Hot Chamber Die Casting
What Is Hot Chamber Die Casting?
Hot chamber die casting means that the pressure chamber is immersed in the liquid metal in the heat preservation melting crucible, and the injection part is not directly connected to the base, but is installed on the crucible. The advantages of hot chamber die casting are simple production process and high efficiency; low metal consumption and stable process. However, the pressure chamber and the injection punch are immersed in the liquid metal for a long time, which affects the service life. And it is easy to increase the iron content of the alloy.
The injection chamber is communicated with the gate of the die-casting mold through a gooseneck tube. It is suitable for die-casting zinc, lead and other low-melting non-ferrous alloy parts, and can be widely used in industrial sectors such as automobiles, motorcycle parts, instruments, household hardware, and household appliances.
Every die casting component, including the most intricate high-volume production run, benefits from the presence of skillful, knowledgeable casting industry professionals. Our staff of engineers, materials experts, and experienced craftsmen are on call to make sure Minghe's customers have total confidence in their source of supply.Minghe is committed to inspiring complete customer confidence in our ability to supply hot chamber die casting parts to a wide variety of industries, straight from our plant in Donguan, China.
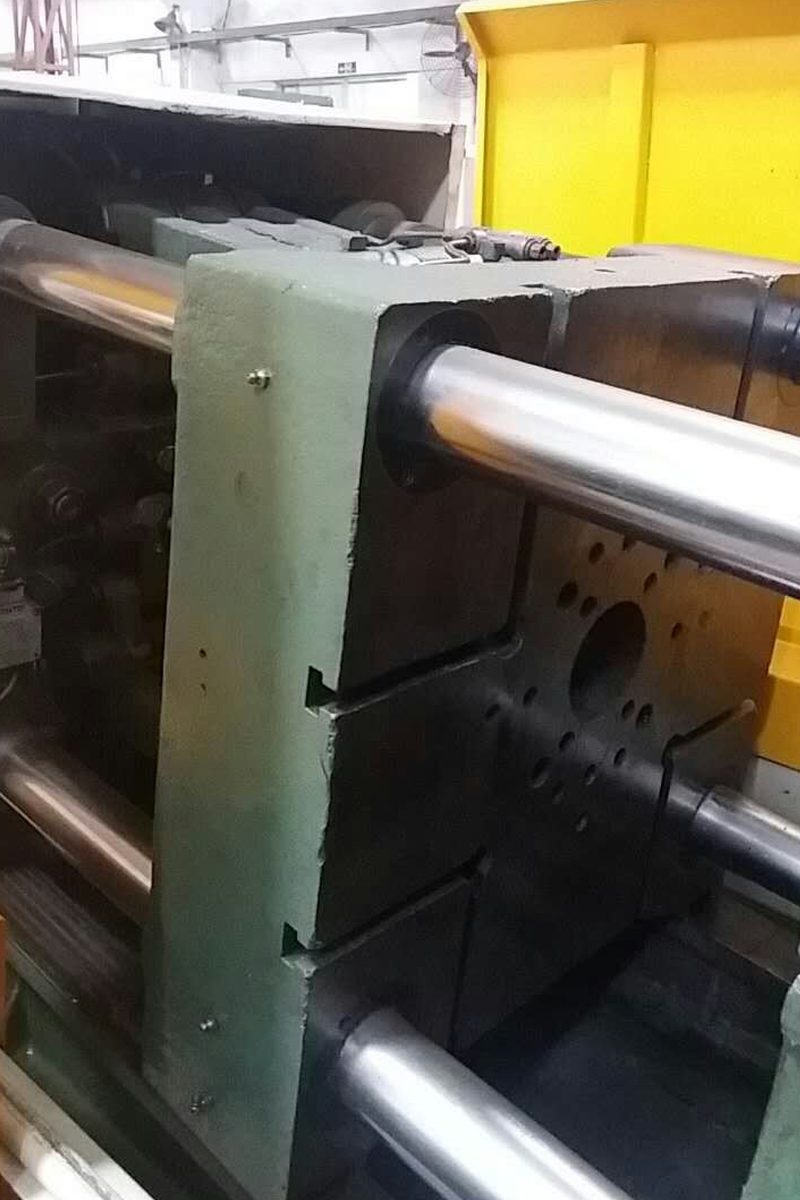
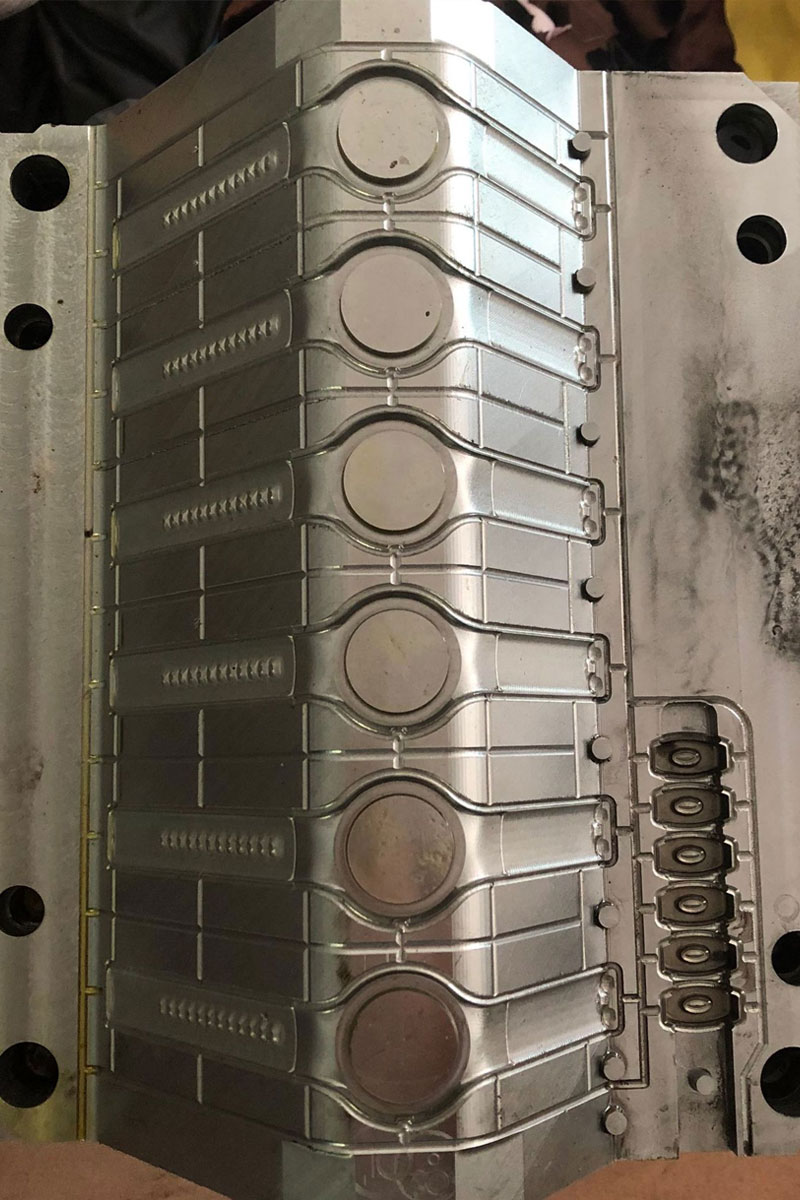
Why Choose Minghe Hot Chamber Die Casting Services?
- Easy for mass production – Since die casting is made from die casting mold, they can be obtained within specified tolerance and shapes. Little or no machining is required and thousands of identical castings can be produced before additional tooling is required. So it’s quiet easy to put on mass production.
- Dimensional accuracy and stability – Die casting produces parts that are durable and dimensionally stable, while maintaining close tolerances. They are also heat resistant.
- Strength and weight – Die cast parts are stronger than plastic injection moldings having the same dimensions. Thin wall castings are stronger and lighter than those possible with other casting methods. Plus, because die castings do not consist of separate parts welded or fastened together, the strength is that of the alloy rather than the joining process.
If you want to choose a china die casting supplier, then Minghe hardware is your best choice.If you have a project that uses low melting point alloys, MINGHE Hardware may be able to help. Depending on the demands of your application, MINGHE Die Casting Company may use cold chamber die casting in place of the hot chamber casting process.
Please contact our die casting experts to help you select the best process to meet the needs of your die casting project, or request a quote on your hot chamber die casting project today.
MINGHE Hardware is your premier source for die casting and machining since 1995.
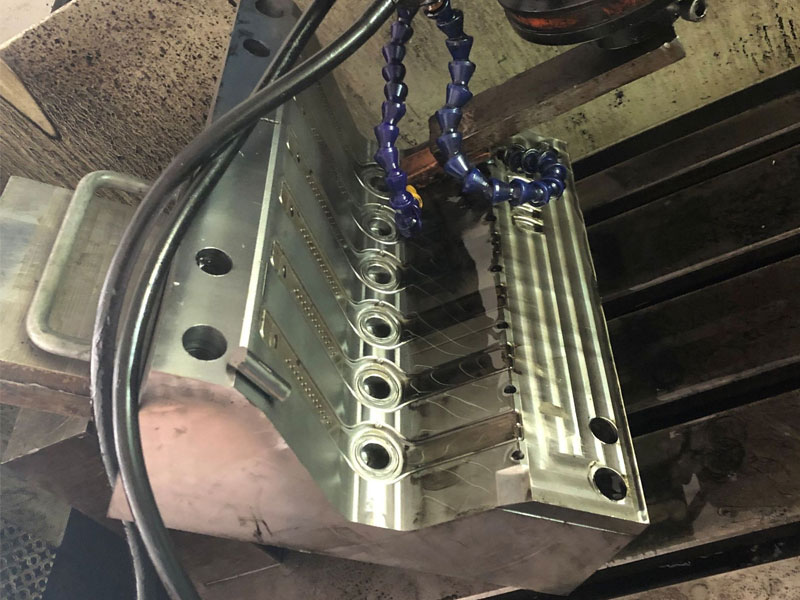
China Die Casting Services Capabilities
Minghe Casting offers and is capable of producing both medium and long-run projects when providing our die casting services. Minghe Casting has supplied the industry's leading die casting services for more than 35 years in a variety of technology for a wide range of applications.
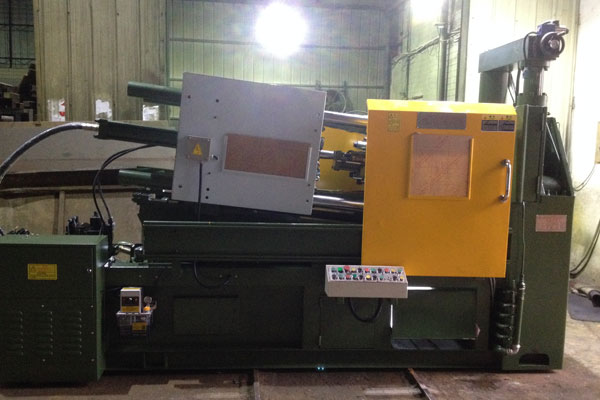
Hot Chamber Die Casting |
Hot Chamber Die Casting for Low Melting Point Alloys.We Can Help with Low Melting Point Alloys |
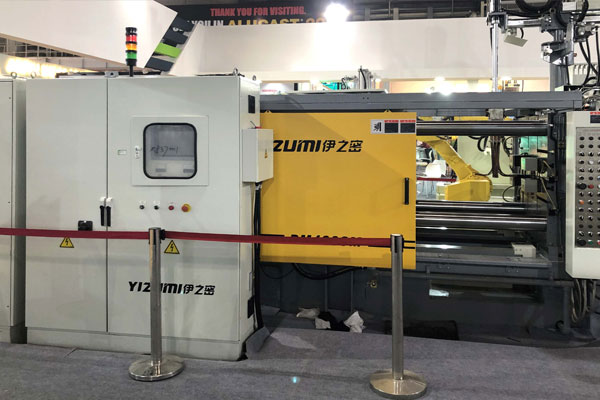
Cold Chamber Die Casting |
Cold Chamber Die Casting for Strong Components and Fast Production |
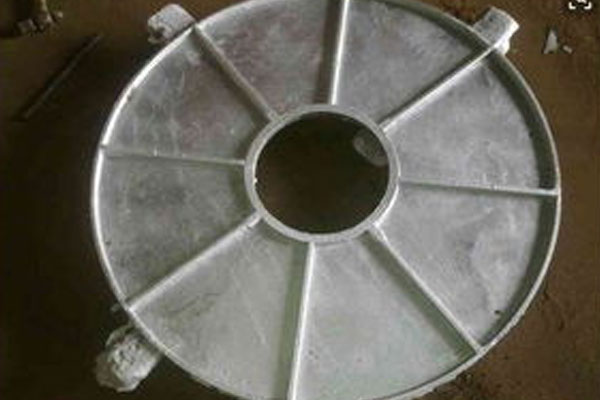
Thin Wall Die Casting |
Ideal Strength-to-Weight Ratio;Thin Wall Die Casting for Lightweight, Complex Aluminum Parts |
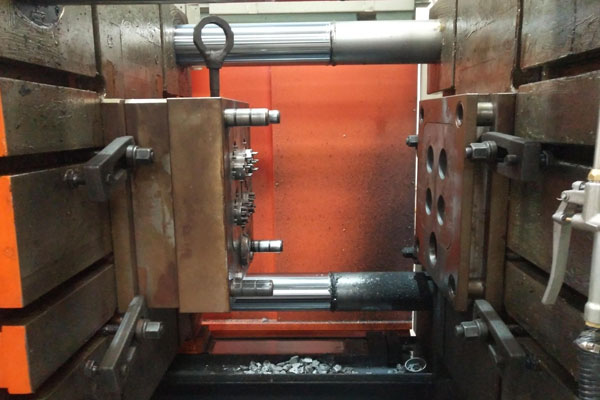
Mold Manufacturing |
Die casting molds from Minghe utilize aluminum and zinc alloys to produce small to large run part identical castings. |
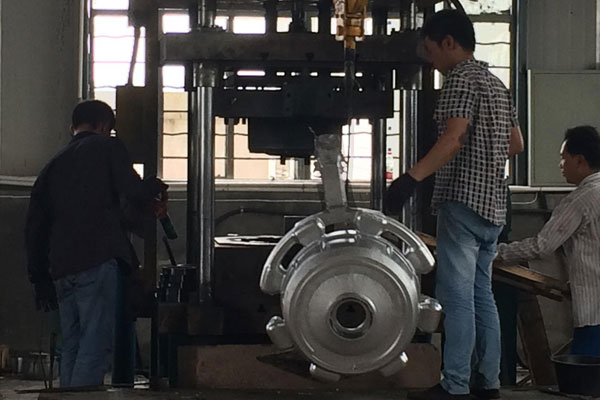
Gravity Casting |
The method has advantages like cost effective, good quality, and process control over other casting techniques. |
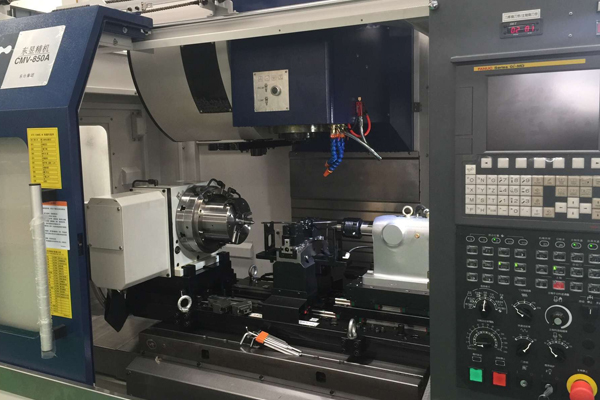
Cnc Machining |
Minghe offers in-house CNC machining as a complement to Minghe die casting services. |
China Minghe Die Casting Materials
Minghe Die Casting services working with Aluminum、Zinc and Other.
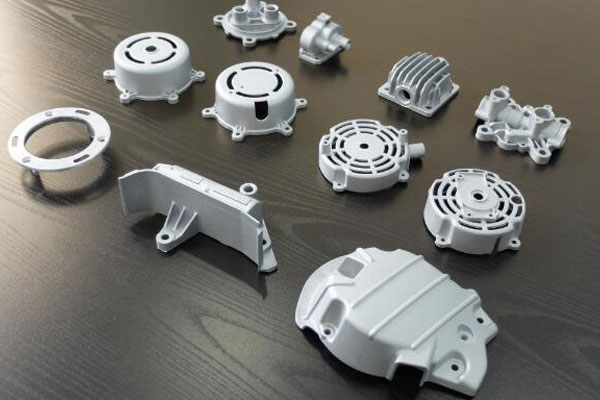
Aluminum Die Casting
- A360
- A380
- ADC6
- ADC10
- ADC12
- ALSi12
- ALSi9Cu3
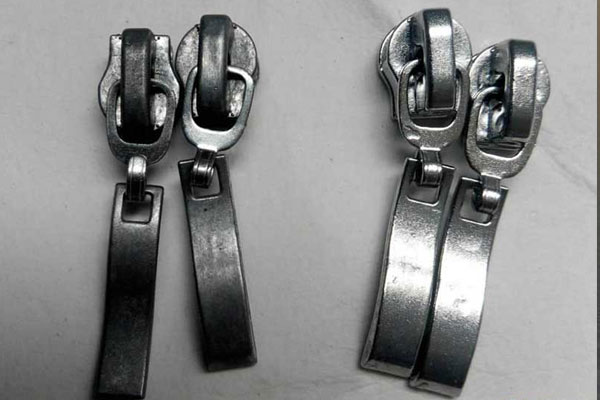
Zinc Die Casting
- Zamak3
- Zamak5
- Zamak8
- Zamak12
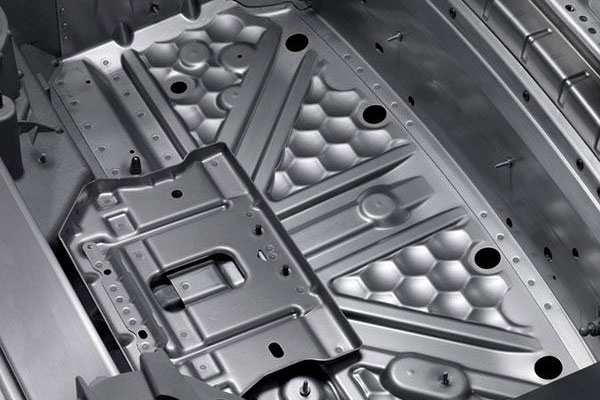
Magnesium Die Casting
- AM50A
- AM60B
- AZ91D
- AZ63A
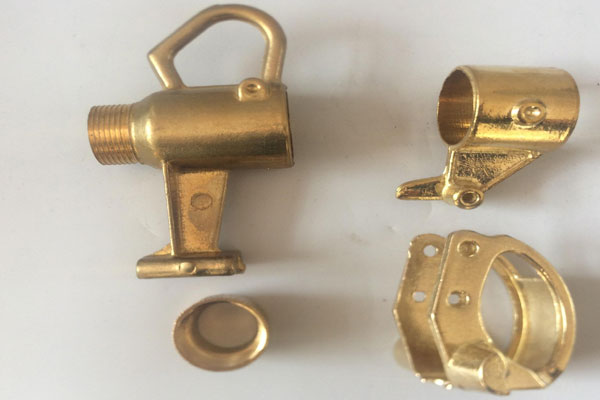
Other Casting Material
- Titanium
- Copper
- Bronze
- Steel
- Stainless Steel
- Foundry Iron
Applications of MINGHE Die Casting Services
Die Casting parts are all around you, they may be important components of your car and also can perform vital functions in your electrical equipment. Minghe is an accomplished casting supplier that engaged in a broad range of die casting applications.
Our manufacturing parts are suitable for following industries:
![]() |
AUTOMOTIVE INDUSTRY |
![]() |
MOTORCYCLE INDUSTRY |
![]() |
MACHINERY INDUSTRY |
![]() |
LED LIGHTING INDUSTRY |
![]() |
HEATSINK INDUSTRY |
![]() |
KITCHENWARE INDUSTRY |
![]() |
PUMP VALVE INDUSTRY |
![]() |
MEDICAL DEVICE INDUSTRY |
![]() |
TELECOM INDUSTRY |
![]() |
BICYCLE INDUSTRY |
![]() |
AEROSPACE INDUSTRY |
![]() |
ELECTRONIC INDUSTRY |
![]() |
DISPLAY CABINT INDUSTRY |
![]() |
ROBOTS INDUSTRY |
![]() |
MORE INDUSTRY |
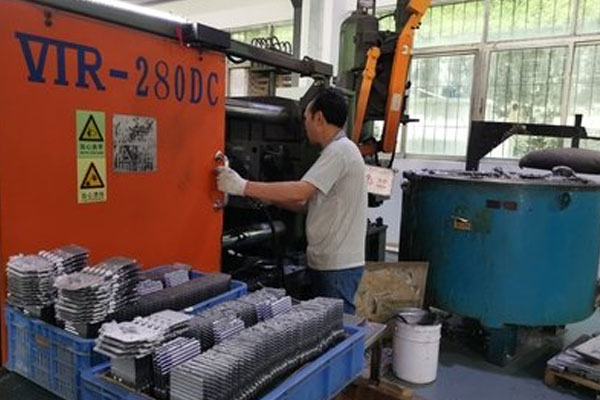
The Advantages of Minghe Hot Chamber Die Cast
- The complex shapes of parts can be obtained and the performance of parts can be improved. Besides, assembly work is reduced.
- Durable and dimensionally stable die casting parts can be obtained with specified shapes, so no machining or less machining is required.
- Die casting parts can have many finishing techniques and surfaces. The process is capable of achieving smooth or textured part surfaces.
- Net shape part configuration is achievable.
- Intricate cast-in detail
- Reduced porosity
- Longer die casting die life due to lower melting points
- Die design efficiencies = waste reduction
- Fast cycle times(approximately 15 cycles a minute)
- The convenience of melting the metal in the casting maching
The Minghe Case Studies Of Hot Chamber Die Casting
You have a complex part design, Minghe Casting Company can help you turn it into a reality. With the right equipment, strong technical knowledge, and a focus on quality.. From tool design to finishing and then on to shipment, Minghe Casting ensure that every project is completed to a high standard and that your orders are delivered on time, every time.
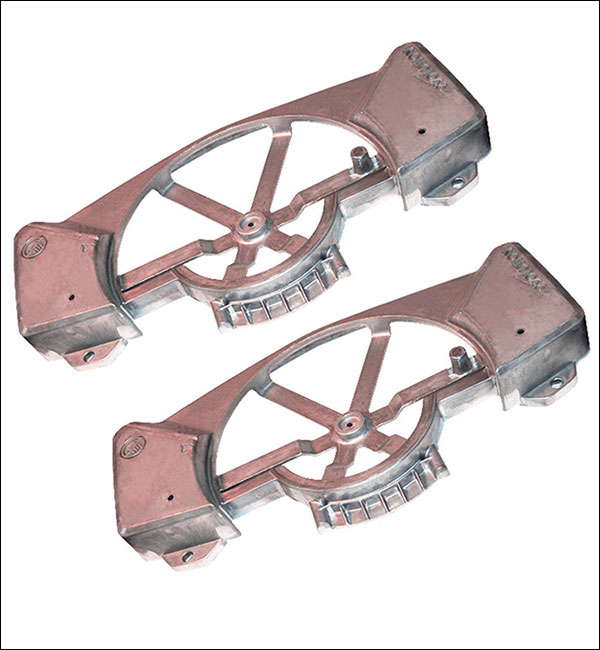
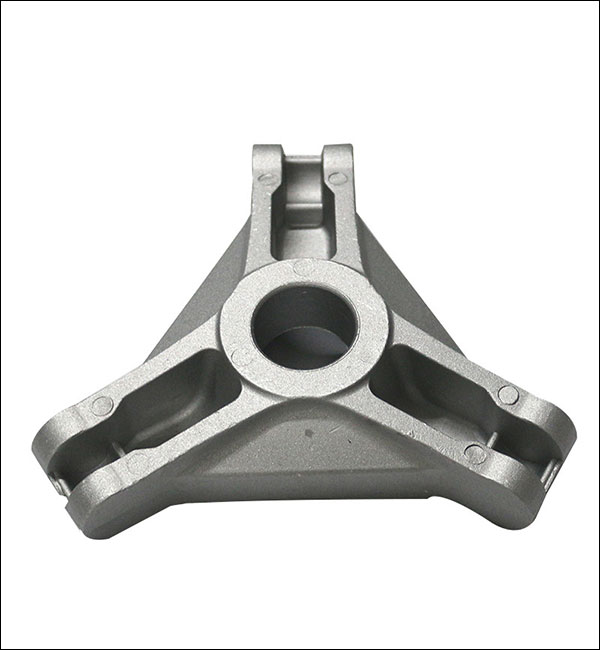
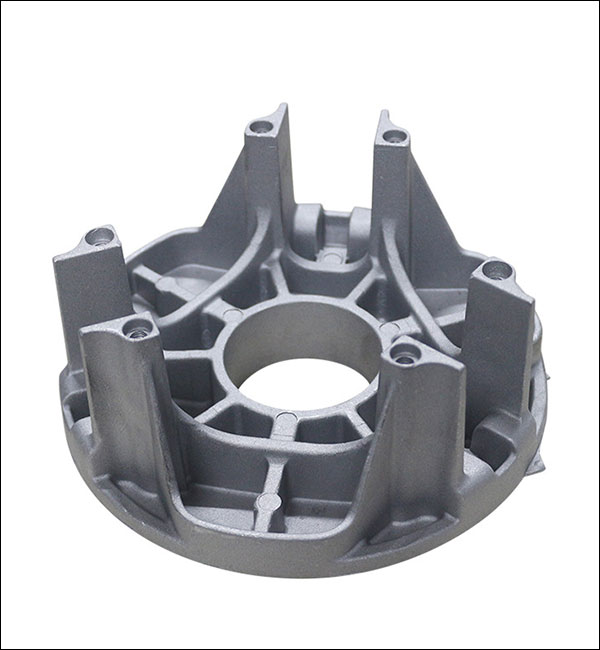
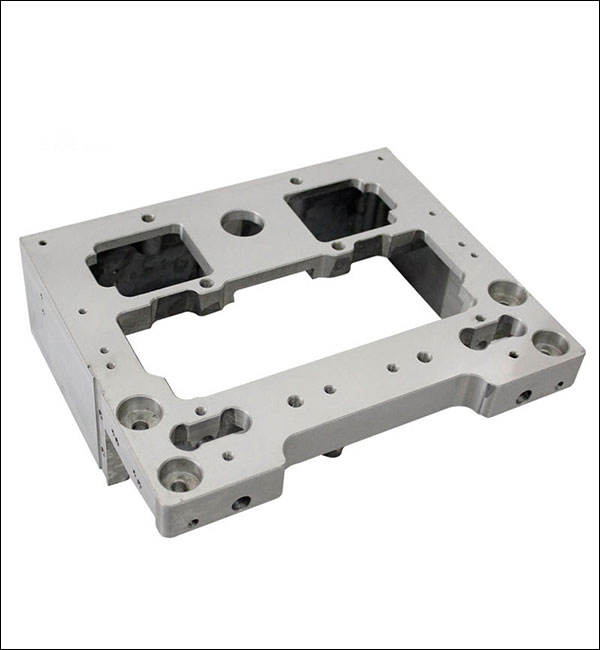
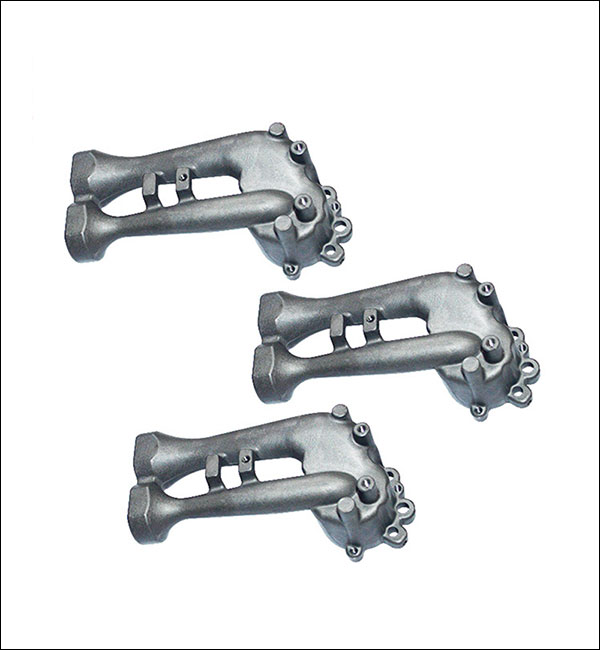
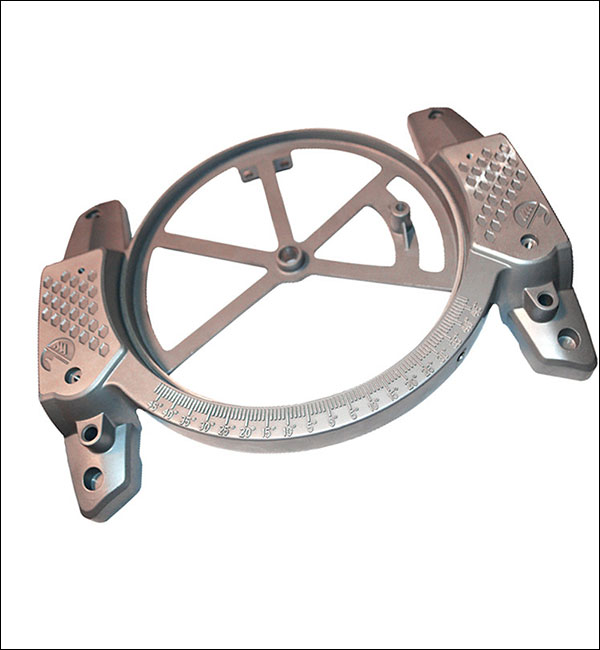
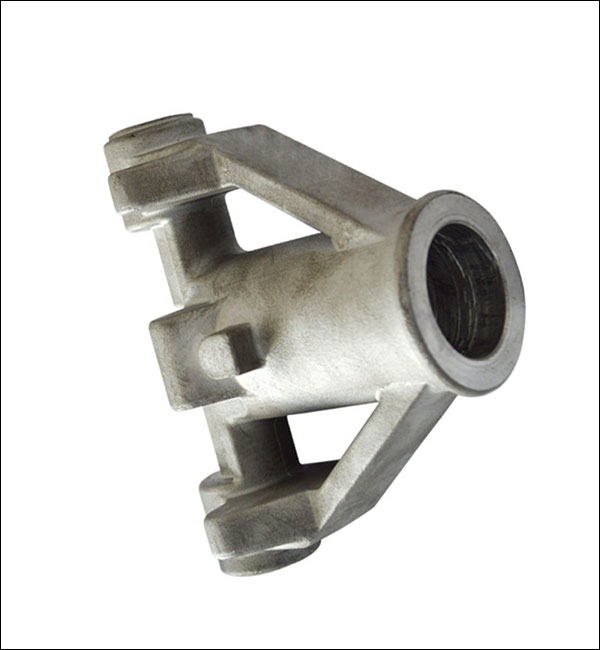
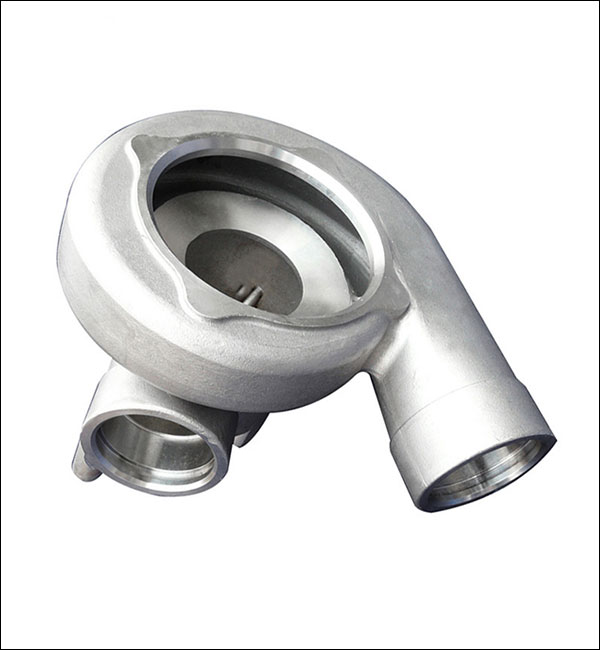
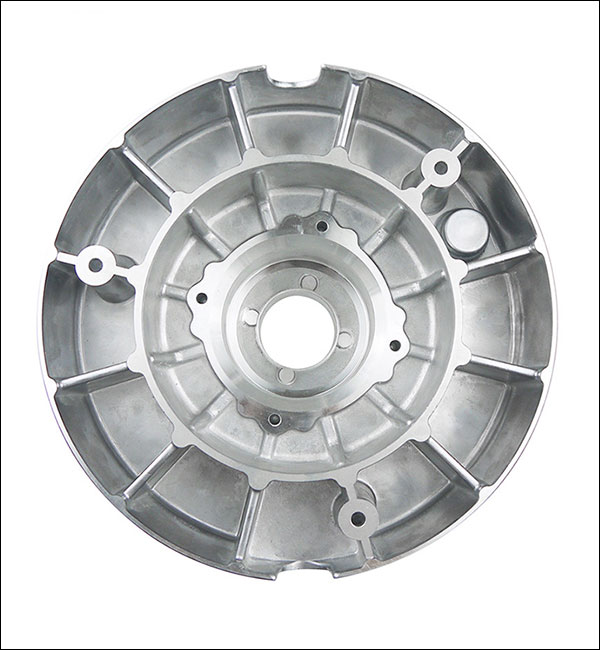
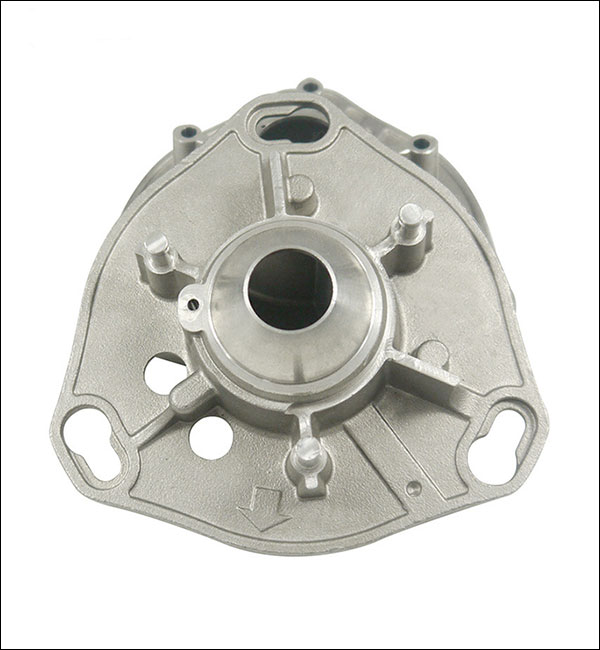
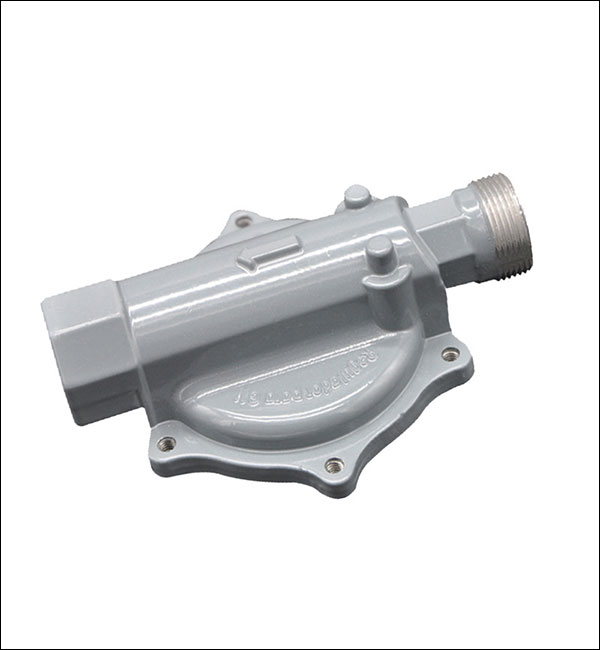
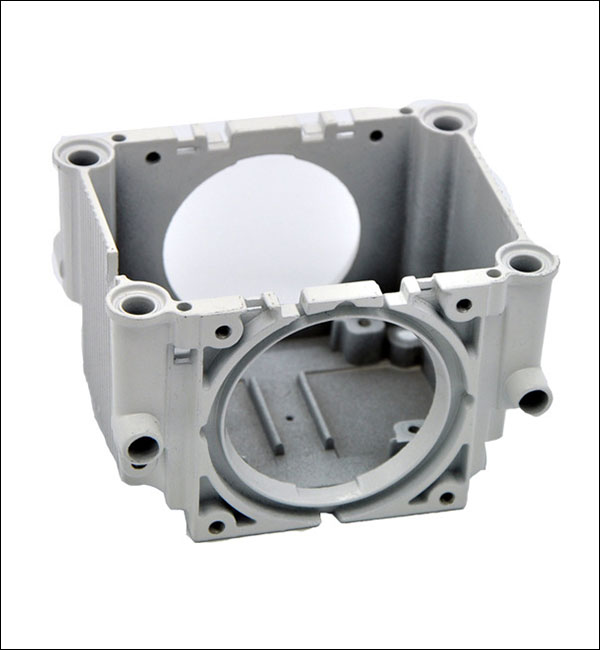
Go To View More Casting Parts Cases Studies >>>
Choose the Best Hot Chamber Die Casting Service
Currently, our hot chamber die casting parts are exported to America, Canada, Australia, United Kingdom, Germany, France, Sout Africa, and many other countries all over the world. We are ISO9001-2015 registered and also certified by SGS.
Custom china die casting service provides durable and affordable castings that meet your specifications for automotive, medical, aerospace, electronics, food, construction, security, marine, and more industries. Fast to send your inquiry or submit your drawings to get a free quote in the shortest time.Contact us or Email sales@hmminghe.com to see how our people, equipment and tooling can bring the best quality for the best price for your hot chamber die casting project.
We Provide Casting Services Include:
Minghe Casting services working with sand casting、metal casting 、investment casting lost foam casting, and more.

Sand Casting
Sand Casting is a traditional casting process that uses sand as the main modeling material to make molds. Gravity casting is generally used for sand molds, and low-pressure casting, centrifugal casting and other processes can also be used when there are special requirements. Sand casting has a wide range of adaptability, small pieces, large pieces, simple pieces, complex pieces, single pieces, and large quantities can be used.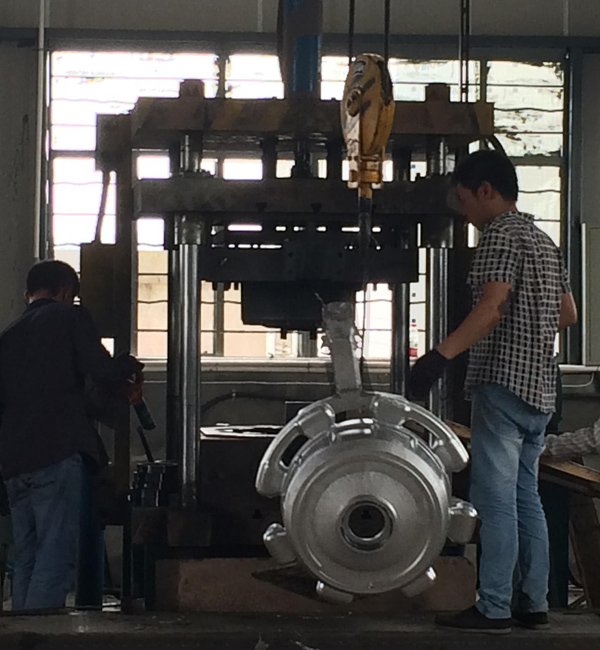
Permanent Mold Casting
Permanent Mold Casting have a long life and high production efficiency, not only have good dimensional accuracy and smooth surface, but also have higher strength than sand castings and are less likely to be damaged when the same molten metal is poured. Therefore, in the mass production of medium and small non-ferrous metal castings, as long as the melting point of the casting material is not too high, metal casting is generally preferred.
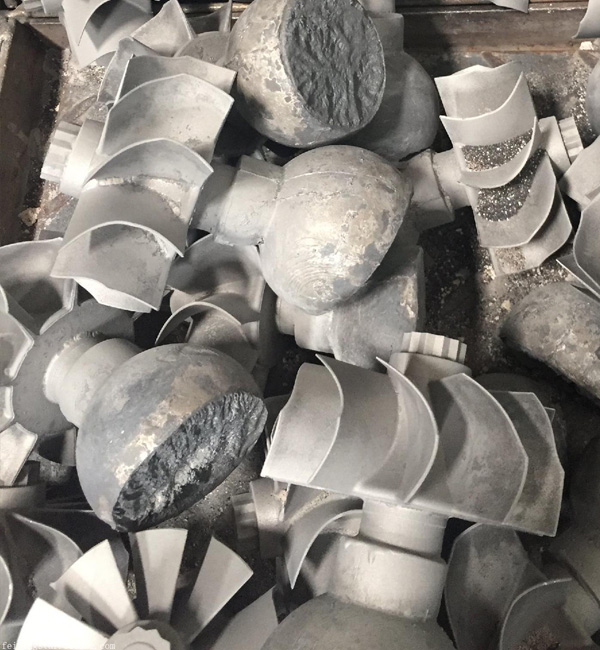
Investment Casting
The biggest advantage of investment casting is that because investment castings have high dimensional accuracy and surface finish, they can reduce machining work, but leave a little machining allowance on the parts with higher requirements. It can be seen that the use of investment casting method can save a lot of machine tool equipment and processing man-hours, and greatly save metal raw materials.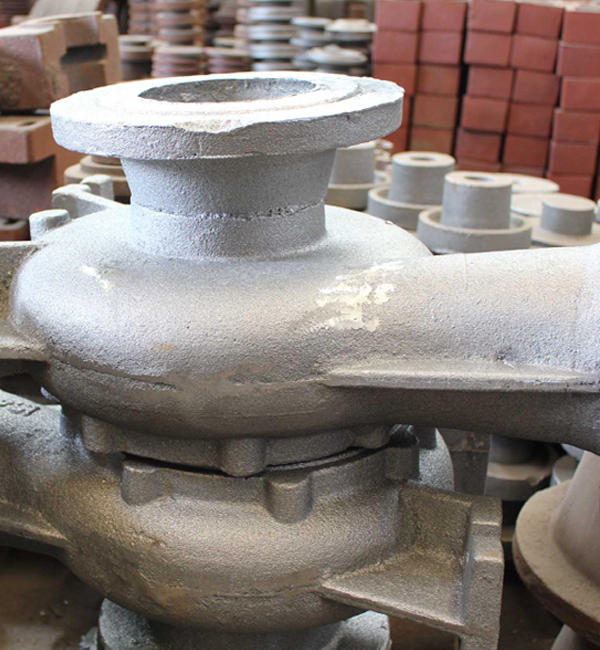
Lost Foam Casting
Lost foam casting is to combine paraffin wax or foam models similar to the casting size and shape into model clusters. After brushing and drying refractory coatings, they are buried in dry quartz sand for vibration modeling, and poured under negative pressure to gasify the model. , The liquid metal occupies the position of the model and forms a new casting method after solidification and cooling.

Die Casting
Die casting is a metal casting process, which is characterized by applying high pressure to the molten metal using the cavity of the mold. Molds are usually made of higher-strength alloys, and this process is somewhat similar to injection molding. Most die castings are iron-free, such as zinc, copper, aluminum, magnesium, lead, tin, and lead-tin alloys and their alloys. Minghe has been China's top die casting service since 1995.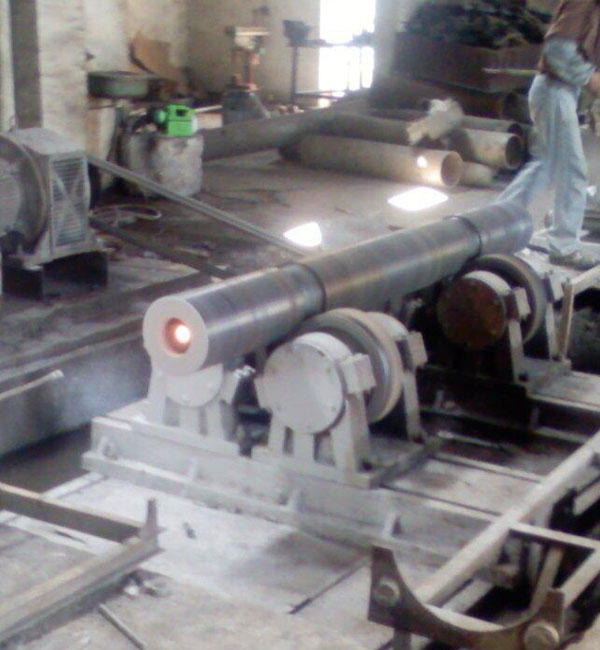
Centrifugal Casting
Centrifugal Casting is a technique and method of injecting liquid metal into a high-speed rotating mold, so that the liquid metal is centrifugal motion to fill the mold and form a casting. Due to the centrifugal movement, the liquid metal can fill the mold well in the radial direction and form the free surface of the casting; it affects the crystallization process of the metal, thereby improving the mechanical and physical properties of the casting.
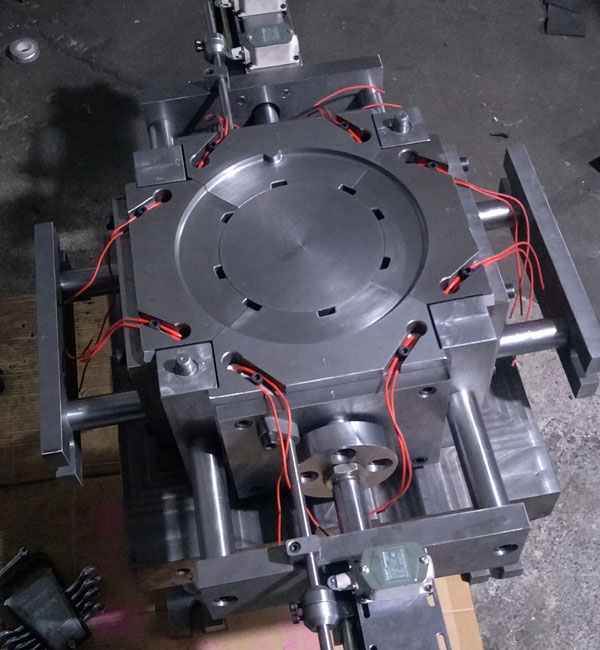
Low Pressure Casting
Low Pressure Casting means that the mold is generally placed above a sealed crucible, and compressed air is introduced into the crucible to cause a low pressure (0.06~0.15MPa) on the surface of the molten metal, so that the molten metal rises from the riser pipe to fill the mold and control Solidified casting method. This casting method has good feeding and dense structure, easy to cast large thin-walled complex castings, no risers, and a metal recovery rate of 95%. No pollution, easy to realize automation.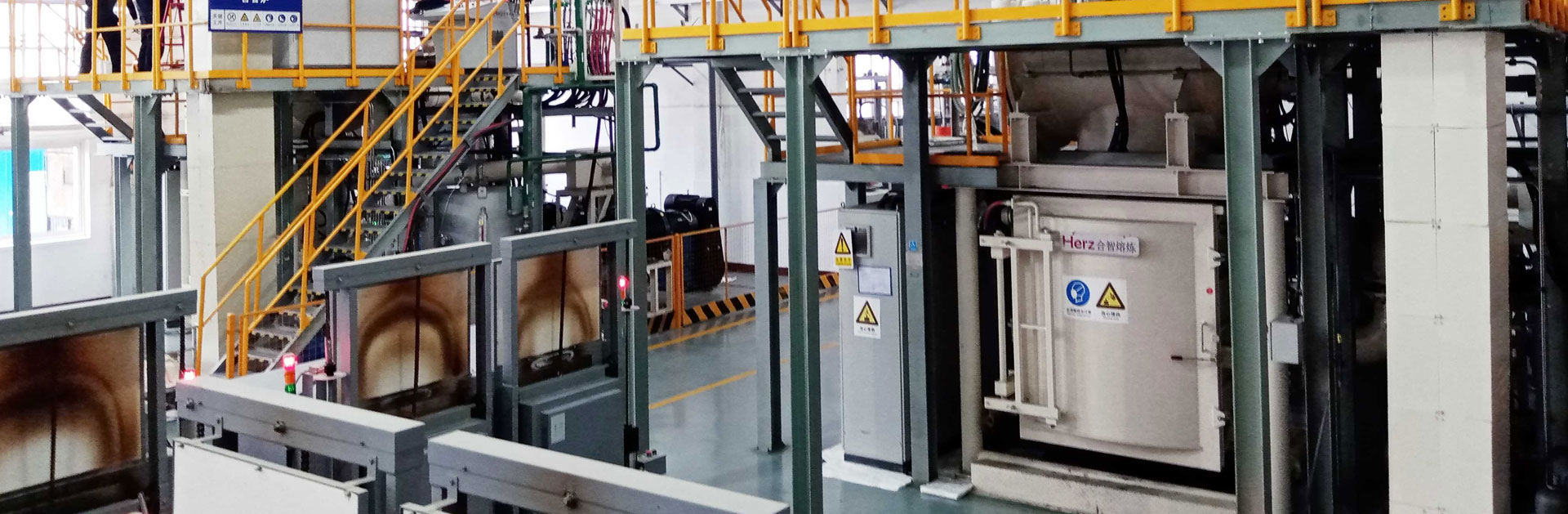