What is Metal Trimming Process & Die Cutting & - Trimming Services
Trimming is the act of removing flash or burrs on the edge of the workpiece.Remove flash or burrs from rubber molded parts, plastic molded parts, metal castings, or the edges of workpieces.This process is an important process to ensure the size of automobile covering parts.The determination of the trimming line is the key to this process.
Minghe has an advanced trimming machine that uses the low-temperature freezing effect of liquid nitrogen to embrittle products made of rubber, plastic or zinc-magnesium-aluminum alloys. High-speed injection of polymer particles hits the product burrs to remove burrs with high efficiency and precision.
Minghe’s die cutting and trimming services were originally added to compliment and support our forming capabilities. Today, customers utilize our industry leading trimming services even when forming is not needed. For 35 years, we have been evolving our trimming services to provide customers with the right solutions to their specific application. Minghe engineers will review the product specifications, material call outs and volume requirements to select the most cost effective solution for your trimming project.
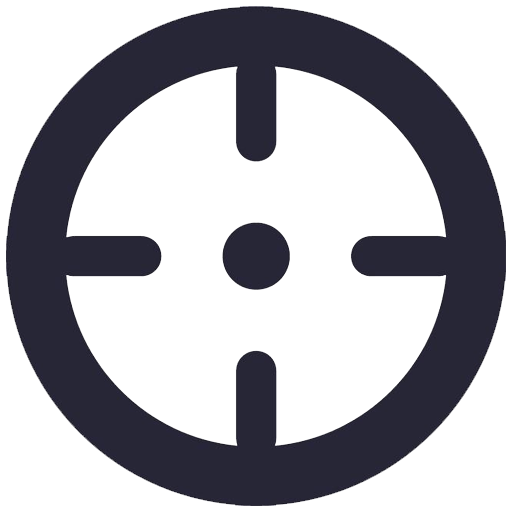
Benefits of Metal Trimming Process
The functions of metal trimming can be summarized as follows:
- – Simple operation: ordinary workers can operate the machine proficiently after half an hour of training, and there is an advanced automatic control system to prevent workers from misoperation.
- – High production efficiency: the average daily processing volume of a frozen trimming machine is equivalent to the trimming workload of 50-80 skilled workers
- – High precision of trimming: it can remove very small and hidden flash, not limited by the shape of the product, with high pass rate and stable trimming quality.
- – It can remove the flash from small rubber and plastic products of any shape, brittle plastic products and magnesium alloy, zinc alloy, and aluminum alloy castings with complex structure.
- – Do not damage the surface of the product, improve the appearance quality of the product, and increase the service life of the product.
- – It occupies a small area, only 4~10 square meters for a frozen trimming machine plus auxiliary equipment.
- – Reduce the cost of mold use and rubber material. The equipment does not need torn edges. It only requires the flash to be as thin as 0.2mm or less, the overflow groove is as small as possible, and the flash margin is only 1/5 of the tearing die -1/10.
- – Energy saving and environmental protection: The machine consumes extremely low energy and discharges other original components of nitrogen.
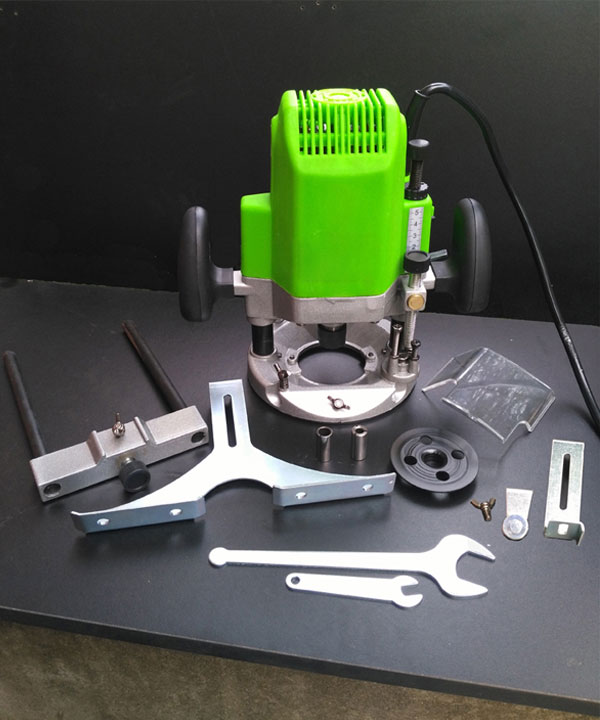
Different Types of Metal Finishes – Surface Treatment Services Available at Minghe
Do you want your die casting parts to be more corrosion-resistant or get a specific look? Metal finishing service is a essential choice to achieve your design perfectly. Minghe is an accomplished finished parts manufacturer, our workers and craftsman are capable to provide precision die casting services and a wide range of finishing services including aluminum anodizing, painting, passivation, electroplating, powder coating, polishing, black oxide, conversion coating, abrasive blasting, etc. Here are the introductions to different types of metal finishes, more details please feel free to contact us.
Powder coating/Powder coat ▶ |
Bead blasting/Bead blast ▶ |
Abrasive blasting/sandblasting▶ |
Choose the Best Trimming Process
After browsing a list of Surface Treatment services, select a process based on essential considerations, like production time, cost-effectiveness, part tolerance, durability and applications. High-tolerance CNC milling, turning parts are not recommended to apply secondary metal surface finish, because the treatment may change the sizes of the finished part through removing or adding a small amount of materials.
Contact us or Email sales@hmminghe.com to see how our people, equipment and tooling can bring the best quality for the best price for your trimming project.