver confidence. We have perfected the art of producing large component volumes with complete JIT reliability, backed by the quality and long-term reliability our customers expect.
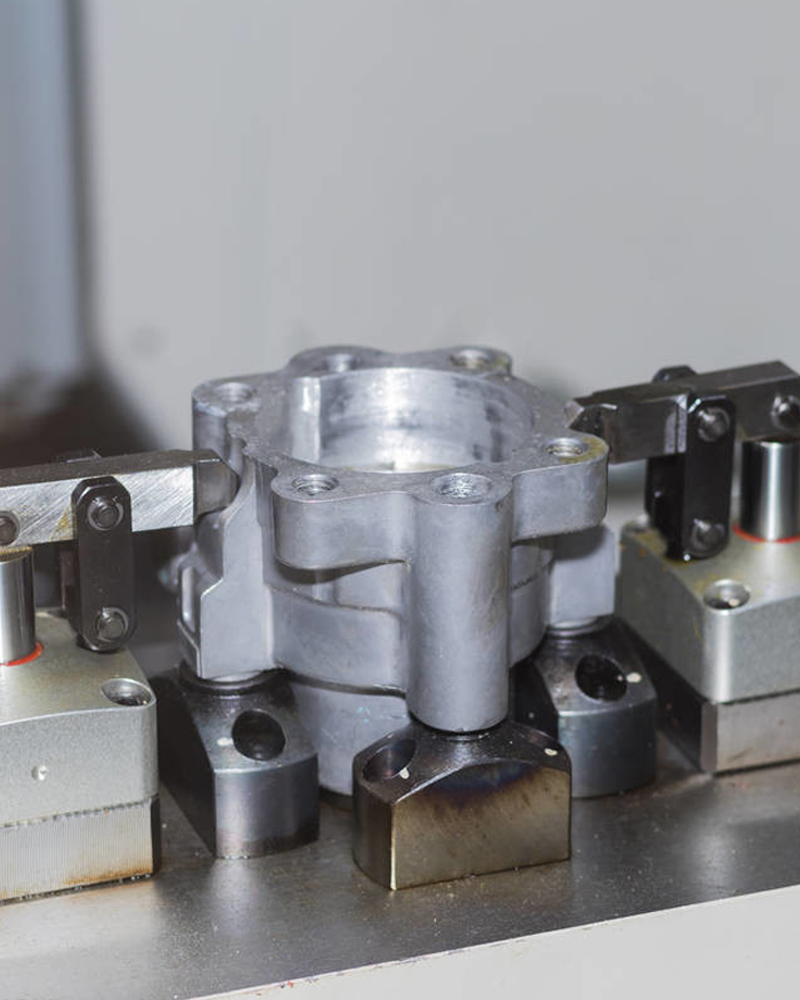
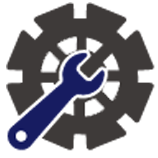
Contact our pump valve part engineer today to discuss the specifics of your complex projects.
1.Commonly Pump Valve Components Applications.
MINGHE’s experience is unrivaled in the design, development, and manufacture of precision die cast and cnc machining solutions for a wide range of Pump Valve applications, including but not limited to:
-
Pump categories: water pumps, oil pumps, chemical pumps, diaphragm pumps, sewage pumps, screw pumps, submersible pumps, sewage pumps, submersible pumps, reciprocating pumps, air conditioning pumps, feed water pumps, multi-stage pumps, pipeline pumps, centrifugal pumps, three-screw Pumps, twin screw pumps, heat conduction oil pumps, scavenge pumps, corrosion-resistant pumps, high temperature and high pressure pumps, vacuum pumps, magnetic pumps, miniature electric pumps, mining pumps, slurry pumps, pulp pumps, non-clogging pumps, self-priming pumps, increase Pressure pump, fire pump, constant pressure tangent pump, clean water pump, thick slurry pump, mud pump, etc.
Valve classification: ball valve, butterfly valve, globe valve, check valve, gate valve, regulating valve, throttle valve, oxygen valve, power station valve, drain valve, discharge valve, vacuum valve, solenoid valve, pressure reducing valve, pressure regulating valve, Angle valve, angle valve, three-way valve, four-way valve, multi-way valve, duckbill valve, flat gate valve, oil field valve, shut-off valve, slag discharge valve, knife gate valve, ash unloading valve, fluorine-lined rubber valve, and many more
2.Why Choose Us For Your Pump Valve Parts Projects
Minghe has over 30 years of experience assisting pump valve manufacturers design cost-effective mechanical components. When you partner with Minghe you can receive the following benefits from our die casting process:
- Minghe’s die casting operation features 40 presses ranging from 250 to 3000 ton. We accommodate some of the most demanding pump valve part runs in terms of volume, part size, and complexity. Because of our engineering and modeling capabilities, we are known by our clients as a company that can reduce part complexity, and make the manufacturing process more efficient.
- Minghe can help consolidate your supply chain by offering the complete package of die casting services in addition to engineering support, mold design and troubleshooting, machining, and logistics.
- Minghe is an ISO Certified Die Casting Manufacturer and has extensive experience in designing and manufacturing zinc and aluminum parts to pump valve quality specifications.
- With presses ranging from large to small, we have the capability to manufacture pump valve parts of all sizes, from a valve cover to large housings.
- We are ITAF 16949 certified and can provide part manufacturing for military and pump valve applications.
- Our technology facilitates and streamlines production. Our suite of technology includes AutoCAD, Pro-E, MAGMAsoft®, CAD/CAM and EDI compatibility, and FARO Laser Scanning.
3.Other Manufacturing Service For Custom Pump Valve Parts
In addition, Minghe also provides CNC machining, investment casting, sand casting and other services related to customized pump valve parts.
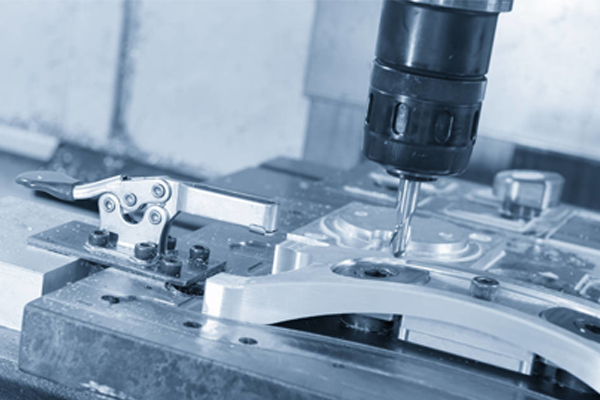
Cnc Machining Pump Valve Parts |
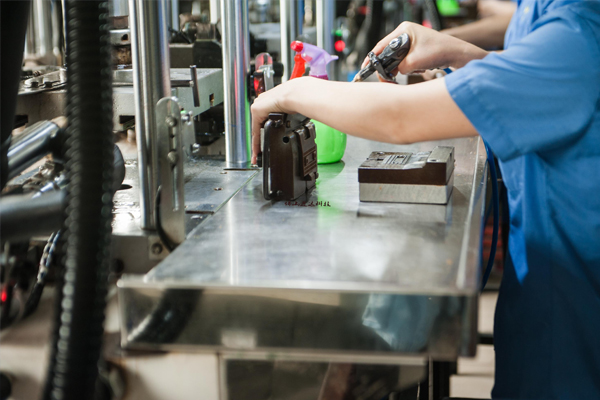
Investment Casting Pump Valve Parts |
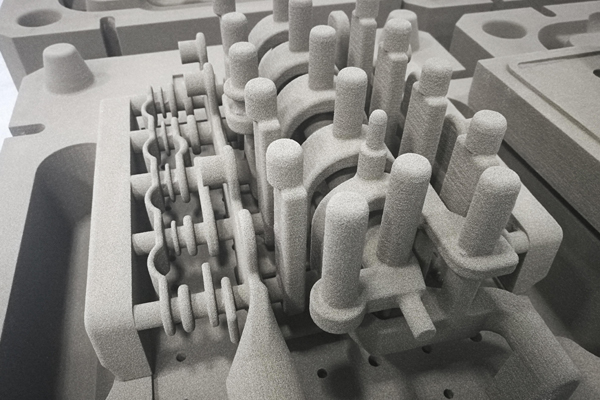
Sand Casting Pump Valve Parts |
4.Capabilities of Our Precision Manufacturing for Pump Valve Parts
In addition, Minghe also provides CNC machining, investment casting, sand casting and other services related to customized pump valve parts.
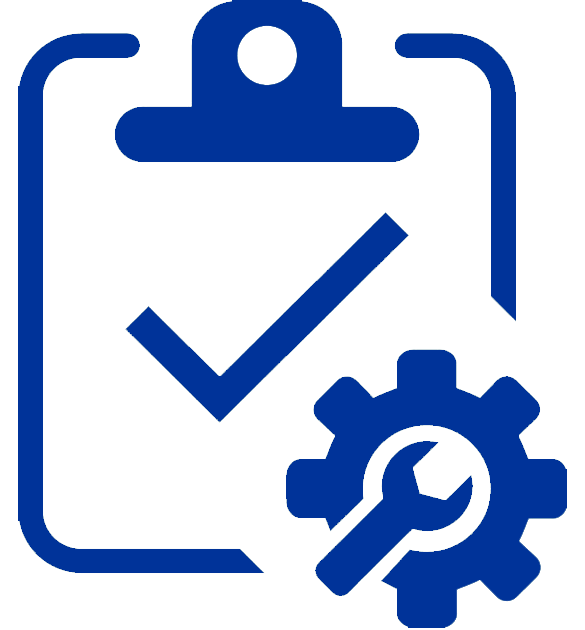
AL360, AL380, AL383, and AL413, ZA-8, ZA-12, ZA-27,Aluminium A356,
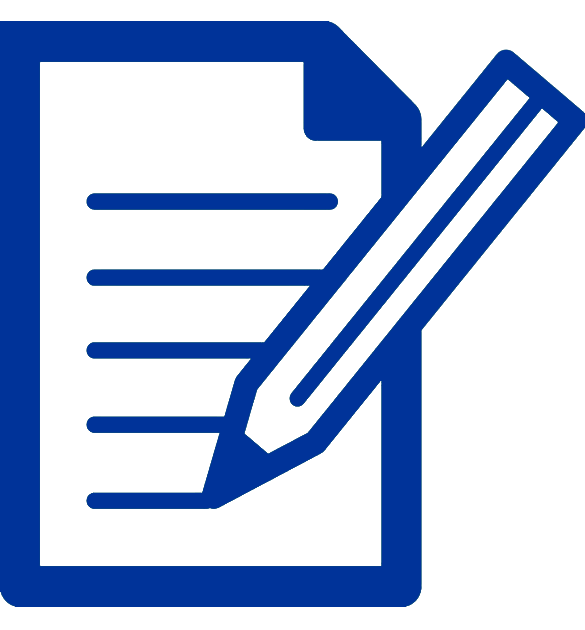
Black, White, Silver, Red, Natural, Blue, Green and different colors as client requirements
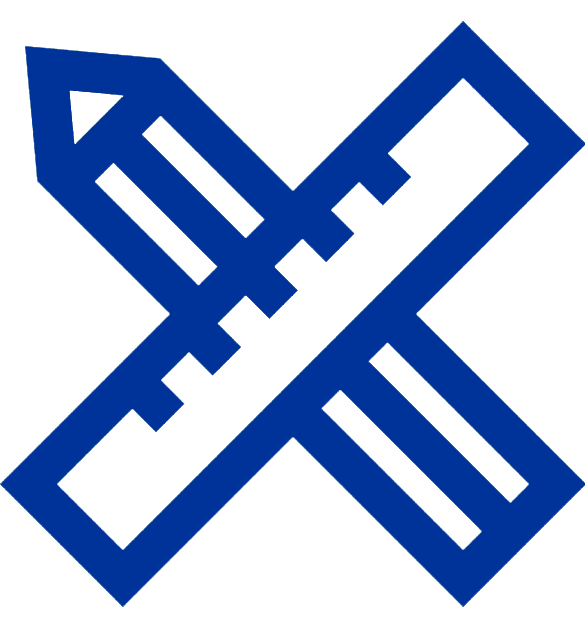
Sand blasting, shot blasting, polishing, anodizing, oxidation, electrophoresis, chromate, powder coating and painting
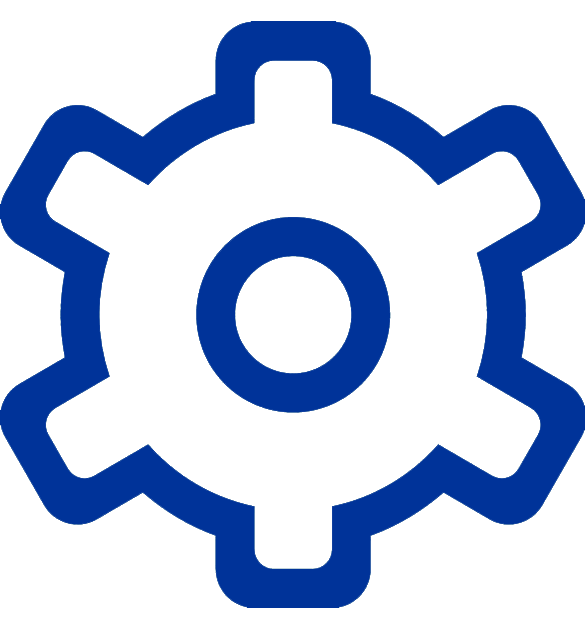
Die Casting,Mold Manufacturing,CNC milling, CNC turning, CNC drilling
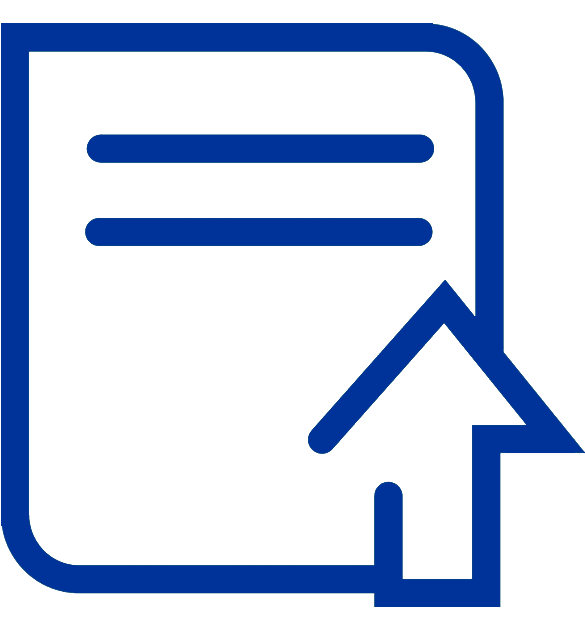
Positive displacement pump/impeller pump/jet pump/vertical pump/horizontal pump/single suction pump/double suction pump/motor pump/steam turbine pump/diesel pump/diaphragm pump;
The Minghe Case Studies Of Pump Valve Parts Casting
You have a complex part design, Minghe Casting Company can help you turn it into a reality. With the right equipment, strong technical knowledge, and a focus on quality.. From tool design to finishing and then on to shipment, Minghe Casting ensure that every project is completed to a high standard and that your orders are delivered on time, every time.
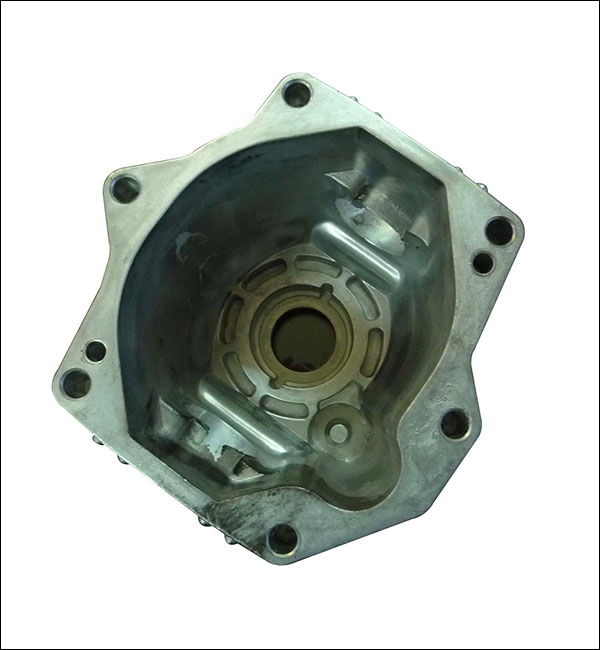
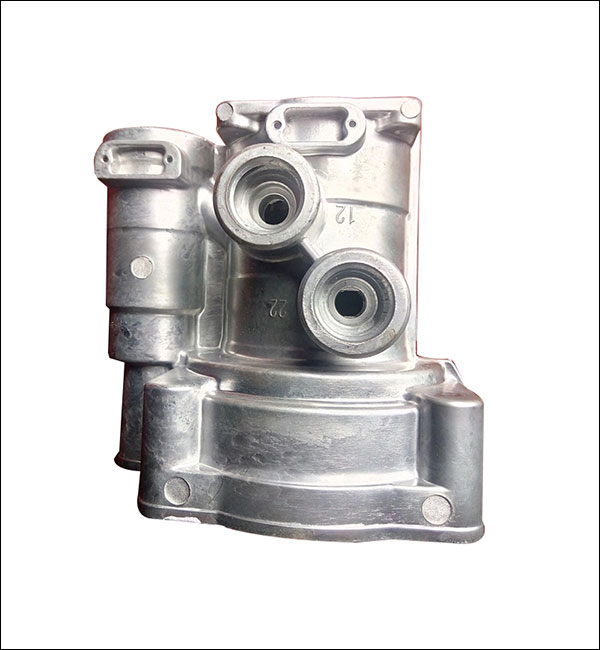
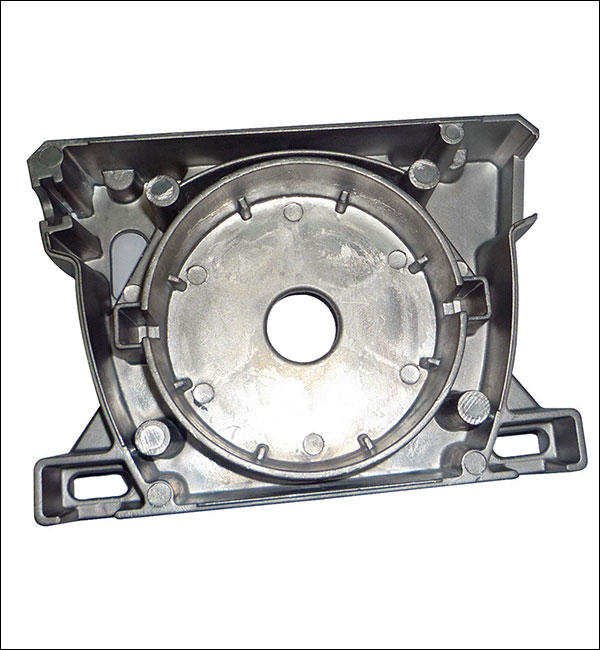
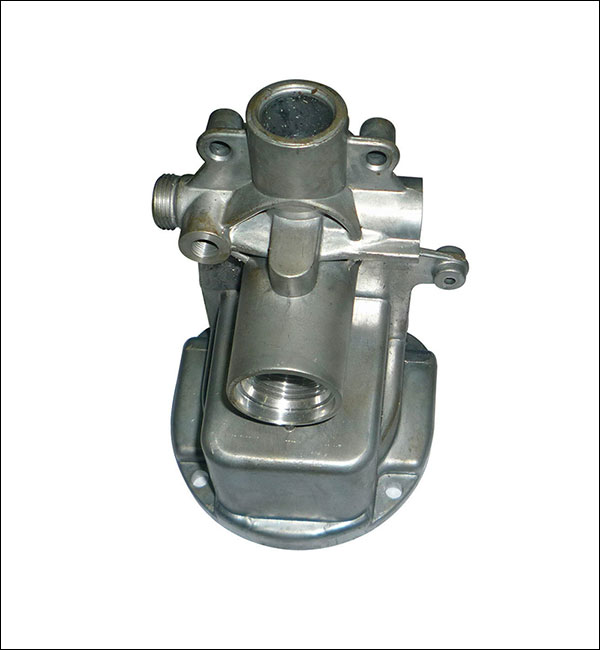
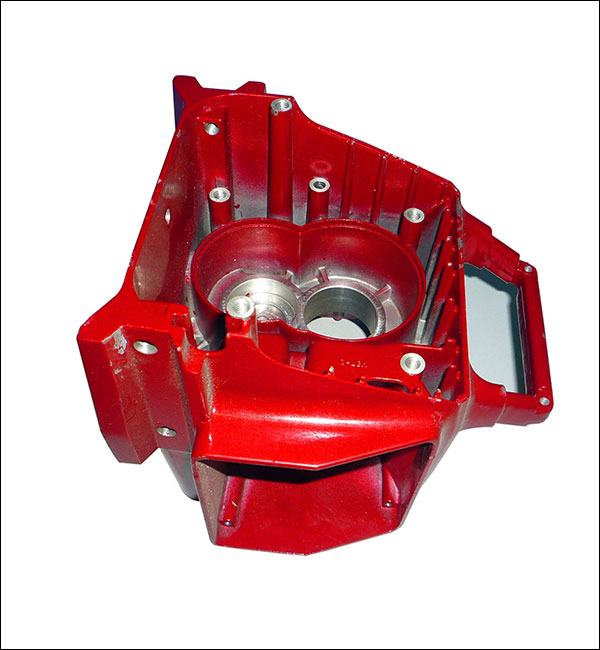
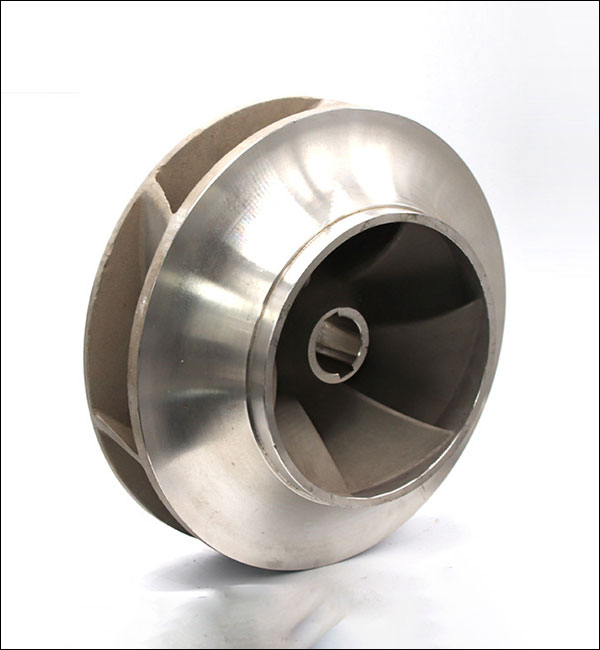
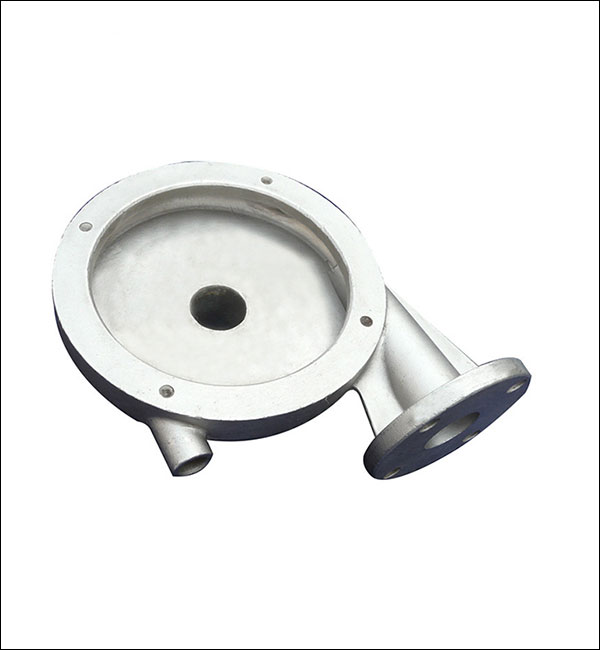
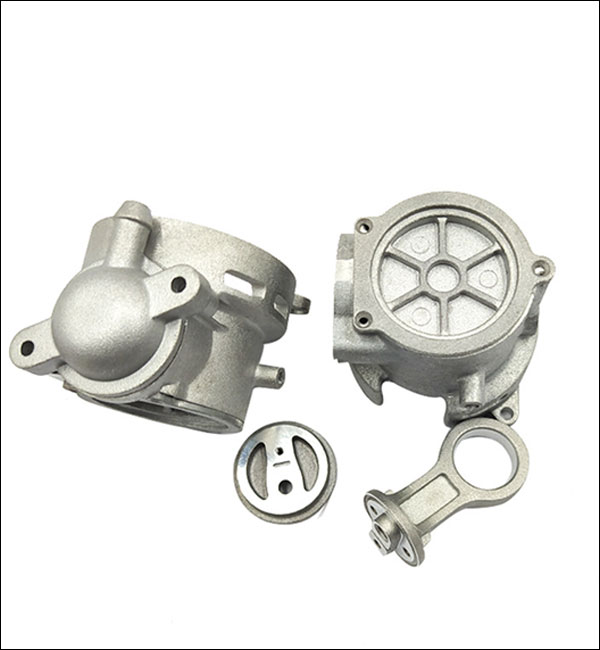
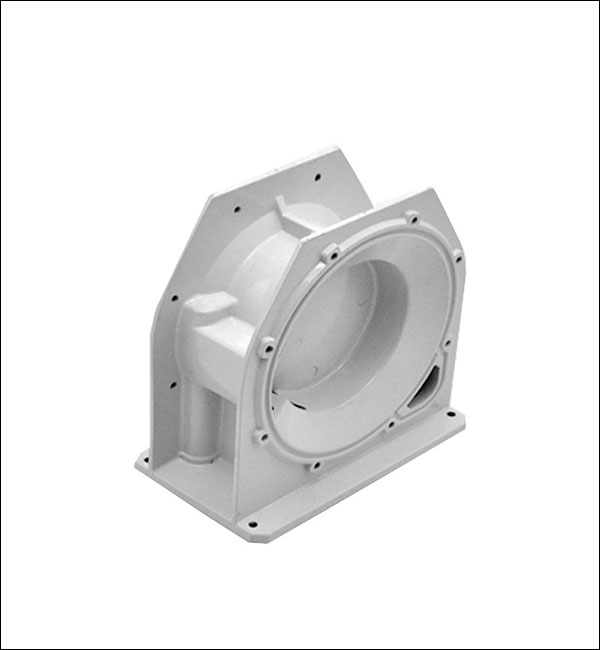
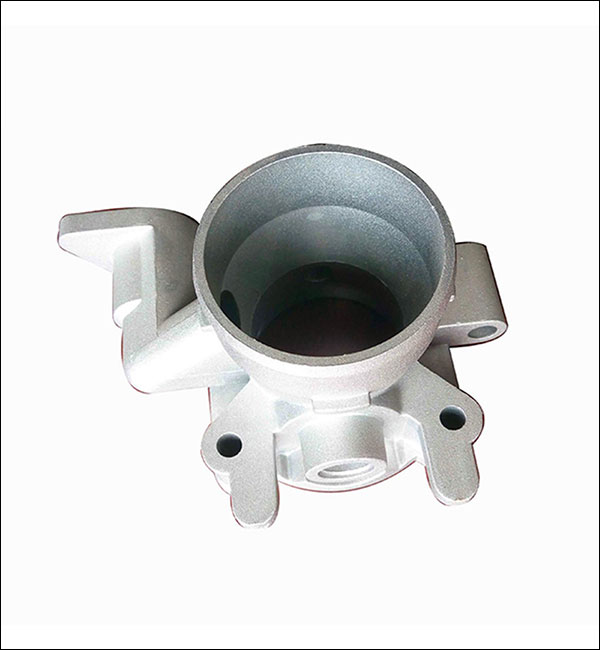
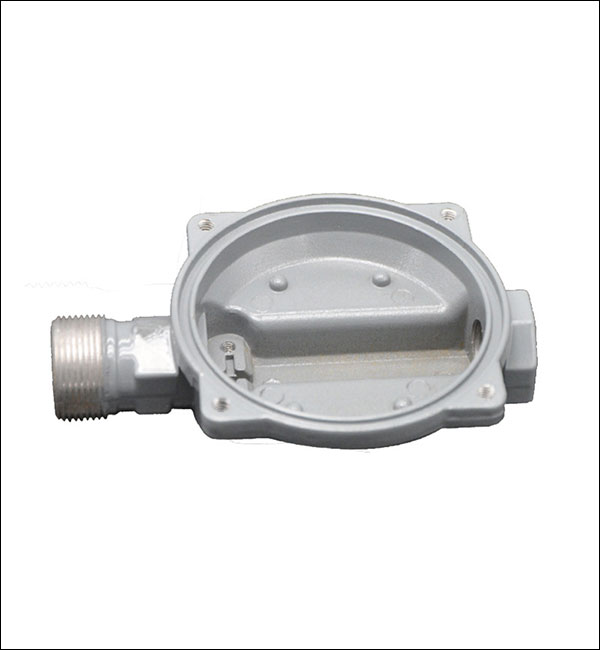
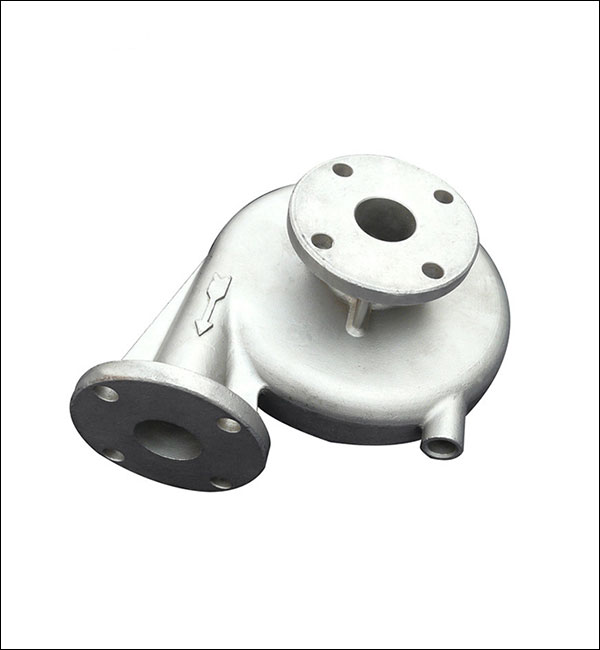
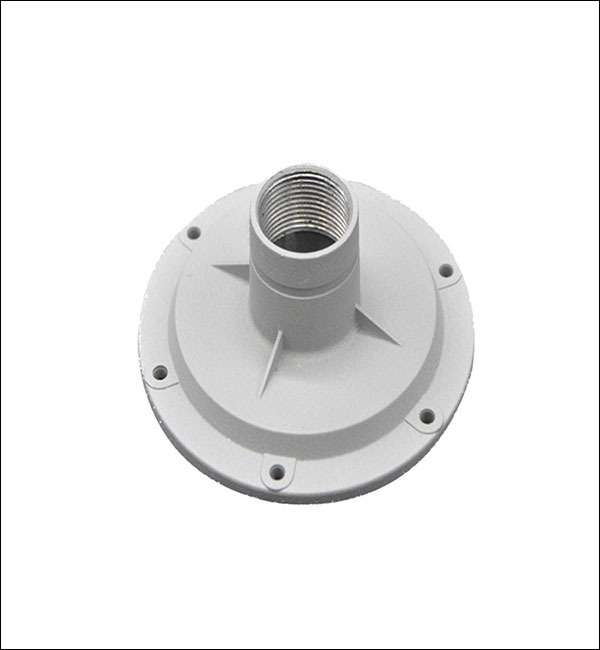
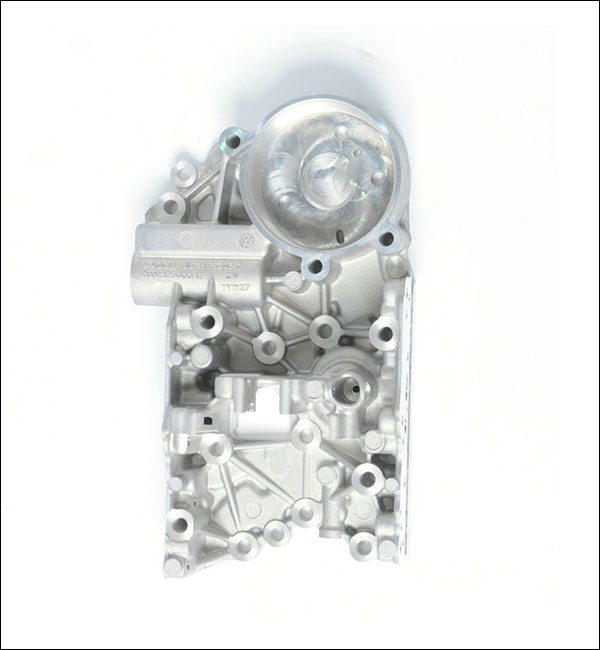
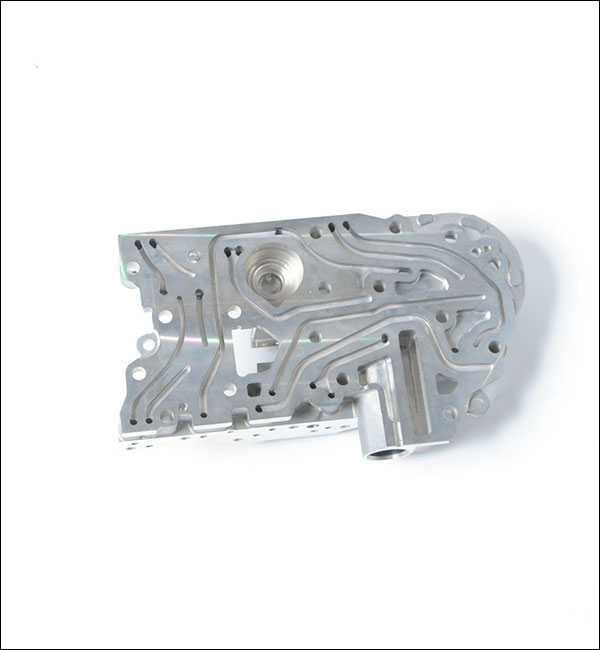
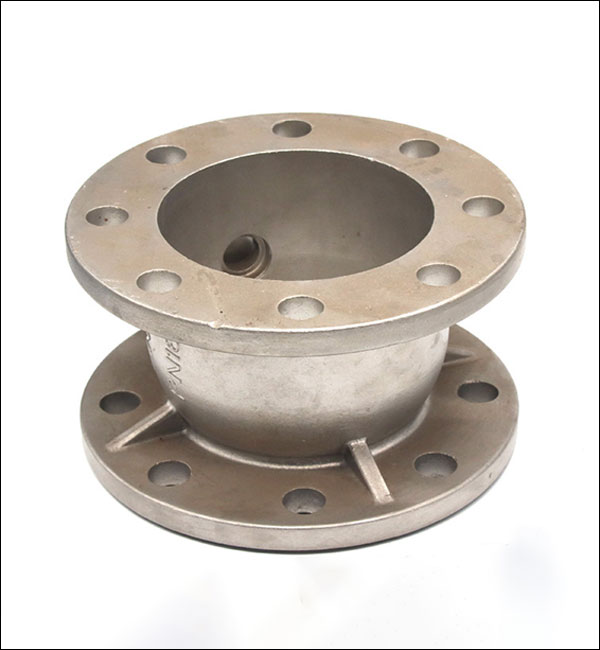
Go To View More Casting Parts Cases Studies >>>
Choose the Best Pump Valve Parts Casting Service
Currently, our pump valve casting parts are exported to America, Canada, Australia, United Kingdom, Germany, France, Sout Africa, and many other countries all over the world. We are ISO9001-2015 registered and also certified by SGS.
Custom china die casting service provides durable and affordable castings that meet your specifications for automotive, medical, aerospace, electronics, food, construction, security, marine, and more industries. Fast to send your inquiry or submit your drawings to get a free quote in the shortest time.Contact us or Email sales@hmminghe.com to see how our people, equipment and tooling can bring the best quality for the best price for your pump valve casting project.
We Provide Casting Services Include:
Minghe Casting services working with sand casting、metal casting 、investment casting lost foam casting, and more.

Sand Casting
Sand Casting is a traditional casting process that uses sand as the main modeling material to make molds. Gravity casting is generally used for sand molds, and low-pressure casting, centrifugal casting and other processes can also be used when there are special requirements. Sand casting has a wide range of adaptability, small pieces, large pieces, simple pieces, complex pieces, single pieces, and large quantities can be used.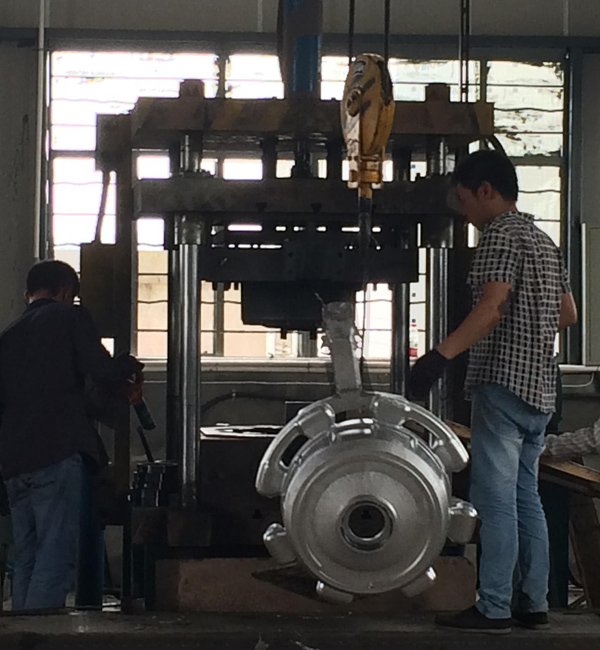
Permanent Mold Casting
Permanent Mold Casting have a long life and high production efficiency, not only have good dimensional accuracy and smooth surface, but also have higher strength than sand castings and are less likely to be damaged when the same molten metal is poured. Therefore, in the mass production of medium and small non-ferrous metal castings, as long as the melting point of the casting material is not too high, metal casting is generally preferred.
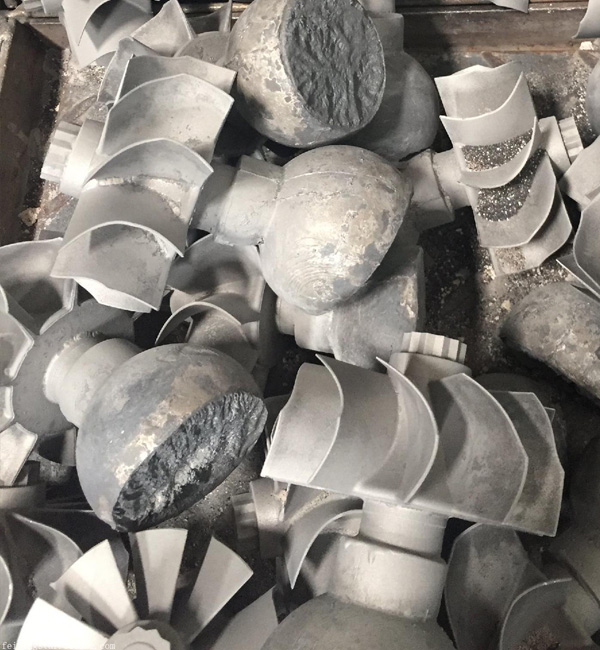
Investment Casting
The biggest advantage of investment casting is that because investment castings have high dimensional accuracy and surface finish, they can reduce machining work, but leave a little machining allowance on the parts with higher requirements. It can be seen that the use of investment casting method can save a lot of machine tool equipment and processing man-hours, and greatly save metal raw materials.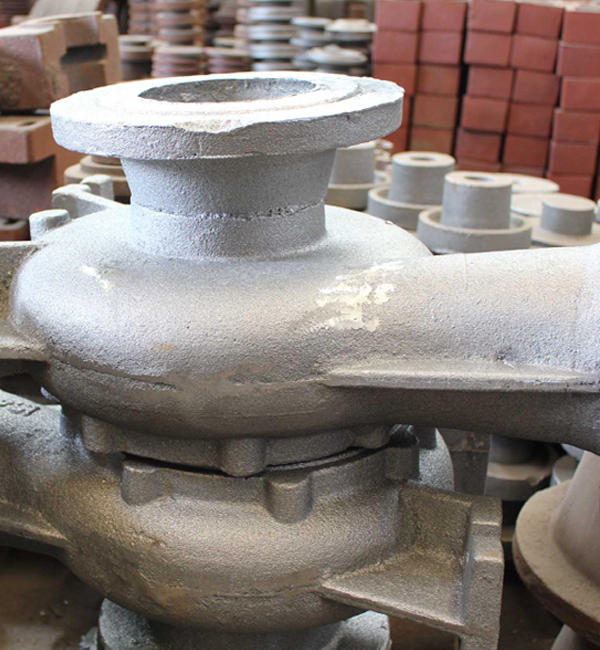
Lost Foam Casting
Lost foam casting is to combine paraffin wax or foam models similar to the casting size and shape into model clusters. After brushing and drying refractory coatings, they are buried in dry quartz sand for vibration modeling, and poured under negative pressure to gasify the model. , The liquid metal occupies the position of the model and forms a new casting method after solidification and cooling.

Die Casting
Die casting is a metal casting process, which is characterized by applying high pressure to the molten metal using the cavity of the mold. Molds are usually made of higher-strength alloys, and this process is somewhat similar to injection molding. Most die castings are iron-free, such as zinc, copper, aluminum, magnesium, lead, tin, and lead-tin alloys and their alloys. Minghe has been China's top die casting service since 1995.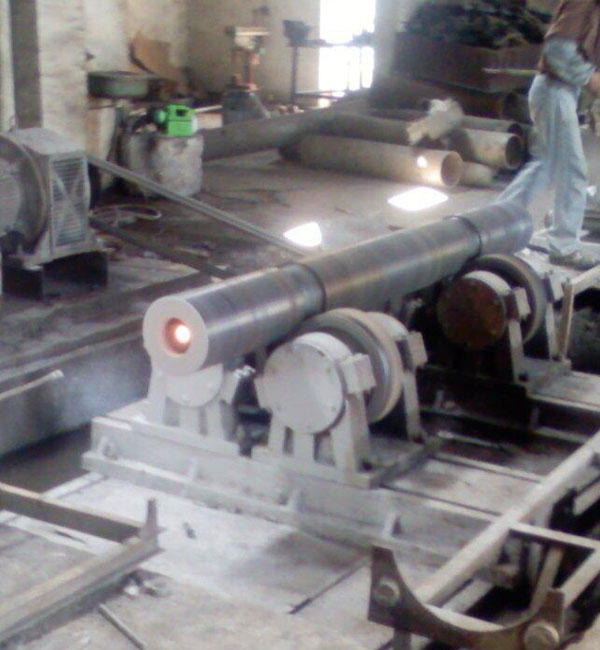
Centrifugal Casting
Centrifugal Casting is a technique and method of injecting liquid metal into a high-speed rotating mold, so that the liquid metal is centrifugal motion to fill the mold and form a casting. Due to the centrifugal movement, the liquid metal can fill the mold well in the radial direction and form the free surface of the casting; it affects the crystallization process of the metal, thereby improving the mechanical and physical properties of the casting.
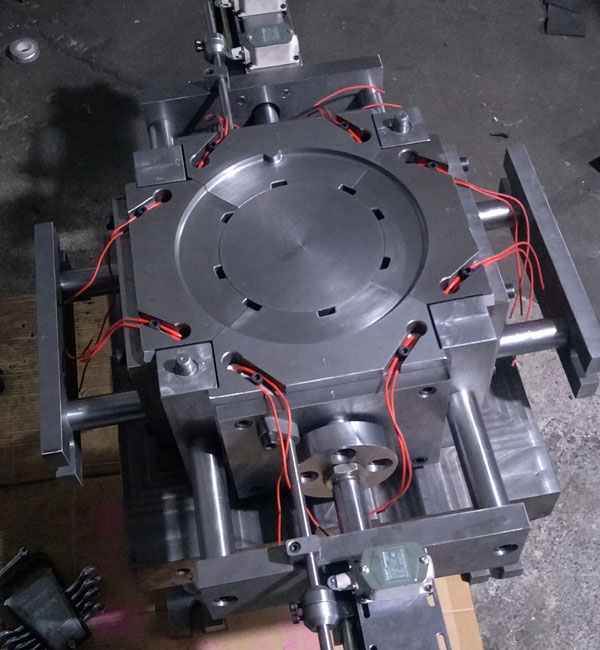
Low Pressure Casting
Low Pressure Casting means that the mold is generally placed above a sealed crucible, and compressed air is introduced into the crucible to cause a low pressure (0.06~0.15MPa) on the surface of the molten metal, so that the molten metal rises from the riser pipe to fill the mold and control Solidified casting method. This casting method has good feeding and dense structure, easy to cast large thin-walled complex castings, no risers, and a metal recovery rate of 95%. No pollution, easy to realize automation.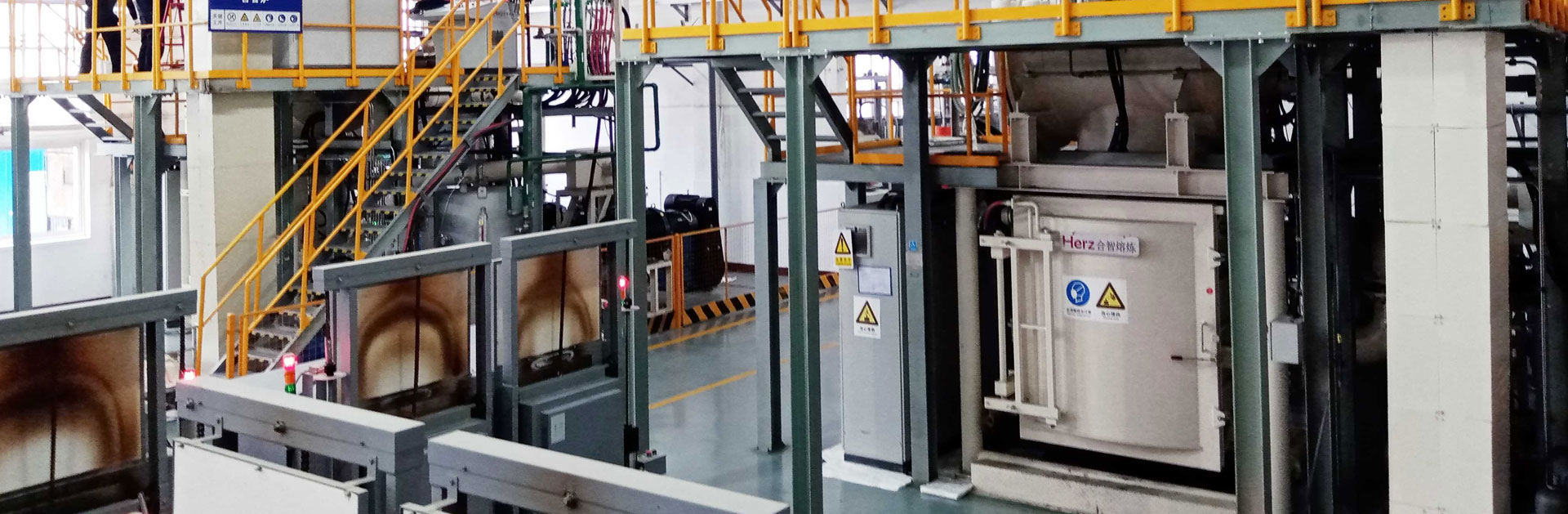