Vacuum Die Casting
What is Vacuum Die Casting
Vacuum die-casting method is an advanced die-casting process that eliminates or significantly reduces the pores and dissolved gases in the die-casting parts by removing the gas in the die-casting mold cavity during the die-casting process, thereby improving the mechanical properties and surface quality of the die-casting parts.
Recently, vacuum aluminum alloy die casting is mainly used to remove the gas in the cavity, and there are two main forms:
- - Pump air directly from the mold;
- - Place the mold in a vacuum box to pump air. When vacuum aluminum alloy die-casting is used, the design of the exhaust duct position and the exhaust duct area of the mold is very important. There is a "critical area" in the exhaust duct, which is related to the amount of gas pumped out in the cavity, the pumping time and the filling time. When the area of the exhaust duct is larger than the critical area, the vacuum aluminum alloy die-casting effect is obvious; on the contrary, it is not obvious.
The choice of the vacuum system is also very important. It is required that the vacuum in the cavity can be maintained until the filling is completed before the vacuum pump is turned off. The gas in the pores of the oxygen-filled die-casting technology is mostly N2 and H2, and there is almost no O2. The main reason is that O2 reacts with active metals to form solid oxides, which provides a theoretical basis for the oxygen-filled die-casting technology. Oxygen-filled die-casting is to fill the cavity with oxygen before die-casting to replace the air in it.
Since pressure casting completes the filling process in a very short time, it is easy to cause gas to be involved and affect the quality of the die casting. For this reason, oxygen-added die-casting machines and vacuum die-casting machines have been developed, and medium-pressure die-casting machines have also achieved rapid development. Some die-casting machines have an inclined form of forming mechanism. Die-casting process automation and die-casting computer control and die-casting flexible machining unit (FMC) have also been gradually developed.
- - Oxygen pressure casting is to fill the pressure chamber and the cavity with oxygen before the aluminum metal liquid fills the cavity to replace the air and other gases. Its characteristics are: eliminate or reduce pores, improve the quality of castings; simple structure, convenient operation, and low investment.
- - Vacuum pressure casting first removes the air from the die-casting cavity, and then presses into the liquid metal. Its characteristics are: it can eliminate or reduce the pores inside the die casting, improve the mechanical properties and surface quality of the casting; greatly reduce the back pressure of the cavity during die casting, and can use alloys with lower specific pressure and poor casting performance.
The Advantages And Disadvantages Of Vacuum Die Casting
Advantages of vacuum die casting
- - The vacuum die casting method can eliminate or reduce the pores inside the die casting, improve the mechanical properties and surface quality of the die casting, and improve the plating performance;
- - The vacuum die-casting method greatly reduces the back pressure of the cavity. Lower specific pressure and alloys with poor casting properties can be used, and it is possible to die-cast larger castings with small machines;
- - The vacuum die-casting method improves the filling conditions and can die-cast thinner castings;
- - Compared with the ordinary die-casting method, the vacuum die-casting method has almost the same production efficiency.
Disadvantages of vacuum die casting
- - The mold sealing structure is complicated, and it is difficult to manufacture and install, so the cost is high;
- - If the vacuum die-casting method is not properly controlled, the effect will not be very significant.
Comparison Of Vacuum Die Casting and Ordinary Die Casting
- - The porosity is greatly reduced;
- - The hardness of vacuum die-casting castings is high, and the microstructure is fine;
- - The mechanical properties of vacuum aluminum alloy die castings are relatively high.
Aluminum-magnesium alloy die-castings produced by vacuum die-casting method have been proved to be able to use welding, heat treatment and other processing methods, and the room temperature performance has also been improved: for example, the vacuum die-casting method has been successfully used to produce AM60B magnesium alloy automobile wheels on the cold-chamber die-casting machine. , The AM60B magnesium alloy automobile steering wheel was produced by vacuum die casting on a hot chamber die casting machine with a clamping force of 2940kN, and the elongation of the die casting was increased from 8% to more than 16%.
As long as it is properly controlled, the vacuum die casting method can bring satisfactory improvements to the performance of die castings. The cost increase caused by mold sealing will be well solved with the popularization of technology and the cost sharing caused by mass production.
Compared with the traditional die-casting method, the laminar filling method/ultra-low-speed die-casting method has lower production efficiency and difficult gate cleaning, which is difficult to apply to mass production; the oxygen-filled die-casting method has complicated operating procedures, and the process parameters are difficult to control and difficult to control. Large-scale application in actual production; only the vacuum die-casting method, the process is simple, the operation is convenient, and the production efficiency is almost the same as that of the ordinary die-casting method, and it is easy to popularize in actual production. Therefore, since its appearance, the vacuum die-casting method has shown strong vitality, and with the improvement of related technologies, its application has become more and more extensive.
Different Types Production Scenario Of Vacuum Casting
Minghe always adheres to the customer's requirements and the company's service standards. In any link of mold design, mold assembly, mold debugging, mold trial production, casting process, etc., there are dedicated engineers to keep you on the phone;
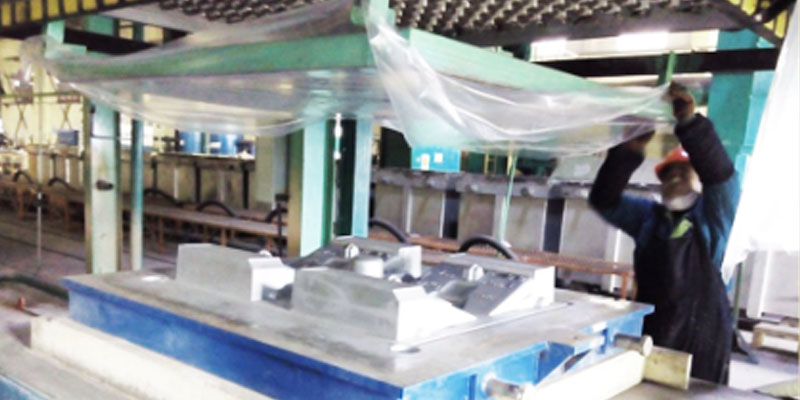
1.Model▶ |
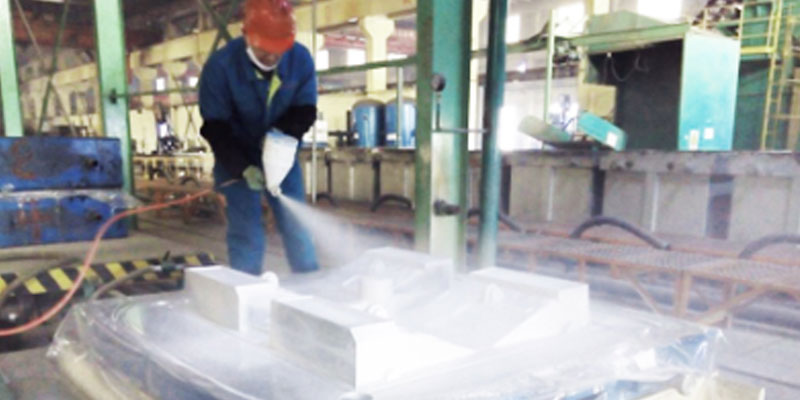
2.Film-Heating ▶ |
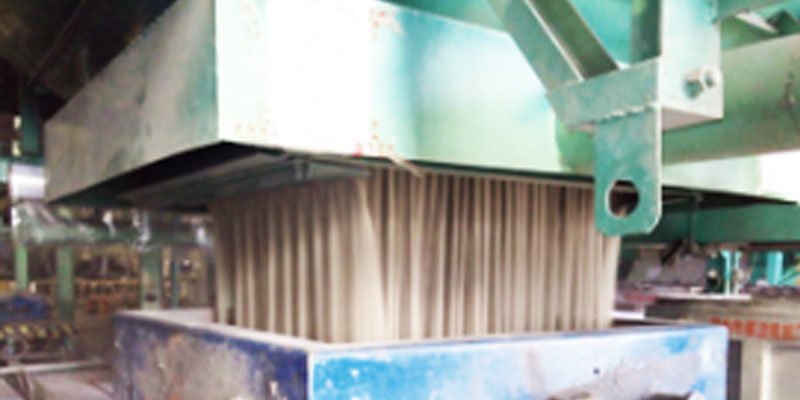
3.Film Forming ▶ |
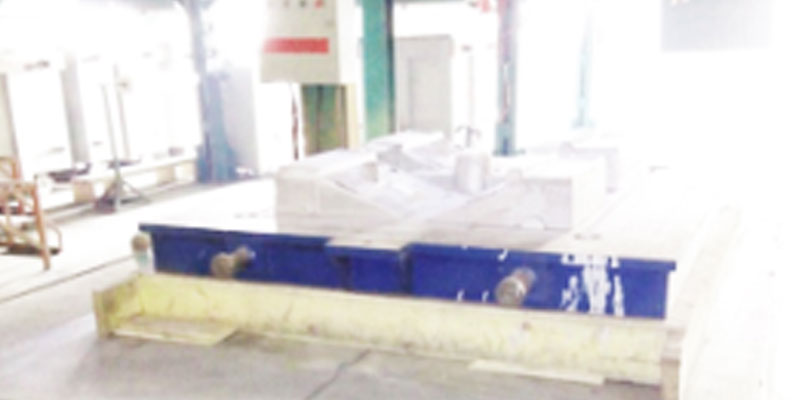
4.Put the Sand Box▶ |
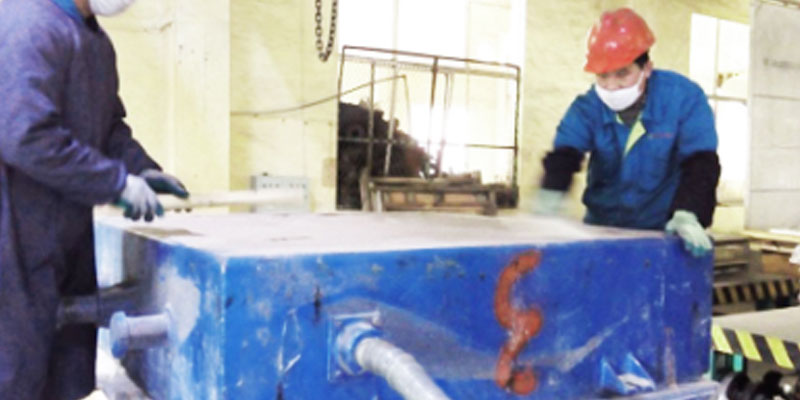
5.Drawing▶ |
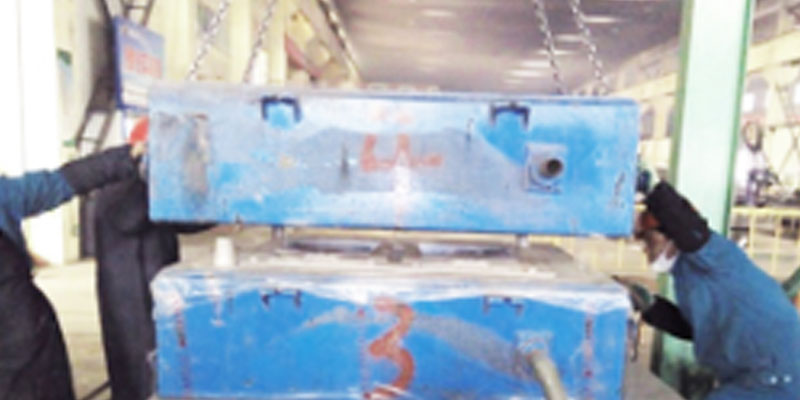
6.Shaking Off The Box▶ |
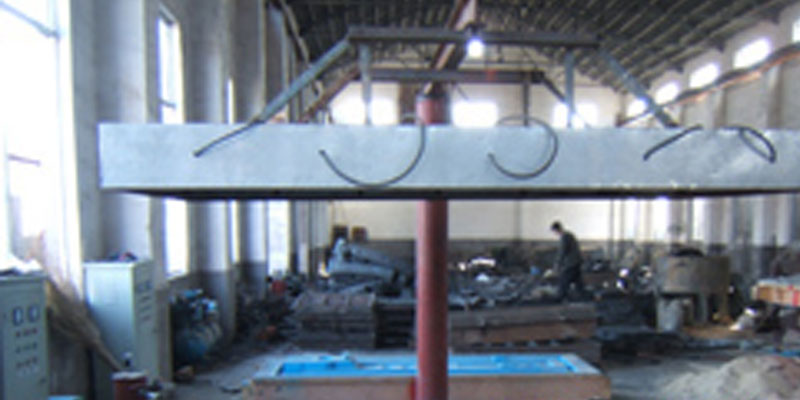
7.Boiler ▶ |
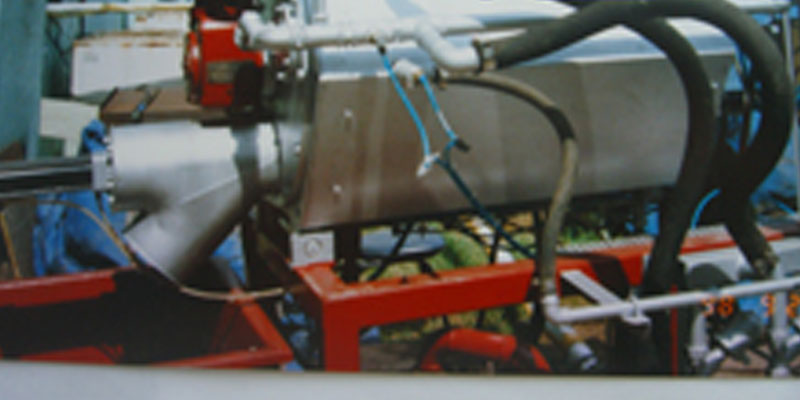
8.Foaming Machine▶ |
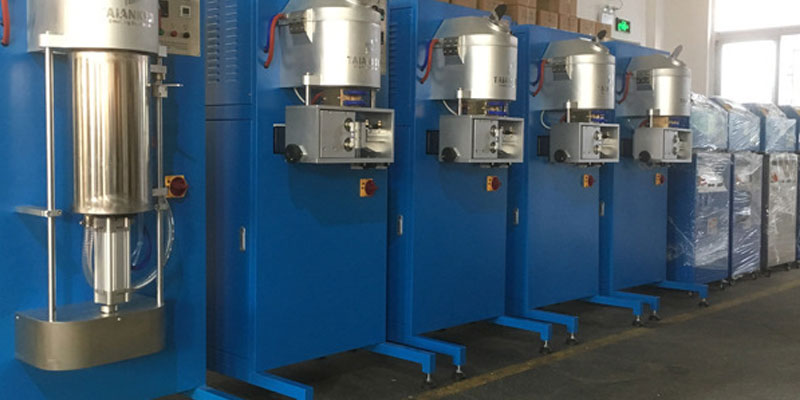
9.Intelligent Continuous Casting▶ |
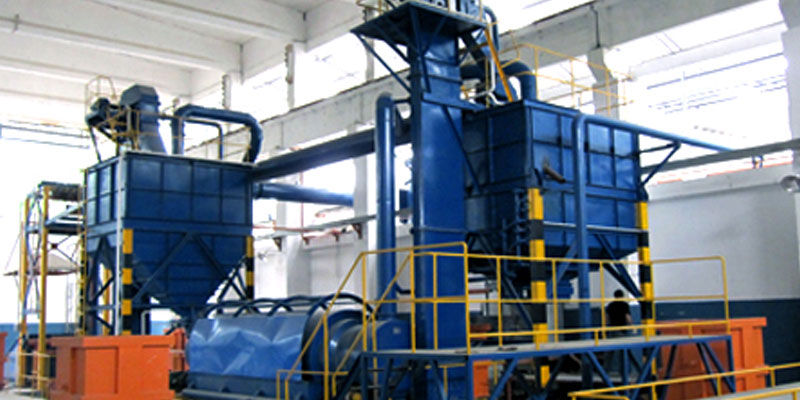
10.Vacuum Casting Machine▶ |
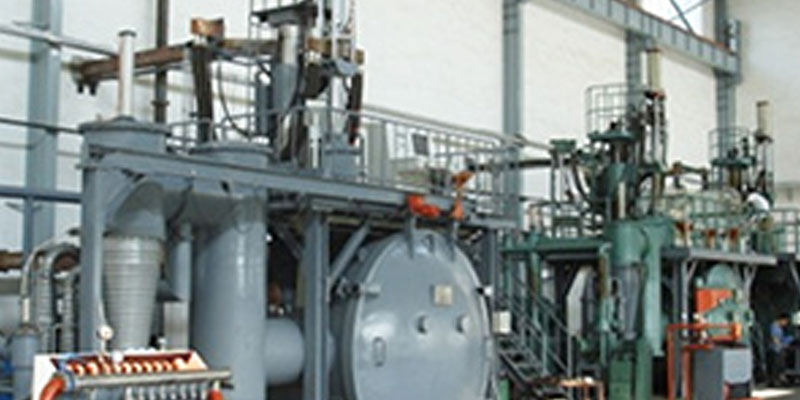
11.Vacuum Casting Machine▶ |
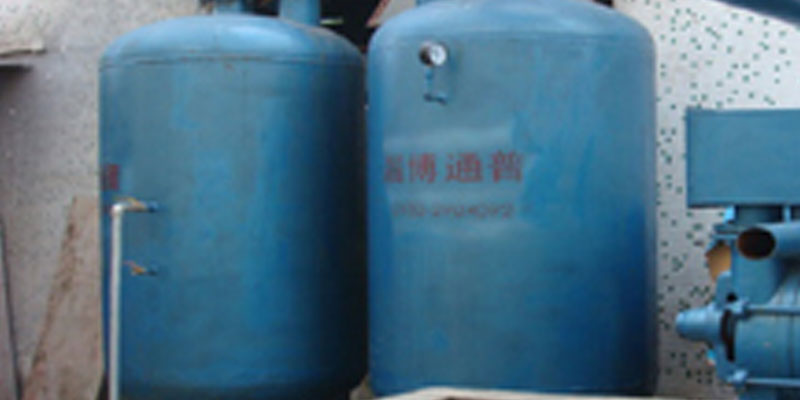
12.Vacuum System▶ |
The Minghe Case Studies Of Vacuum Casting
Minghe Casting fabrication services are available for both design to reality and low to high volume production runs of your die casting parts,sand casting parts,investment casting parts,metal casting parts, lost foam casting parts and more.
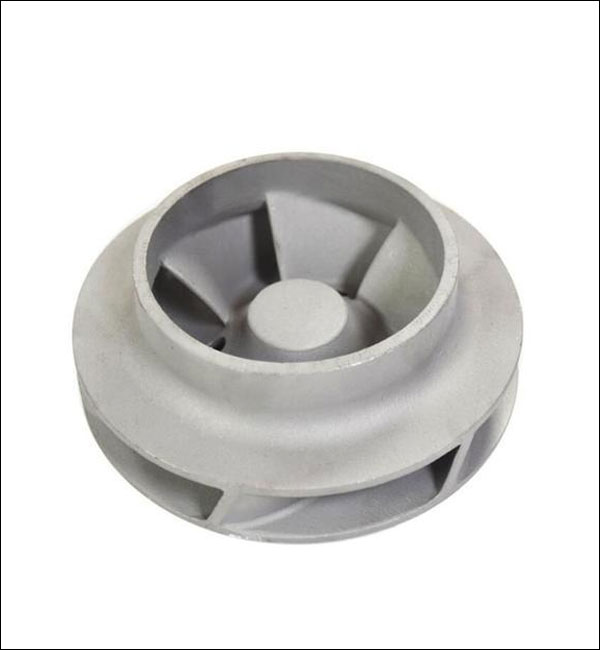
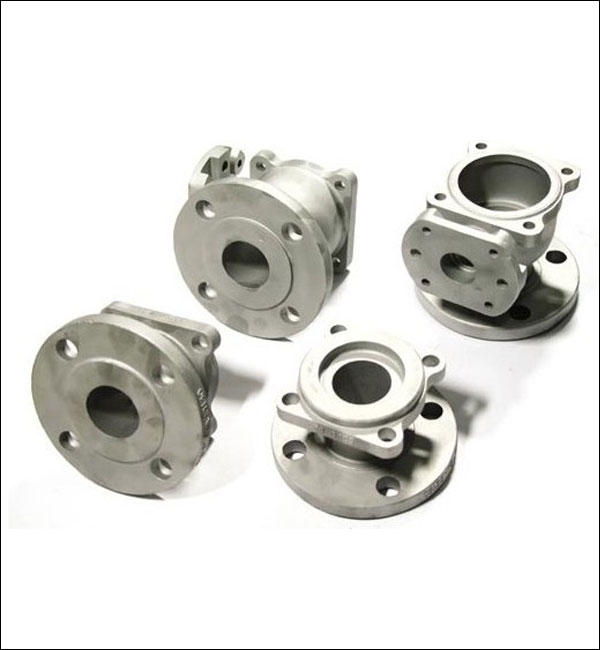
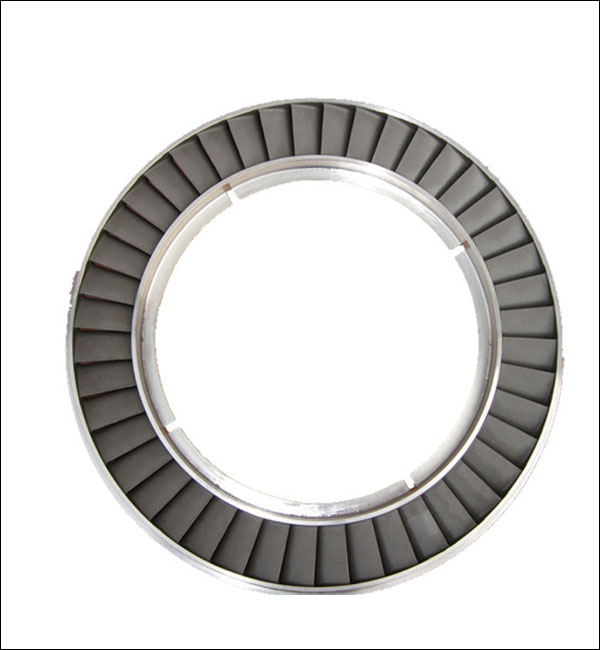
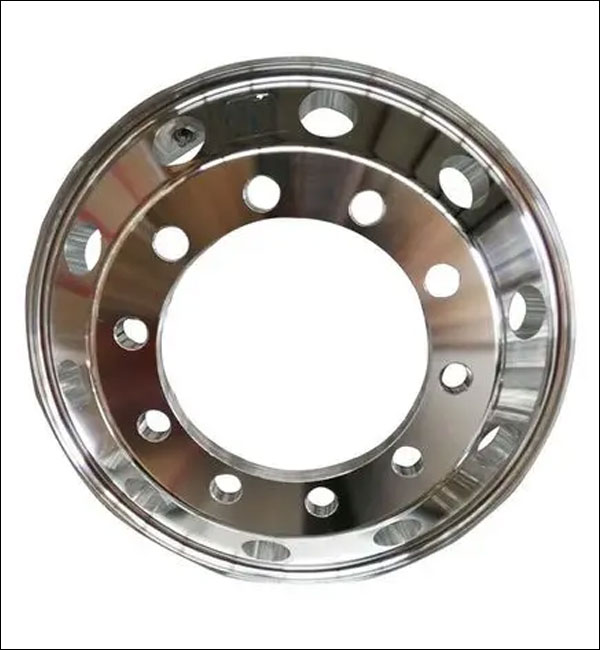

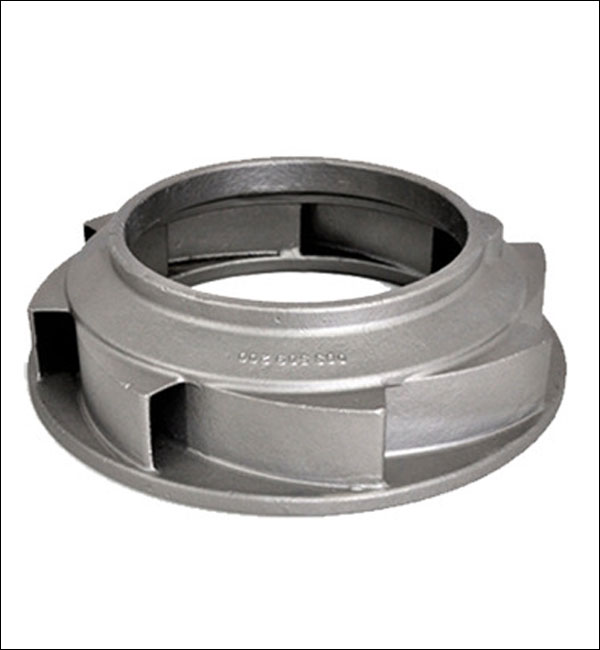
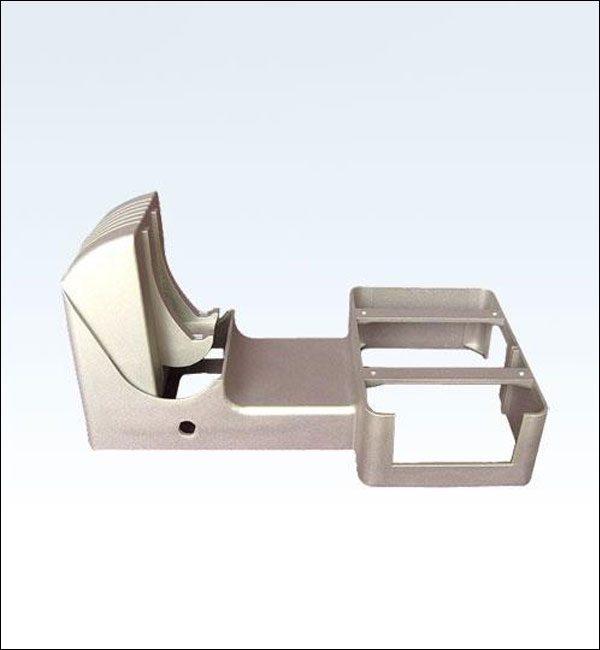
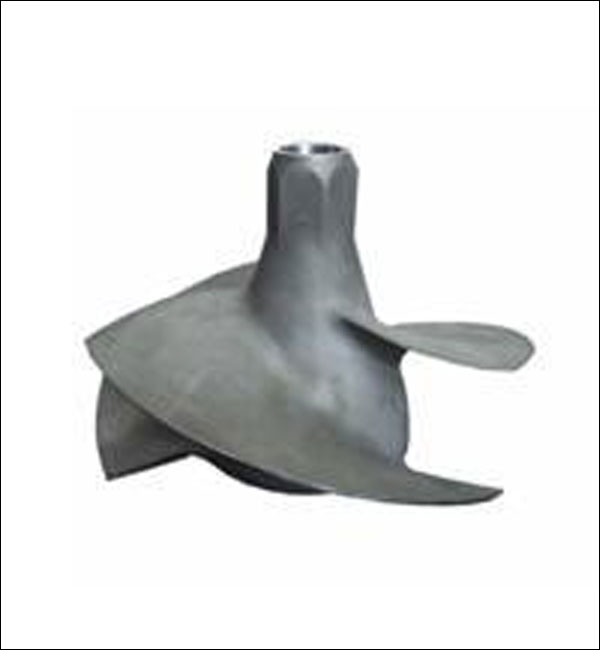
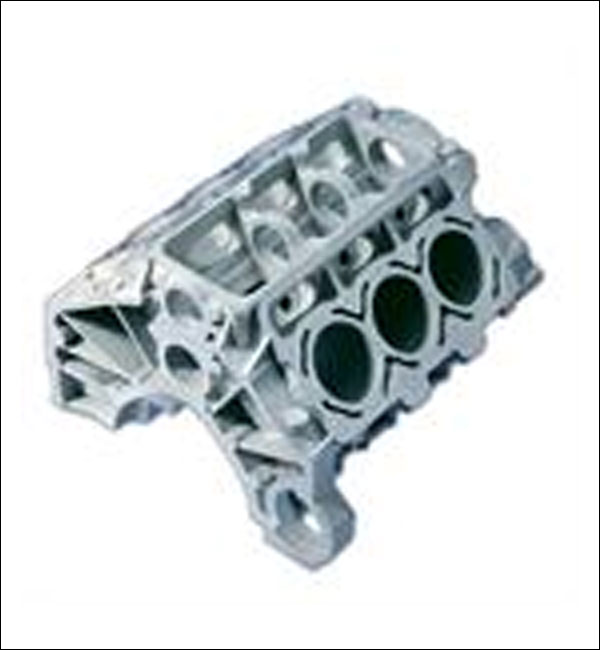
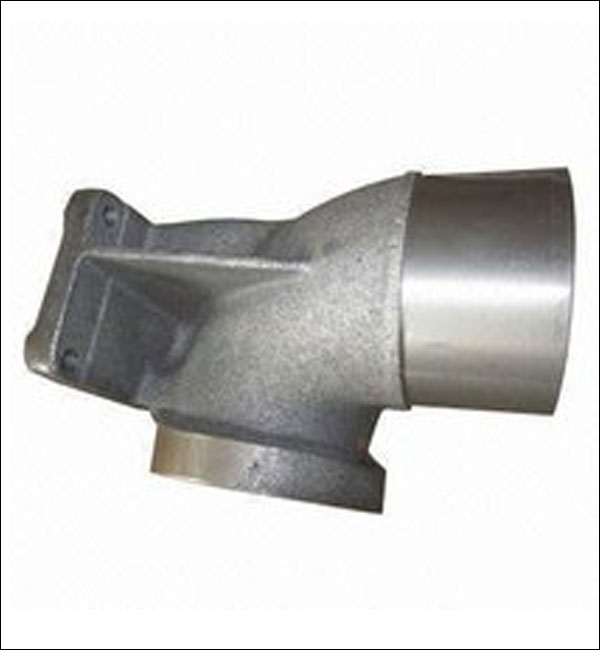

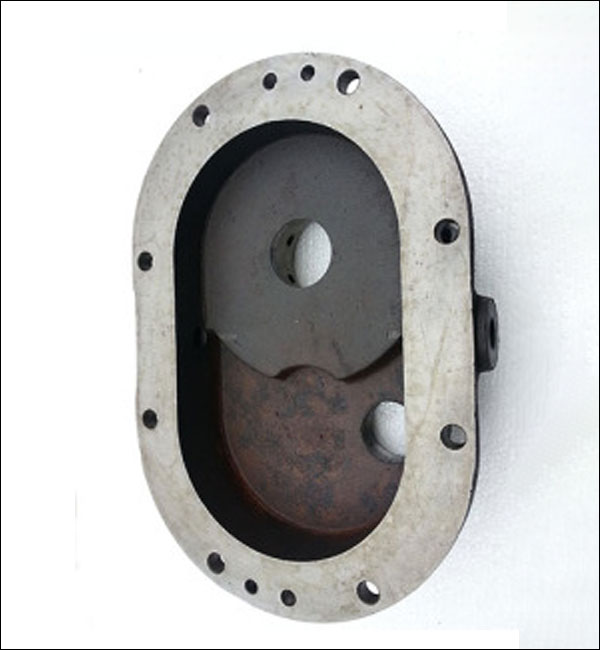
Go To View More Casting Parts Cases Studies >>>
Choose the Best Vacuum Casting Supplier
Currently, our vacuum casting parts are exported to America, Canada, Australia, United Kingdom, Germany, France, Sout Africa, and many other countries all over the world. We are ISO9001-2015 registered and also certified by SGS.
Our custom vacuum casting fabrication service provides durable and affordable castings that meet your specifications for automotive, medical, aerospace, electronics, food, construction, security, marine, and more industries. Fast to send your inquiry or submit your drawings to get a free quote in the shortest time.Contact us or Email sales@hmminghe.com to see how our people, equipment and tooling can bring the best quality for the best price for your vacuum casting project.
We Provide Casting Services Include:
Minghe Casting services working with sand casting、metal casting 、investment casting lost foam casting, and more.

Sand Casting
Sand Casting is a traditional casting process that uses sand as the main modeling material to make molds. Gravity casting is generally used for sand molds, and low-pressure casting, centrifugal casting and other processes can also be used when there are special requirements. Sand casting has a wide range of adaptability, small pieces, large pieces, simple pieces, complex pieces, single pieces, and large quantities can be used.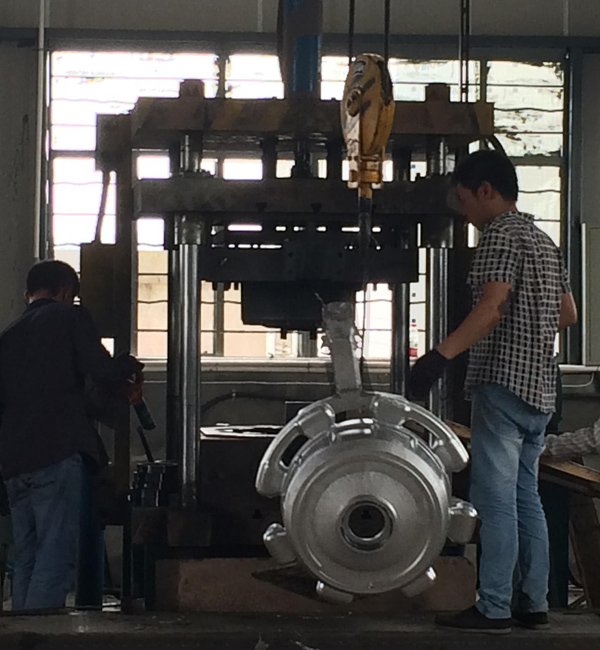
Permanent Mold Casting
Permanent Mold Casting have a long life and high production efficiency, not only have good dimensional accuracy and smooth surface, but also have higher strength than sand castings and are less likely to be damaged when the same molten metal is poured. Therefore, in the mass production of medium and small non-ferrous metal castings, as long as the melting point of the casting material is not too high, metal casting is generally preferred.
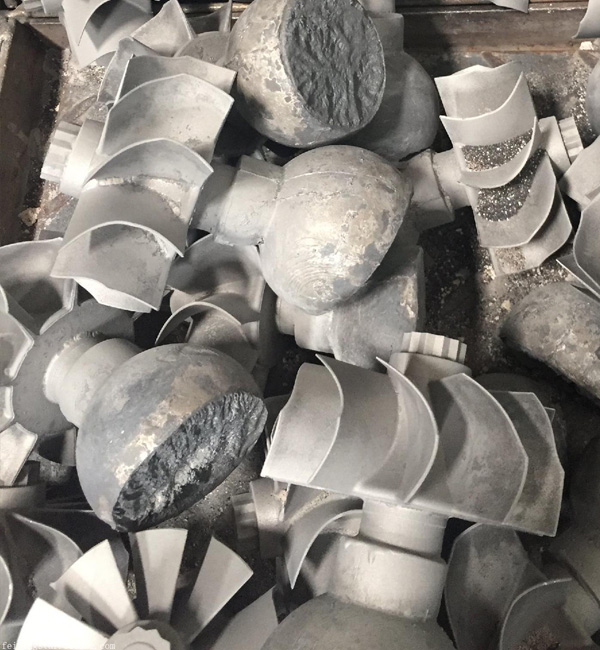
Investment Casting
The biggest advantage of investment casting is that because investment castings have high dimensional accuracy and surface finish, they can reduce machining work, but leave a little machining allowance on the parts with higher requirements. It can be seen that the use of investment casting method can save a lot of machine tool equipment and processing man-hours, and greatly save metal raw materials.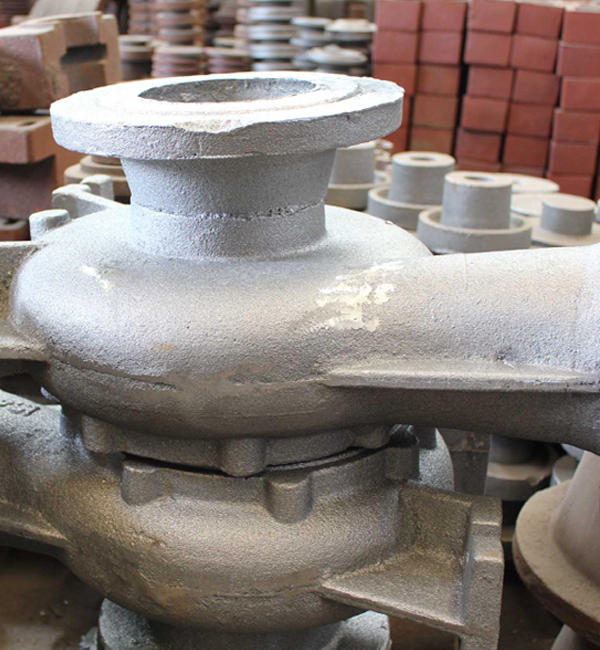
Lost Foam Casting
Lost foam casting is to combine paraffin wax or foam models similar to the casting size and shape into model clusters. After brushing and drying refractory coatings, they are buried in dry quartz sand for vibration modeling, and poured under negative pressure to gasify the model. , The liquid metal occupies the position of the model and forms a new casting method after solidification and cooling.

Die Casting
Die casting is a metal casting process, which is characterized by applying high pressure to the molten metal using the cavity of the mold. Molds are usually made of higher-strength alloys, and this process is somewhat similar to injection molding. Most die castings are iron-free, such as zinc, copper, aluminum, magnesium, lead, tin, and lead-tin alloys and their alloys. Minghe has been China's top die casting service since 1995.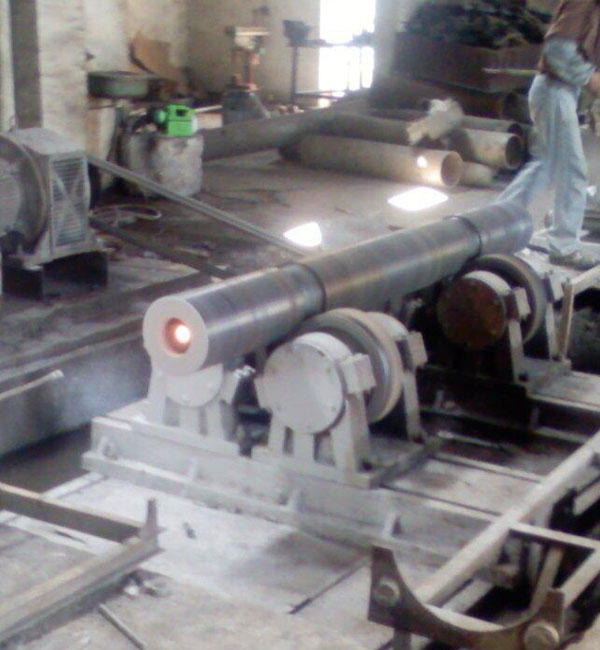
Centrifugal Casting
Centrifugal Casting is a technique and method of injecting liquid metal into a high-speed rotating mold, so that the liquid metal is centrifugal motion to fill the mold and form a casting. Due to the centrifugal movement, the liquid metal can fill the mold well in the radial direction and form the free surface of the casting; it affects the crystallization process of the metal, thereby improving the mechanical and physical properties of the casting.
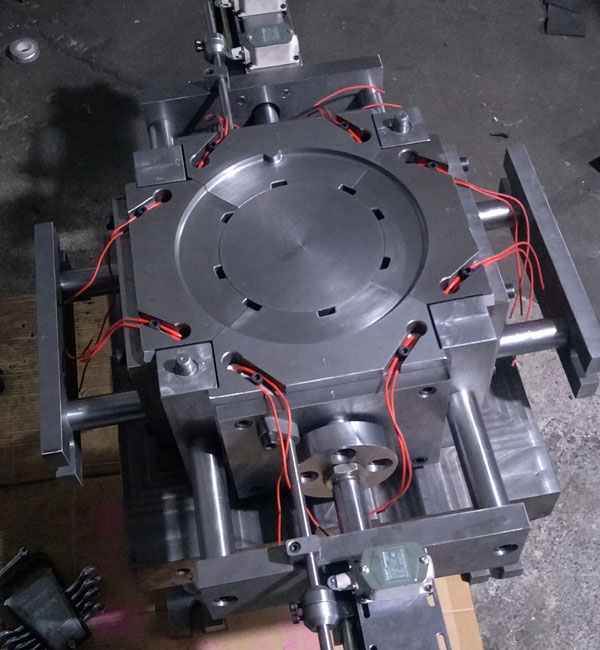
Low Pressure Casting
Low Pressure Casting means that the mold is generally placed above a sealed crucible, and compressed air is introduced into the crucible to cause a low pressure (0.06~0.15MPa) on the surface of the molten metal, so that the molten metal rises from the riser pipe to fill the mold and control Solidified casting method. This casting method has good feeding and dense structure, easy to cast large thin-walled complex castings, no risers, and a metal recovery rate of 95%. No pollution, easy to realize automation.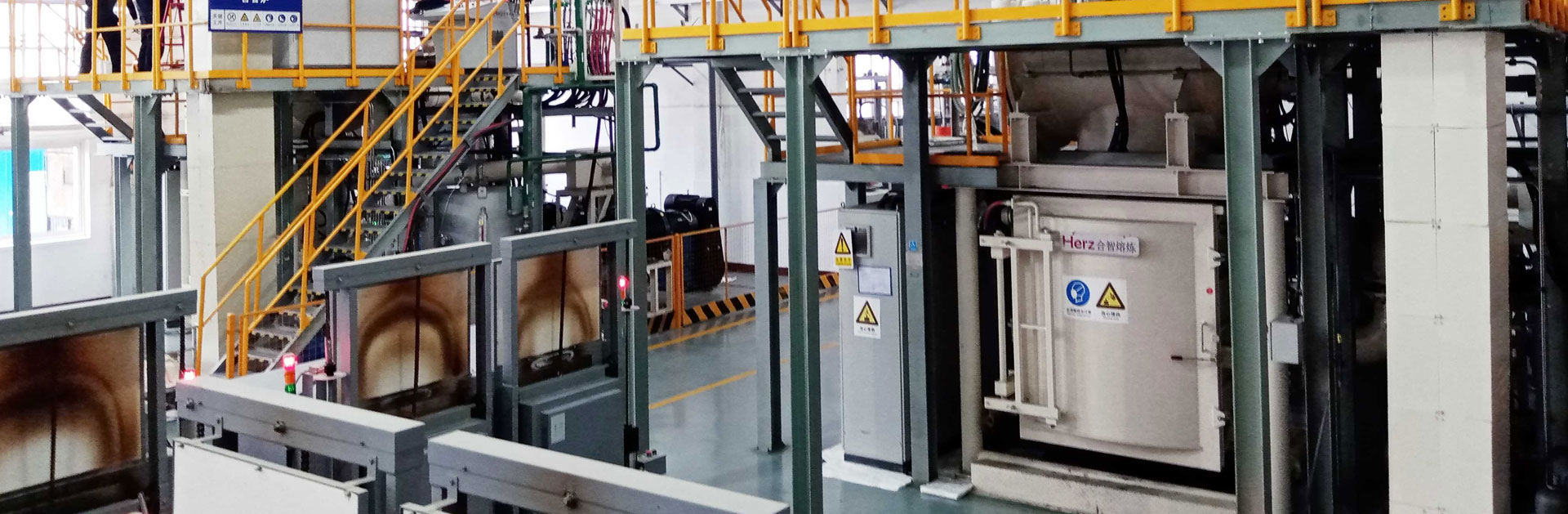
Vacuum Casting
Vacuum Casting is a casting process in which metal is smelted, poured and crystallized in a vacuum chamber. Vacuum casting can minimize the gas content in the metal and prevent metal oxidation. This method can produce very demanding special alloy steel castings and extremely easily oxidized titanium alloy castings. Minghe Casting has a vacuum casting sub-factory, which is enough to solve all the problems related to vacuum casting