Titanium Casting
Titanium Casting Services – Custom Casting Titanium Alloy Parts China Company
IATF 16949 CERTIFIED CAST MANUFACTURING FOR TITANIUM CASTINGS
What Is Titanium Casting? Casting Titanium Alloy refers to the process of smelting and pouring titanium materials into castings under vacuum or protective gas conditions. Most deformed titanium alloys have good casting properties. One of the most widely used is Ti-6A1-4V alloy. It has the best casting process performance and stable structure, and has good strength (5σb≥890MPa) and fracture toughness below 350°C.
Titanium castings are mainly used in the aerospace industry. Important parts used are: engine compressor casing, intermediate casing, blades, hollow guide, inner ring, turbocharger impeller, bearing housing and support, aircraft bracket, umbrella compartment, lugs, short beam, flap Wing slides, brake shells; missile control cabins, tail wings, rocket rear heads, public bottoms, etc.; artificial satellites, scanner frames, lens barrels, etc. It is widely used in the civil industry to manufacture corrosion-resistant pump bodies, valves, impellers; screw propellers for ships; shells, brackets, and cylinders for precision machinery; artificial joints and prosthetic components for medical use; golf heads for sports equipment, horses Tools, bicycle parts, etc.
Minghe is a casting titanium China company specialized in custom titanium parts manufacturing for more than 35 years, with advanced in-house equipment and tool facility, proficient machinists, and rich expertise, we can provide mass titanium casting services and customize quality titanium casting parts with exact specification, budget prices and on-time delivery based on your requirements. In our titanium casting shop, Die Casting,Sand Casting,Investment Casting, Lost Foam Casting and more processes are available, as well as excellent surface finishing. Our lineup of titanium and titanium alloy components can be used in broad range of industries and applications, typically including airplane parts and fasteners, gas turbine engines, compressor blades, casings, engine cowlings and heat shields. We are aiming to establish close and friendly cooperation with worldwide customers.
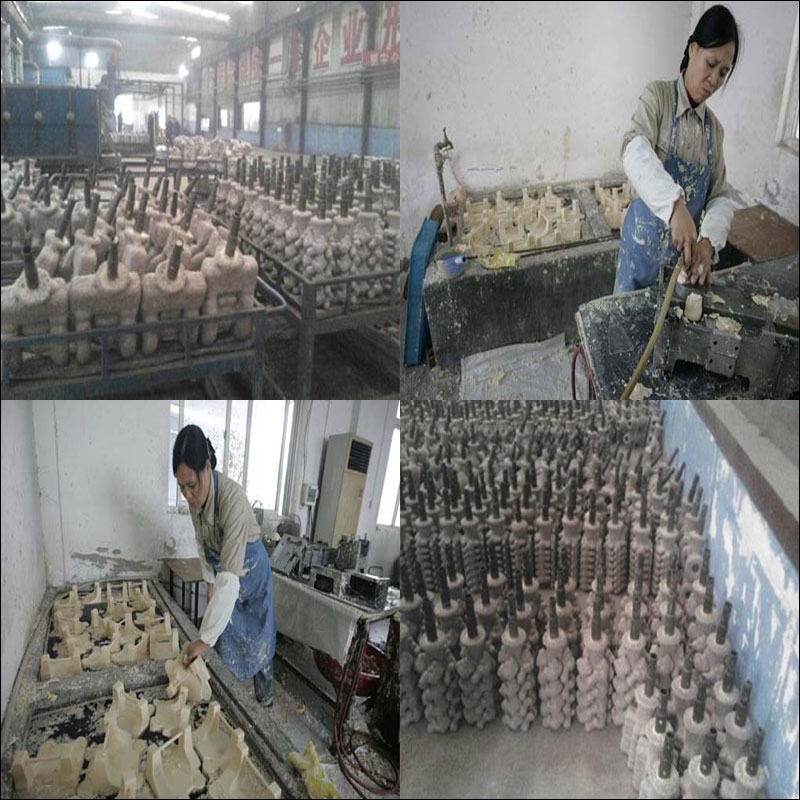
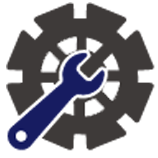
Contact our titanium casting part engineer today to discuss the specifics of your complex projects.
The History Of Titanium Alloy Casting.
Titanium is very active in the molten state. For a long time, it has not been possible to find a suitable casting method and modeling material. As a result, cast titanium lags behind deformed titanium alloy for more than 20 years. From 1956 to 1962, American Bell (Beal) and others developed vacuum consumable arc condensed shell melting technology, which made titanium castings officially enter industrial production. In the 1970s, it began to be used in the aerospace field. Since the 1970s, titanium alloy large-scale thin-wall precision casting technology has been developed and applied. Under the premise that its material performance is close to or equal to aviation titanium forgings, the cost is reduced by about 50%, so the titanium casting technology has developed rapidly. It is expected that in the near future, it will achieve the same important position as wrought titanium alloy.
The Casting Method Of Titanium
Titanium castings are mostly used in vacuum condensing furnace and graphite casting. Compared with deformed alloys of the same composition, their strength is basically equal, but the plasticity and fatigue properties are about 40%-50% lower, and the fracture toughness is slightly better. Most titanium castings are treated with stabilized annealing. The solution treatment and hydrogenation treatment under study can refine the alloy casting structure and increase its fatigue strength to the level of forgings.
1.The Graphite Casting Of Titanium
Graphite is the main molding process for the production of civilian titanium castings. It is divided into processing graphite type and graphite tamping type. The processed graphite mold is made by manual or mechanical processing of high-quality artificial graphite blocks. According to the complexity of the mold, multiple movable block combinations can be used. This mold can be used multiple times. The graphite tamping type is formed by grinding and mixing artificial graphite sand and carbonaceous organic binder into a mixture, which is molded by hand or modeling machinery in a wooden mold or a metal mold sand box. The finished graphite sand mold is baked, dried and solidified at a low temperature, and then fired at a high temperature under the cover of dry dispersed graphite powder or under the protection of a non-oxidizing atmosphere. After the mold combination is made, it can be installed in the furnace for casting. For the production of aerospace castings with strict quality requirements, the processing and tamping types need to be vacuum degassed before casting
2.The Investment Casting Of Titanium
Investment casting is the main process for producing titanium alloy castings for aviation with high precision, complex shape, smooth surface and dense interior. The investment casting method of titanium is basically the same as the steel precision casting process, except for the shell materials and certain processes.There are three processes used to produce titanium precision castings today:
- - Graphite shell process.
- - Ceramic shell technology with metal surface layer.
- - Oxide ceramic shell process. The first type is cheap and can be used for the production of small and medium castings, and the latter two can be used for the production of large thin-wall precision castings.
Casting titanium alloy and casting quality Most deformed titanium alloys can be used for casting, the most widely used is Ti-6A1-4V alloy. It has good casting properties and stable organization properties. Compared with the deformation alloy of the same composition, the strength of cast titanium alloy is basically equal, but its plasticity and fatigue properties are about 40%-50% lower, and the fracture toughness is slightly better.
Titanium castings are generally treated with stabilized annealing. The solution treatment and hydrogenation treatment under study can refine the grains, improve the structure, and improve the fatigue performance of the alloy to the level of forgings. Hot isostatic pressing is a common treatment method for high-quality titanium castings. After high temperature and high pressure treatment, the size of the casting does not change, but the internal structure becomes denser, and the stability of mechanical properties will be greatly improved. The quality of castings should be inspected according to national standard GB6614, national military standard GJB2896 or aviation standard HB5448. The technical characteristics of titanium alloy castings are listed in the table
The Minghe Case Studies Of Titanium Casting
Minghe Casting fabrication services are available for both design to reality and low to high volume production runs of your aluminum casting parts,zinc casting parts,magnesium casting,titanium casting parts,stainless steel casting parts,copper casting parts,steel casting parts, brass casting parts and more.
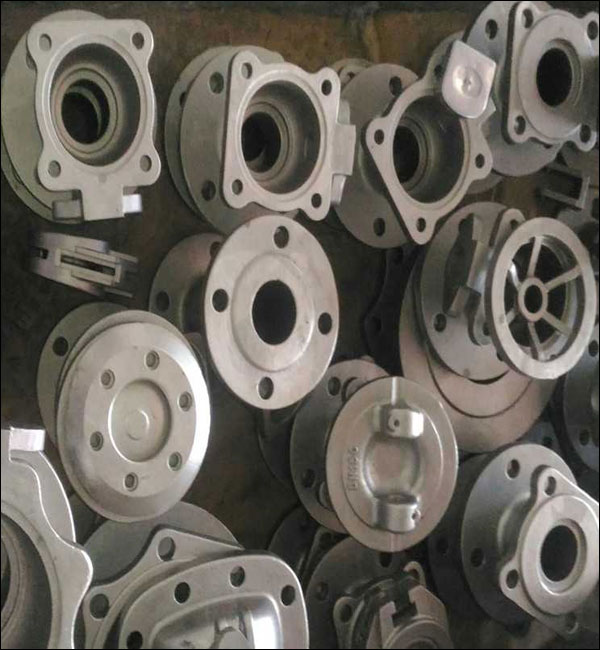
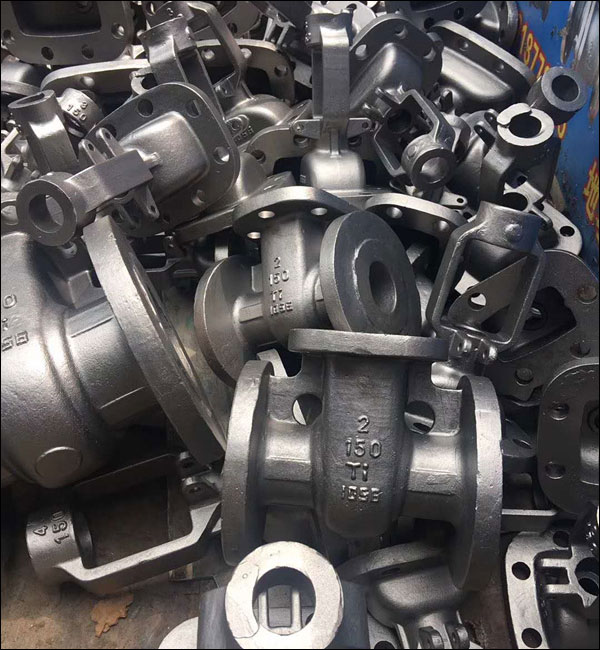
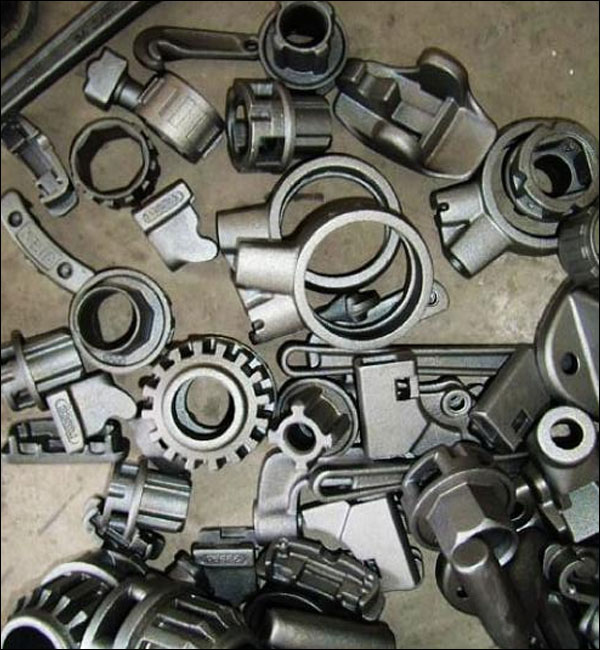
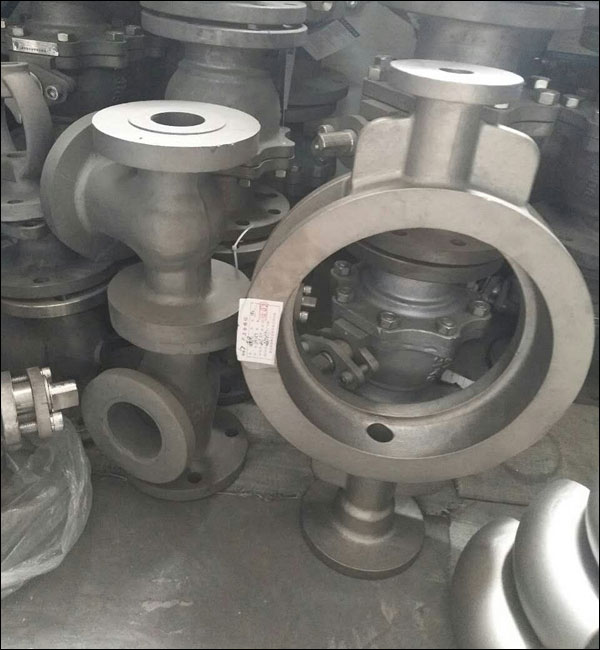
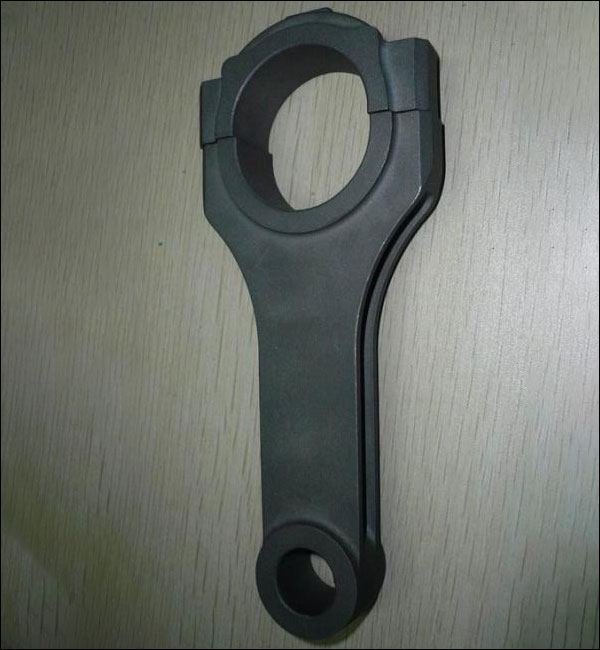
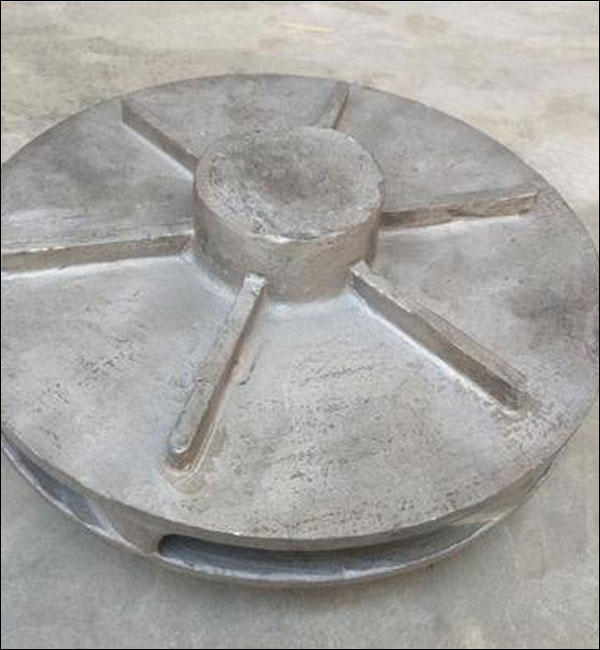
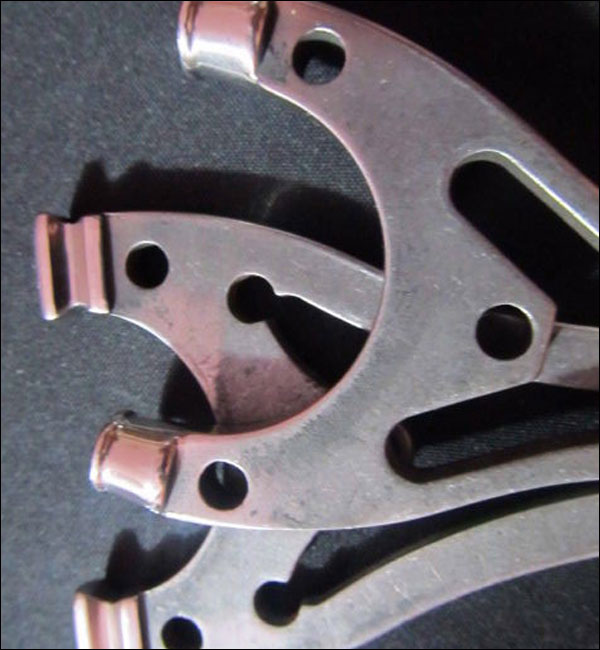
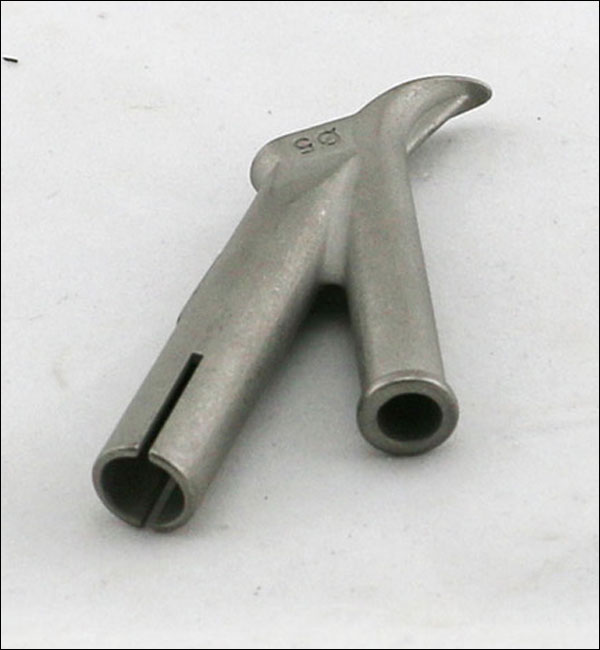
Go To View More Casting Parts Cases Studies >>>
Choose the Best Titanium Casting Supplier
Currently, our titanium casting parts are exported to America, Canada, Australia, United Kingdom, Germany, France, Sout Africa, and many other countries all over the world. We are ISO9001-2015 registered and also certified by SGS.
Our custom titanium casting fabrication service provides durable and affordable castings that meet your specifications for automotive, medical, aerospace, electronics, food, construction, security, marine, and more industries. Fast to send your inquiry or submit your drawings to get a free quote in the shortest time.Contact us or Email sales@hmminghe.com to see how our people, equipment and tooling can bring the best quality for the best price for your titanium casting project.
We Provide Casting Services Include:
Minghe Casting services working with sand casting、metal casting 、investment casting lost foam casting, and more.

Sand Casting
Sand Casting is a traditional casting process that uses sand as the main modeling material to make molds. Gravity casting is generally used for sand molds, and low-pressure casting, centrifugal casting and other processes can also be used when there are special requirements. Sand casting has a wide range of adaptability, small pieces, large pieces, simple pieces, complex pieces, single pieces, and large quantities can be used.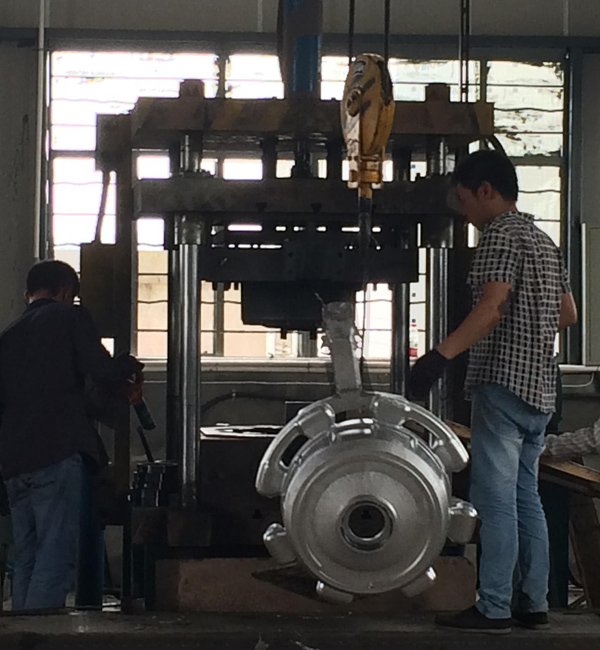
Permanent Mold Casting
Permanent Mold Casting have a long life and high production efficiency, not only have good dimensional accuracy and smooth surface, but also have higher strength than sand castings and are less likely to be damaged when the same molten metal is poured. Therefore, in the mass production of medium and small non-ferrous metal castings, as long as the melting point of the casting material is not too high, metal casting is generally preferred.
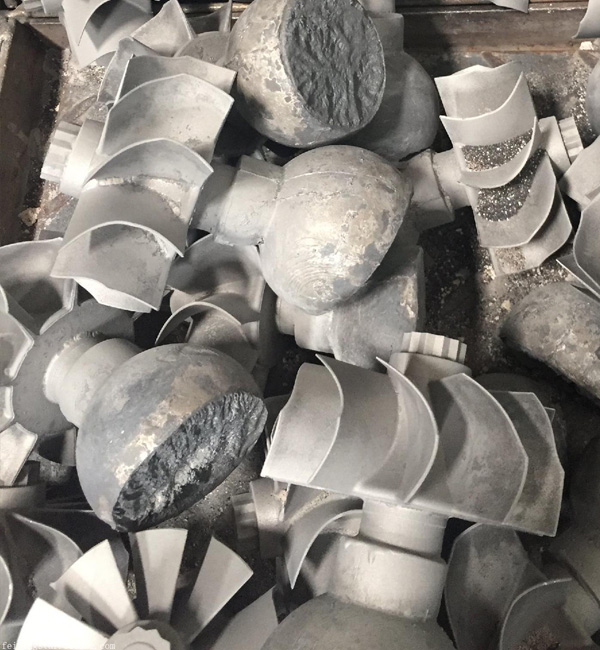
Investment Casting
The biggest advantage of investment casting is that because investment castings have high dimensional accuracy and surface finish, they can reduce machining work, but leave a little machining allowance on the parts with higher requirements. It can be seen that the use of investment casting method can save a lot of machine tool equipment and processing man-hours, and greatly save metal raw materials.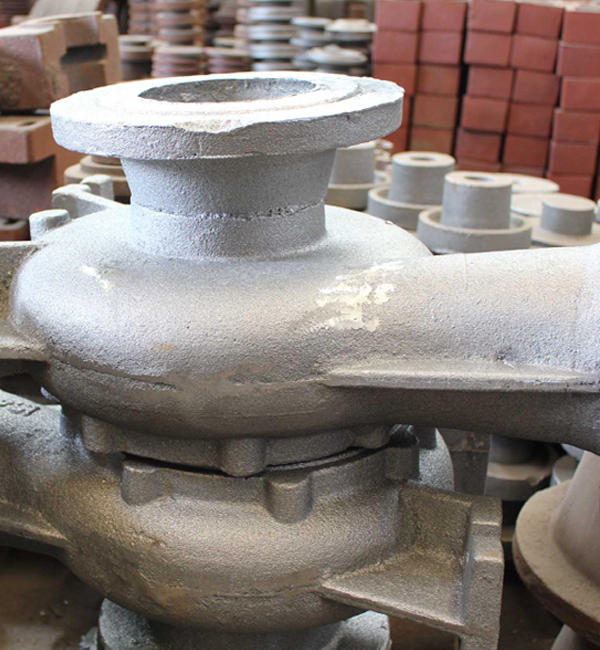
Lost Foam Casting
Lost foam casting is to combine paraffin wax or foam models similar to the casting size and shape into model clusters. After brushing and drying refractory coatings, they are buried in dry quartz sand for vibration modeling, and poured under negative pressure to gasify the model. , The liquid metal occupies the position of the model and forms a new casting method after solidification and cooling.

Die Casting
Die casting is a metal casting process, which is characterized by applying high pressure to the molten metal using the cavity of the mold. Molds are usually made of higher-strength alloys, and this process is somewhat similar to injection molding. Most die castings are iron-free, such as zinc, copper, aluminum, magnesium, lead, tin, and lead-tin alloys and their alloys. Minghe has been China's top die casting service since 1995.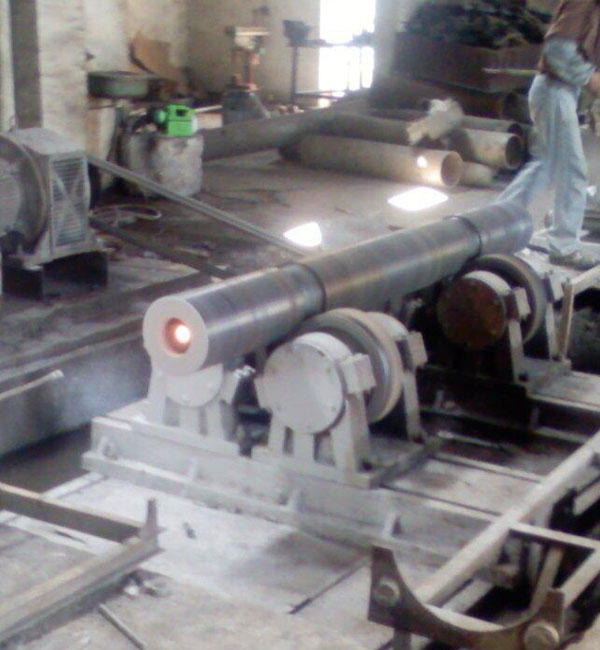
Centrifugal Casting
Centrifugal Casting is a technique and method of injecting liquid metal into a high-speed rotating mold, so that the liquid metal is centrifugal motion to fill the mold and form a casting. Due to the centrifugal movement, the liquid metal can fill the mold well in the radial direction and form the free surface of the casting; it affects the crystallization process of the metal, thereby improving the mechanical and physical properties of the casting.
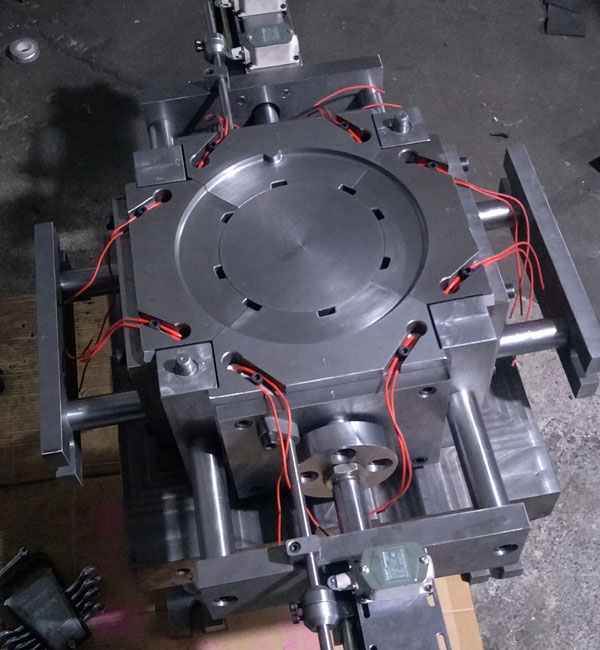
Low Pressure Casting
Low Pressure Casting means that the mold is generally placed above a sealed crucible, and compressed air is introduced into the crucible to cause a low pressure (0.06~0.15MPa) on the surface of the molten metal, so that the molten metal rises from the riser pipe to fill the mold and control Solidified casting method. This casting method has good feeding and dense structure, easy to cast large thin-walled complex castings, no risers, and a metal recovery rate of 95%. No pollution, easy to realize automation.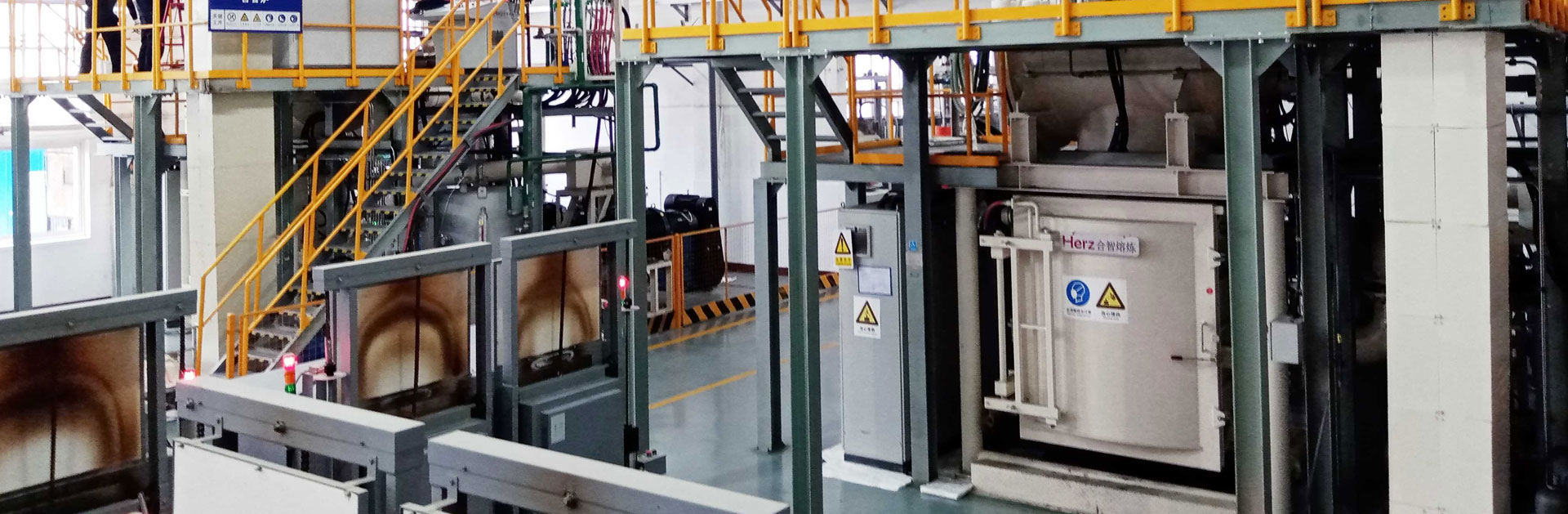
Vacuum Casting
Vacuum Casting is a casting process in which metal is smelted, poured and crystallized in a vacuum chamber. Vacuum casting can minimize the gas content in the metal and prevent metal oxidation. This method can produce very demanding special alloy steel castings and extremely easily oxidized titanium alloy castings. Minghe Casting has a vacuum casting sub-factory, which is enough to solve all the problems related to vacuum casting