Zinc Casting
What Is Zinc Die Casting?
Zinc alloy die casting is a kind of precision casting method, which uses high pressure to force the metal to melt into the complex metal mold.
The design and development of zinc alloy die casting mold, die casting is a kind of precision casting method, which uses high pressure to force the metal melt into the complex metal mold. In China, the zinc alloy die casting industry is mainly concentrated in the Pearl River Delta and Wenzhou, Zhejiang Province, but in terms of technology maturity and the whole post-processing level, the Pearl River Delta is still far stronger than Wenzhou. Industry analysis, do high-quality zinc alloy products preferred Dongguan die-casting factory, Dongguan die-casting factory and small processing plant with incomplete statistics up to 1000! In the domestic die casting industry row first! Due to the low threshold of the industry, to a certain extent, die-casting processing plants are a bit rampant in Dongguan. Some of them are engaged in die-casting processing after their families get a few rooms and some equipment. However, many companies have gradually become industry benchmarks. Zinc alloy die casting is no better than other molding process. If you want to make a good die casting product, you can't have a good die casting machine. You must combine the mold, die casting machine and die casting process to make a good product.
China Advance Zinc Die Casting Service
If you are seeking a professional zinc die casting supplier to provide high quality precision zinc die casting parts, Minghe Casting is one of the most affordable and capable manufacturer, specializing in high pressure casting process on advanced 200T and 1650T die casting machines. Our professional technical team has in-depth understanding of special zinc die casting parts requirements (especially custom jewelry industry, Automobile industry, electronic industry, wireless charging industry, dash cam industry, recorder industry, Bluetooth speaker industry, smart watch industry, smart home industry) and other than the alyuminium parts, and state-of-the art facility has helped us achieve this distinction. With great experience and broad knowledge, our zinc die casting center can reach extremely tight tolerances in manufacturing zinc parts & products.

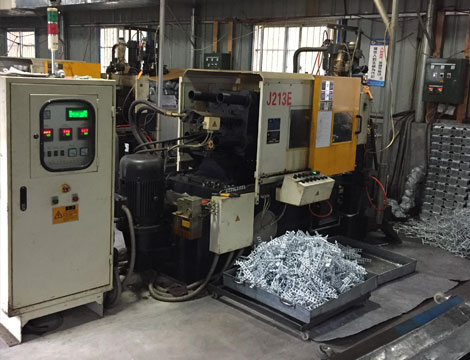
Benefits of Zinc Die Casting
- It's bigger than weight, has more texture than weight, and has more strength than plastic injection molding.
- Good casting performance, can die-casting complex shape, thin-walled precision parts, casting surface is smooth.
- Surface treatment: electroplating, spraying and painting.
- No iron absorption, no corrosion, no die sticking during melting and die casting.
- Good room temperature mechanical properties and wear resistance.
- Low melting point, melting at 385 ℃, easier to form than aluminum alloy die casting
Advantages of Zinc Die Casting
- Great precision and high tolerance ensure high-quality zinc die casting parts
- Time and cost-saving, great speed of Zinc Die Casting part
- Allows products ordered to be made precisely to the specifications stated
- Complex zinc die casting parts for high tech industry can be machined
Diecastingcompany.com – Zinc Die Casting Specialist
Minghe Die Casting Company is one of the reliable precision zinc die casting parts manufacturer in the China. Our years professional zinc die casting center provide you all-around care services that our experienced project engineers and machinists will analyze your project carefully and process it with the most efficient process of die casting zinc to to meet your design specification, while optimize your time and cost.
Product Description Of Our Zinc Casting Services
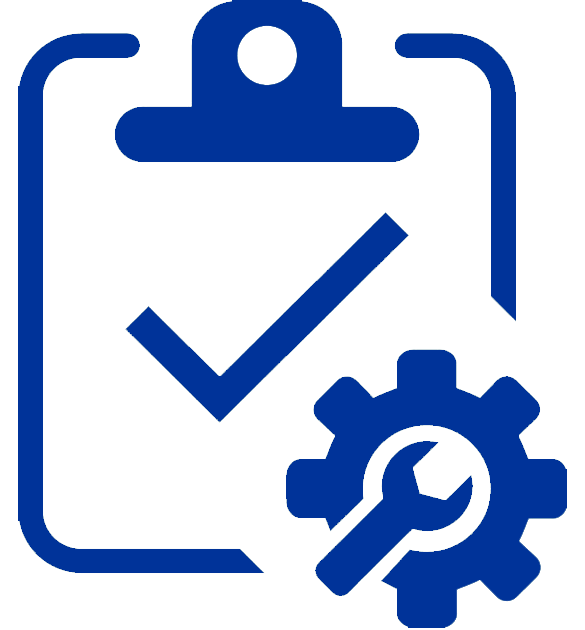
Traditional die casting 2, 3, 4, 5, 7 zinc alloy and high aluminum zinc base alloy za-8, ZA-12, ZA-27.
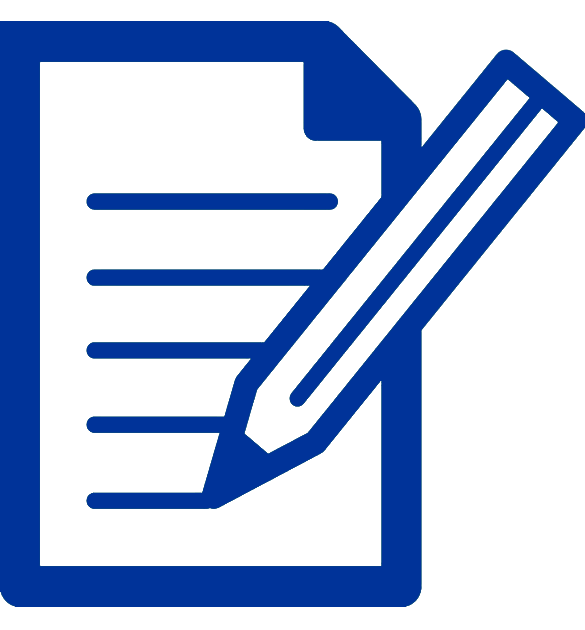
Black, Natural, Blue, Green and different colors as your requirements
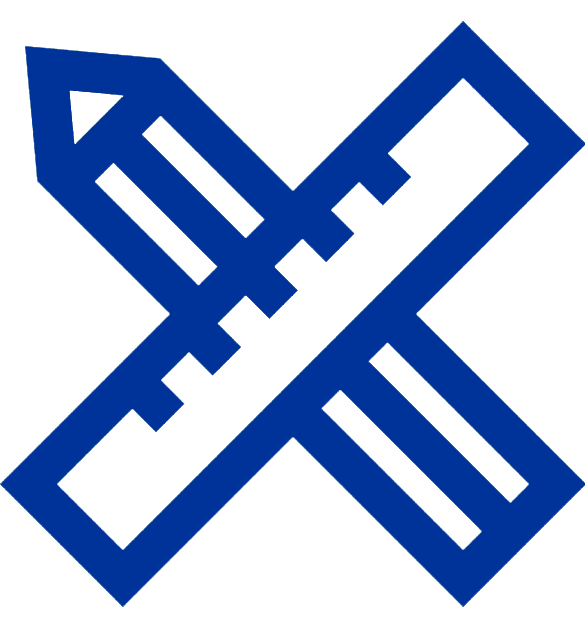
Sand blasting, shot blasting, polishing, anodizing, oxidation, electrophoresis, chromate, powder coating and painting
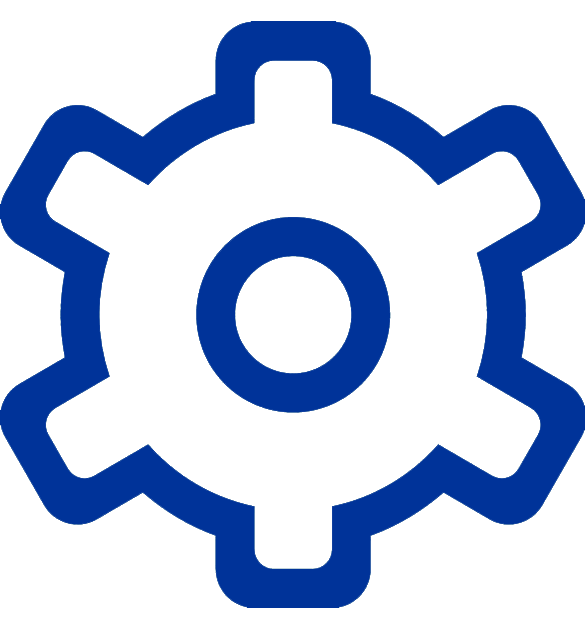
CNC milling, CNC turning, CNC drilling,
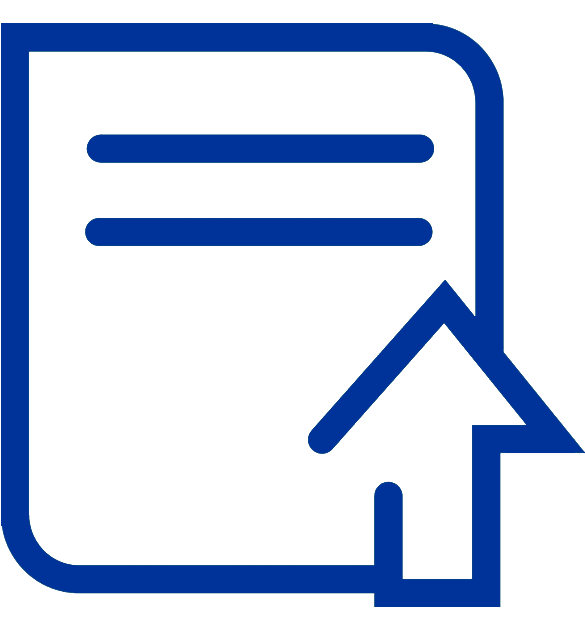
Zinc die casting parts can be applied to jewelry, Automobile, electronic, wireless charging, dash cam, recorder, Bluetooth speaker, smart watch, smart home
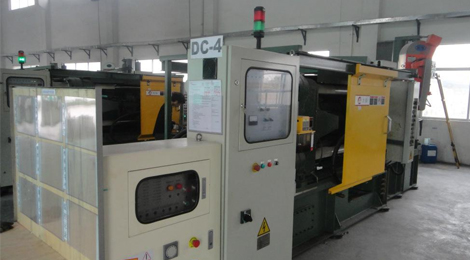
Advantages of Minghe Zinc Die Casting Services
- Experience, accuracy, and powerful machinery
- Relatively stable casting of Zinc
- Design and produce complex custom zinc parts
- High production efficiency and cost saving
- Simultaneously realize various and large quantities of production
- Provides the clients with a high quality part in a comparable timeline
- Timely shipment, one-stop instant service
The Minghe Case Studies Of Zinc Casting
You have a complex part design, Minghe Casting Company can help you turn it into a reality. With the right equipment, strong technical knowledge, and a focus on quality.. From tool design to finishing and then on to shipment, Minghe Casting ensure that every project is completed to a high standard and that your orders are delivered on time, every time.
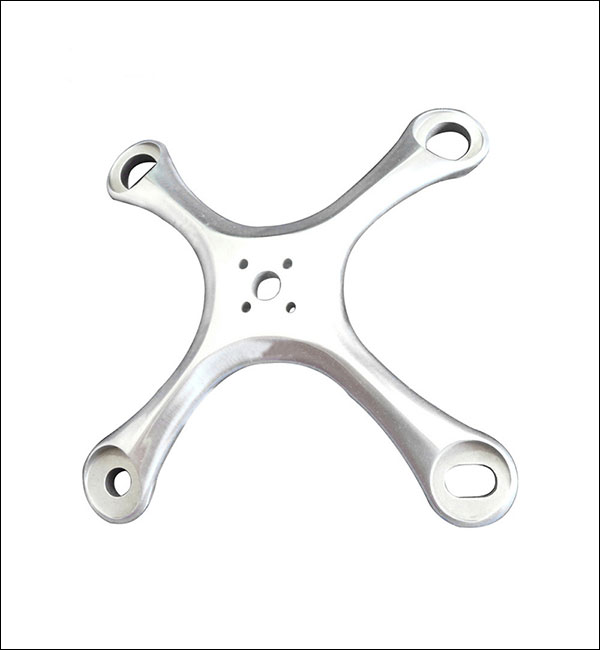
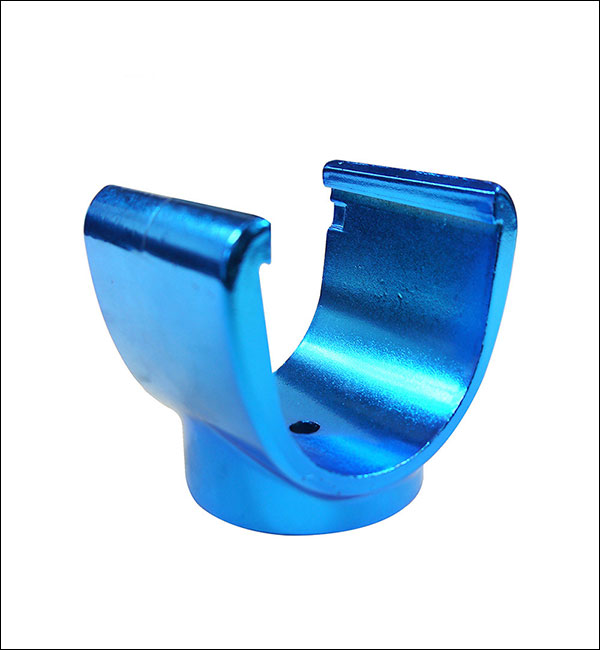
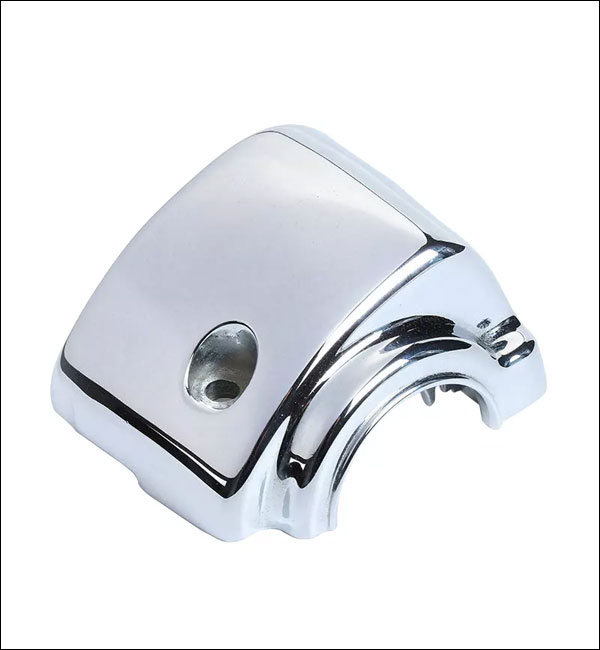

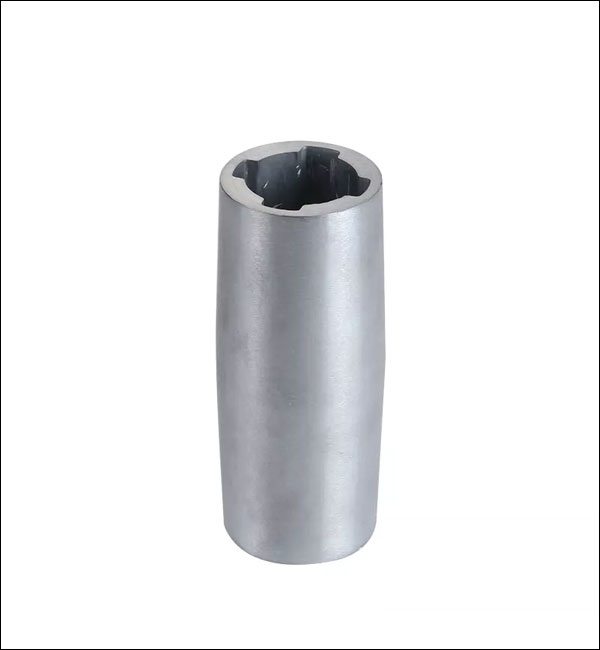
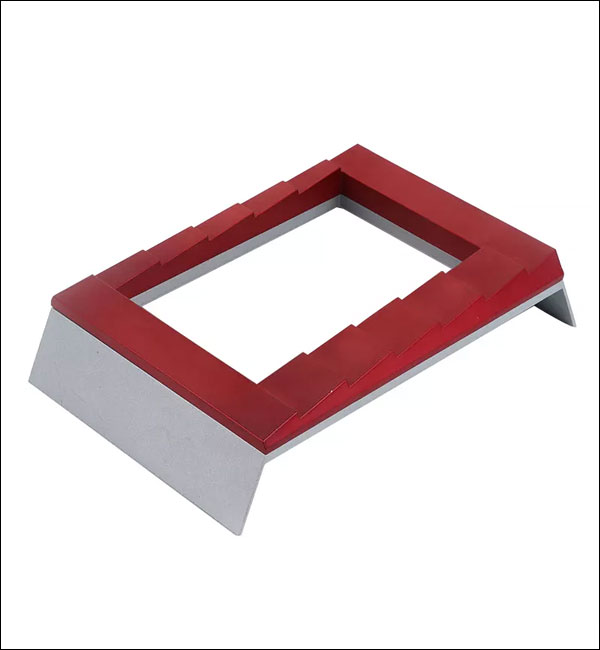
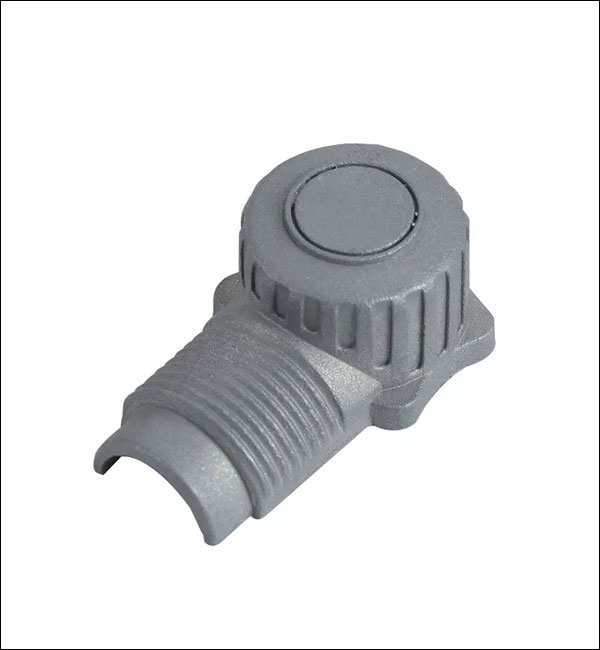
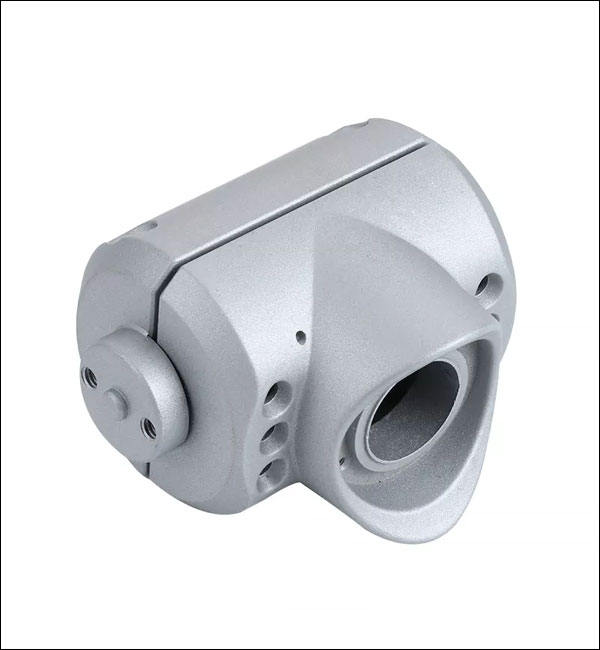
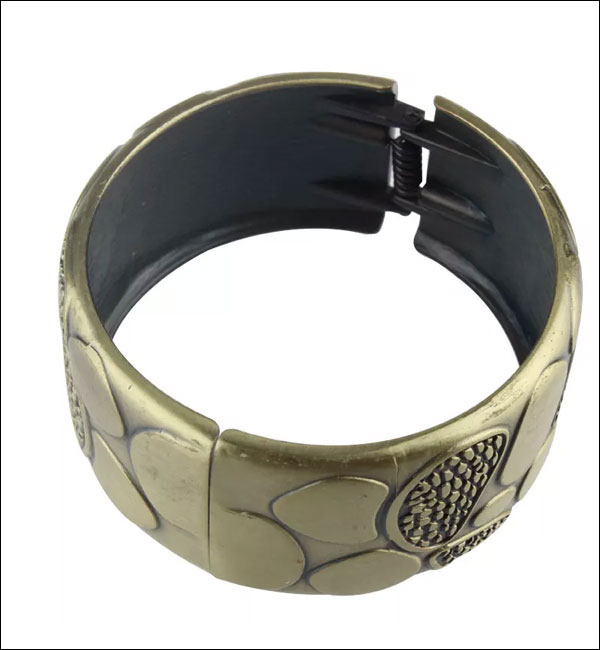
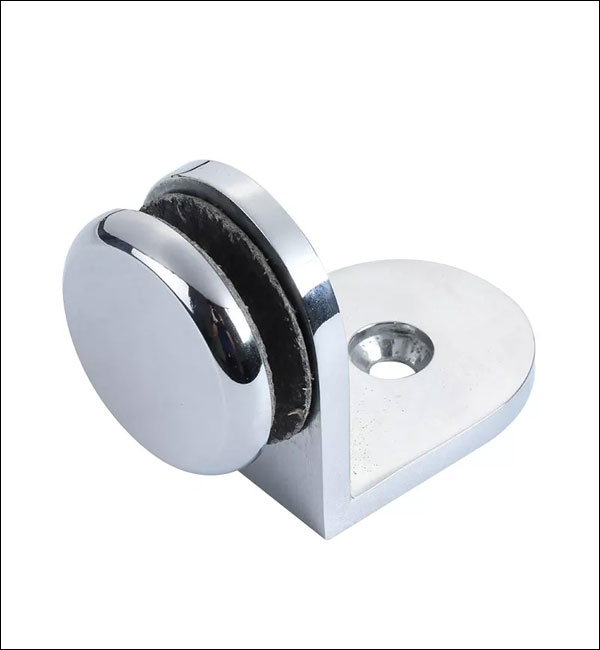
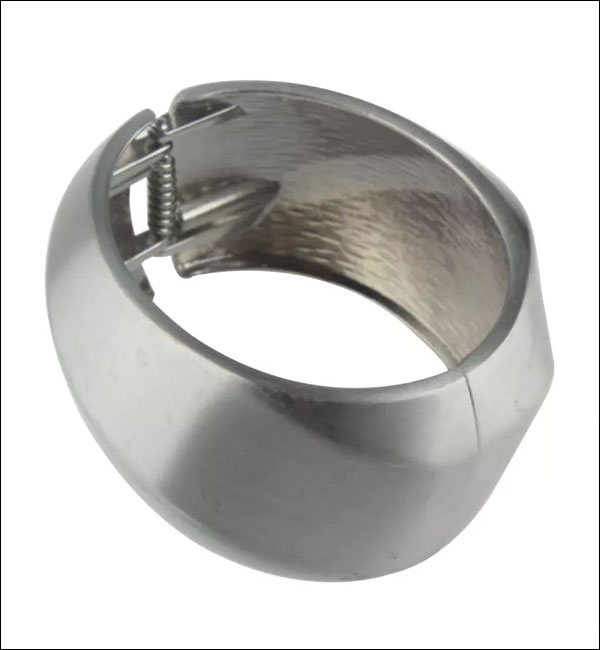
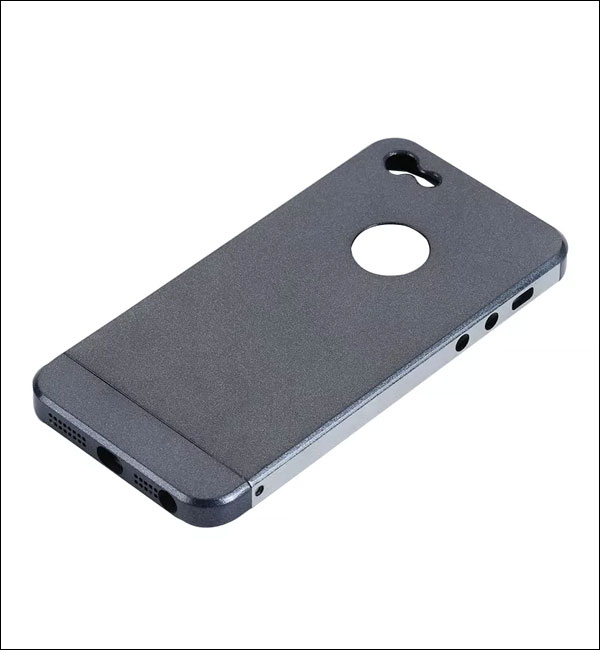
Go To View More Casting Parts Cases Studies >>>
Choose The Best Zinc Casting Service
Currently, our zinc casting parts are exported to America, Canada, Australia, United Kingdom, Germany, France, Sout Africa, and many other countries all over the world. We are ISO9001-2015 registered and also certified by SGS.
Custom china casting service provides durable and affordable castings that meet your specifications for automotive, medical, aerospace, electronics, food, construction, security, marine, and more industries. Fast to send your inquiry or submit your drawings to get a free quote in the shortest time.Contact us or Email sales@hmminghe.com to see how our people, equipment and tooling can bring the best quality for the best price for your zinc casting project.
We Provide Casting Services Include:
Minghe Casting services working with sand casting、metal casting 、investment casting lost foam casting, and more.

Sand Casting
Sand Casting is a traditional casting process that uses sand as the main modeling material to make molds. Gravity casting is generally used for sand molds, and low-pressure casting, centrifugal casting and other processes can also be used when there are special requirements. Sand casting has a wide range of adaptability, small pieces, large pieces, simple pieces, complex pieces, single pieces, and large quantities can be used.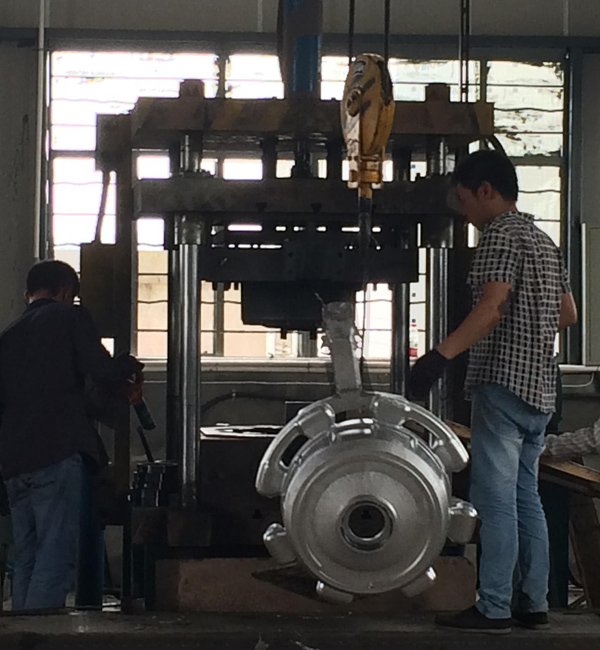
Permanent Mold Casting
Permanent Mold Casting have a long life and high production efficiency, not only have good dimensional accuracy and smooth surface, but also have higher strength than sand castings and are less likely to be damaged when the same molten metal is poured. Therefore, in the mass production of medium and small non-ferrous metal castings, as long as the melting point of the casting material is not too high, metal casting is generally preferred.
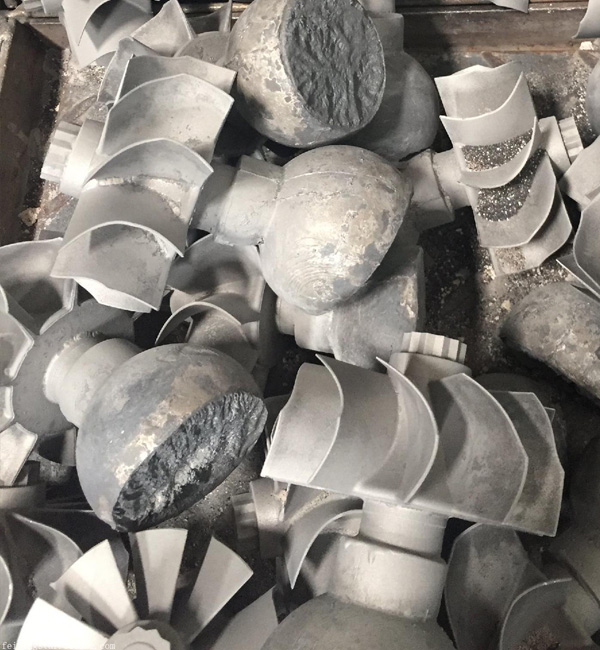
Investment Casting
The biggest advantage of investment casting is that because investment castings have high dimensional accuracy and surface finish, they can reduce machining work, but leave a little machining allowance on the parts with higher requirements. It can be seen that the use of investment casting method can save a lot of machine tool equipment and processing man-hours, and greatly save metal raw materials.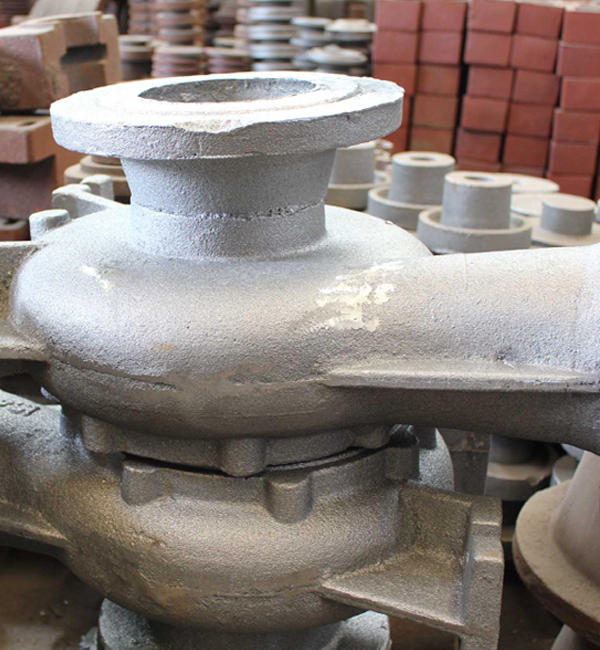
Lost Foam Casting
Lost foam casting is to combine paraffin wax or foam models similar to the casting size and shape into model clusters. After brushing and drying refractory coatings, they are buried in dry quartz sand for vibration modeling, and poured under negative pressure to gasify the model. , The liquid metal occupies the position of the model and forms a new casting method after solidification and cooling.

Die Casting
Die casting is a metal casting process, which is characterized by applying high pressure to the molten metal using the cavity of the mold. Molds are usually made of higher-strength alloys, and this process is somewhat similar to injection molding. Most die castings are iron-free, such as zinc, copper, aluminum, magnesium, lead, tin, and lead-tin alloys and their alloys. Minghe has been China's top die casting service since 1995.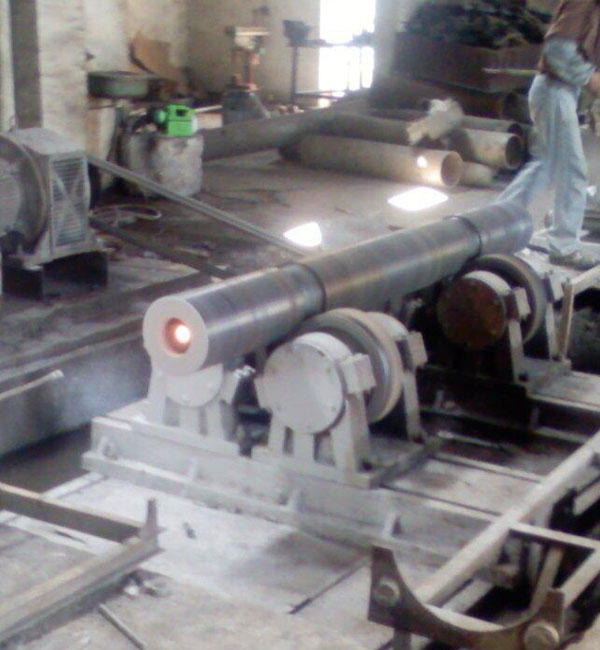
Centrifugal Casting
Centrifugal Casting is a technique and method of injecting liquid metal into a high-speed rotating mold, so that the liquid metal is centrifugal motion to fill the mold and form a casting. Due to the centrifugal movement, the liquid metal can fill the mold well in the radial direction and form the free surface of the casting; it affects the crystallization process of the metal, thereby improving the mechanical and physical properties of the casting.
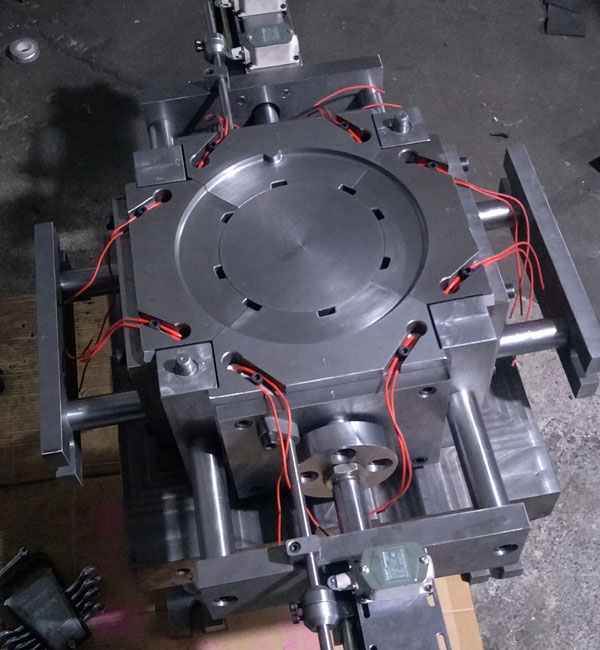
Low Pressure Casting
Low Pressure Casting means that the mold is generally placed above a sealed crucible, and compressed air is introduced into the crucible to cause a low pressure (0.06~0.15MPa) on the surface of the molten metal, so that the molten metal rises from the riser pipe to fill the mold and control Solidified casting method. This casting method has good feeding and dense structure, easy to cast large thin-walled complex castings, no risers, and a metal recovery rate of 95%. No pollution, easy to realize automation.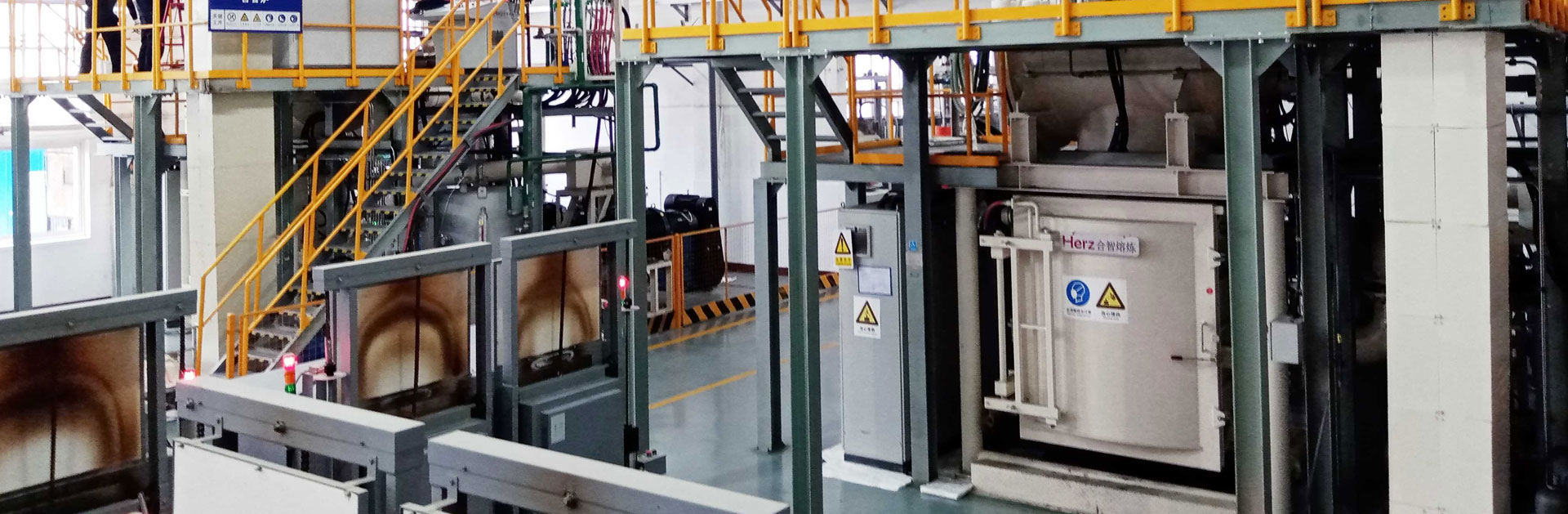