Sand Casting
What Is Sand Casting
Sand casting refers to a casting method in which castings are produced in sand molds. Steel, iron and most non-ferrous alloy castings can be obtained by sand casting methods. Because the modeling materials used in sand casting are cheap and easy to obtain, and the molds are easy to manufacture, they can adapt to single-piece production, batch production and mass production of castings. For a long time, it has been the basic process in casting production.
The basic raw materials for making sand molds are foundry sand and sand binder. The most commonly used foundry sand is siliceous sand. When the high-temperature performance of silica sand cannot meet the requirements of use, special sand such as zircon sand, chromite sand, and corundum sand are used. In order to make the finished sand mold and core have a certain strength and not be deformed or damaged during handling, molding and pouring of liquid metal, it is generally necessary to add a sand binder in the casting to bond the loose sand particles to form sand. The most widely used molding sand binder is clay, and various drying oils or semi-drying oils, water-soluble silicates or phosphates and various synthetic resins can also be used as molding sand binders. The outer sand molds used in sand casting are divided into three types: clay green sand, clay dry sand and chemical hardened sand according to the binder used in the sand and the way it builds its strength.
Clay Wet Sand
Clay and an appropriate amount of water are used as the main binder for molding sand. After the sand is made, it is directly combined and poured in a wet state. Wet casting has a long history and is widely used. The strength of green sand depends on the clay slurry formed by mixing clay and water in a certain proportion. Once the molding sand is mixed, it has a certain strength. After being pounded into a sand mold, it can meet the requirements of molding and pouring. Therefore, the amount of clay and moisture in the molding sand are very important process factors.
A casting method in which molding sand and core sand are used as molding materials to make a mold, and liquid metal is filled with the mold under gravity to produce a casting. Steel, iron and most non-ferrous alloy castings can be obtained by sand casting methods. Because the molding materials used in sand casting are cheap and easy to obtain, and the molds are easy to manufacture, they can adapt to single-piece production, batch production and mass production of castings. For a long time, it has been the basic process in casting production.
The mold used in sand casting is generally composed of a combination of an outer sand mold and a core. In order to improve the surface quality of castings, a layer of paint is often applied to the surface of the sand mold and core. The main components of the coating are powdery materials and binders with high refractoriness and good chemical stability at high temperatures. In addition, a carrier (water or other solvents) and various additives are added for easy application.
The advantages of clay green sand casting are:
- - Clay is rich in resources and low in price.
- - Most of the used clay wet sand can be recycled and reused after proper sand treatment.
- - The cycle of manufacturing the mold is short and the work efficiency is high.
- - The mixed molding sand can be used for a long time.
- - After the sand mold is pounded, it can still tolerate a small amount of deformation without being damaged, which is very beneficial for drafting and core setting.
Weakness is:
- - To coat the viscous clay slurry on the surface of the sand grains during sand mixing, high-power sand mixing equipment with kneading action is required, otherwise it is impossible to obtain good quality sand.
- - Since the molding sand has very high strength after being mixed, the molding sand is not easy to flow during modeling and it is difficult to pound. It is laborious and requires certain skills when modeling by hand, and the equipment is complicated and huge when modeling by machine.
- - The rigidity of the mold is not high, and the dimensional accuracy of the casting is poor.
- - Castings are prone to defects such as sand washing, sand inclusion and pores.
Clay dry sand molds have a slightly higher wet moisture content than those used in the production of this sand mold.
Clay sand core is a simple core made of clay sand.
Dry Clay Sand
The wet moisture of the molding sand used to make this sand mold is slightly higher than that of the wet molding sand. After the sand mold is made, the surface of the cavity should be coated with refractory paint, and then placed in an oven for drying, and after it has cooled down, it can be molded and poured. It takes a long time to dry clay sand molds, consumes a lot of fuel, and the sand molds are easily deformed during the drying process, which affects the accuracy of castings. Clay dry sand molds are generally used to make steel castings and larger iron castings. Since chemically hardened sand has been widely adopted, dry sand types have tended to be eliminated.
Chemically Hardened Sand
The molding sand used in this type of sand is called chemically hardened sand. The binder is generally a substance that can polymerize molecules and become a three-dimensional structure under the action of a hardener, and various synthetic resins and water glass are commonly used. There are basically 3 ways of chemical hardening.
- - Self-Hardening: The binder and hardener are both added during sand mixing. After the sand mold or core is made, the binder reacts under the action of the hardener to cause the sand mold or core to harden by itself. The self-hardening method is mainly used for modeling, but it is also used to manufacture larger cores or cores with small production batches.
- - Aerosol Hardening: Add binder and other auxiliary additives when mixing sand, without adding hardener first. After modeling or core making, blow in gaseous hardener or liquid hardener atomized in the gas carrier to disperse it in the sand mold or core to cause the sand mold to harden. The aerosol hardening method is mainly used to make cores, and is sometimes used to make small sand molds.
- - Heating Hardening: Add binder and latent hardening agent that does not work at room temperature when mixing sand. After the sand mold or core is made, it is heated. At this time, the latent hardener reacts with certain components in the binder to generate an effective hardener that can harden the binder, thereby hardening the sand mold or core. The heating hardening method is mainly used to make cores in addition to the manufacture of small thin-shell sand molds.
The History Of Minghe Sand Casting Workshop
Minghe Sand casting workshop was added in 2005 with the addition of a coastal sand mixer continuous sand mixer. Sand casting is a great compliment to the Rubber Plaster Mold, process the company was founded on. Sand casting currently makes up about half of our foundry business.
In 2016, Minghe Casting greatly expanded the sand casting line with the addition of a larger continuous sand mixer with dual hopper, automated controls, and mechanical reclaim. This allows Minghe Casting to move from just low quantity high quality to production quantities, while still maintaining the high quality demanded by the market place. The investment also represents the commitment of Prototype Casting to minimize its footprint for consuming natural resources, specifically the silica sand used in sand casting. Because of secondary markets for reclaimed sand, and the ability to reuse 80% of the sand in the process, the waste of sand to landfills will be completely eliminated!!!
Minghe sand casting workshop is about 8000 square meters. Whatever your casting project is small or big, we can give you good lead time and good quality. In our foundry, more than 60% Cast Aluminum parts are exported. So we have much experience for your projects.
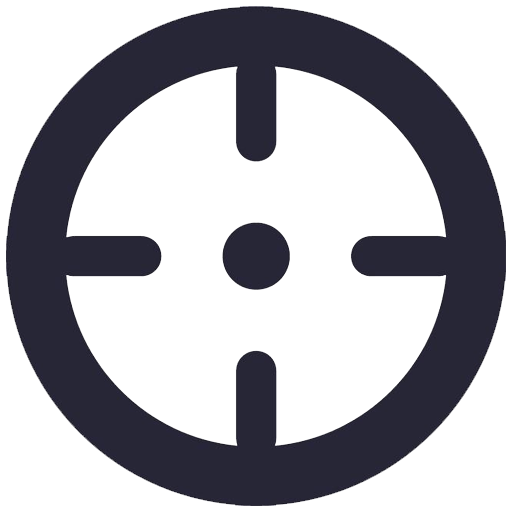
Benefits of Sand Casting Process
The functions of investment casting can be summarized as follows:
- – The wear-resistant parts of sand casting crushers are still very common in China, such as jaw plates, high chromium hammers, crushing walls, rolling mortar walls, etc., because in the crusher equipment, as a relatively large wear-resistant casting, Relatively speaking, the accuracy is not very high. Especially for the jaws, the finished products are almost not polished by a lathe. The broken wall, rolling mortar wall, roll skin and the like only need to be polished by a lathe, so it is especially suitable for sand casting. Because the wear-resistant parts of sand casting jaws, high chromium hammers, broken walls, rolling mortar walls, roll skins, etc., these crushing equipment are more than 20% more durable than other products such as lost foam casting.
- – Sand casting is a kind of casting process. The casting mold used in sand casting is generally composed of an outer sand mold and a core. Because the molding materials used in sand casting are cheap and easy to obtain, and the molds are easy to manufacture, they can adapt to single-piece production, batch production and mass production of castings. For a long time, it has been the basic process in casting production. At present, internationally, in the production of all castings, 60 to 70% of the castings are produced with sand molds, and about 70% of them are produced with clay sand molds.
- – low cost
- – Simple production process
- – Short production cycle
- – Therefore, castings such as automobile engine cylinder blocks, cylinder heads, crankshafts, etc. are all produced by the clay green sand process. When the wet type cannot meet the requirements, consider using the clay sand surface dry sand type, dry sand type or other sand types. The weight of castings made from clay green sand can range from a few kilograms to dozens of kilograms, while castings produced by dry clay can weigh dozens of tons.
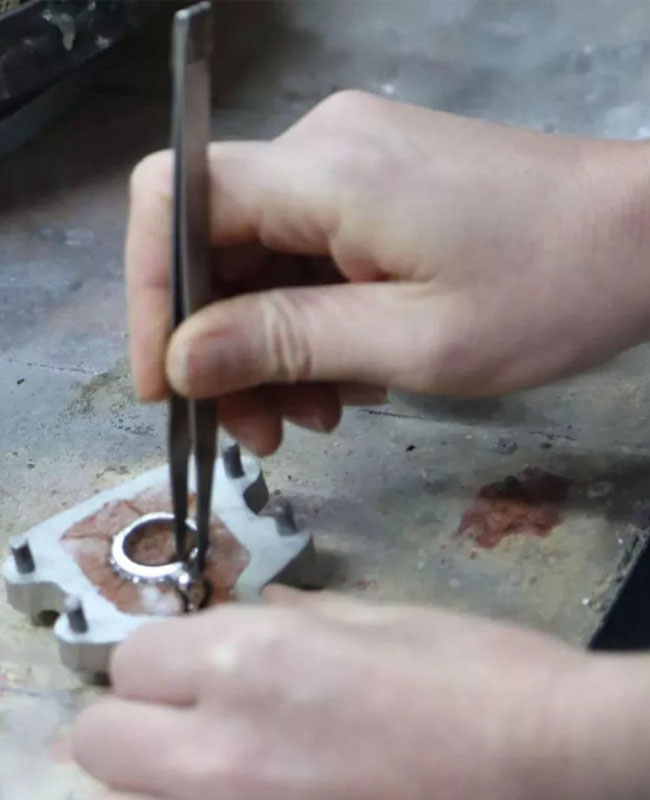
Minghe Hardware Production Process Of Sand Casting
The basic process of Minghe Casting sand casting process has the following steps:
- Sand Mixing Stage: Preparing molding sand and core sand for modeling, generally use a sand mixer to put in the old map and appropriate amount of clay to mix.
- Mold Making Stage: Make molds and core boxes according to the drawings of the parts. Generally, a single piece can be made of wood molds, mass production can be used to make plastic molds or metal molds (commonly known as iron molds or steel molds), and large-scale castings can be used to make pattern plates. Now the molds are basically engraving machines, so the production cycle is greatly shortened, and it usually takes 2 to 10 days to make the mold.
- Modeling (Core-Making) Stage: including modeling (forming the cavity of the casting with molding sand), core-making (forming the inner shape of the casting), and mold matching (putting the core into the cavity, and closing the upper and lower flasks) ). Modeling is a key link in casting.
- Melting Stage: According to the required metal composition, the chemical composition is matched, and the appropriate melting furnace is selected to melt the alloy material to form a qualified liquid metal liquid (including qualified composition and qualified temperature). Smelting generally uses cupola or electric furnace (due to environmental protection requirements, cupolas are now basically banned, and electric furnaces are basically used).
- Pouring Stage: Use a ladle to pour the molten iron in the electric furnace into the finished mold. It is necessary to pay attention to the speed of pouring molten iron, so that the molten iron fills the entire cavity. In addition, pouring molten iron is more dangerous, so pay attention to safety!
- Cleaning Stage: After pouring and waiting for the molten metal to solidify, take a hammer to remove the gate and shake off the sand of the casting, and then use a sandblasting machine for sandblasting, so that the surface of the casting will look very clean! For castings that are not strictly required After inspection, it is basically ready to leave the factory.
- Casting Processing: For some castings with special requirements or some castings that cannot meet the requirements, simple processing may be required. Generally, a grinding wheel or a grinder is used for processing and polishing to remove the burrs and make the castings smoother.
- Casting Inspection: Casting inspection is usually in the process of cleaning or processing, and the unqualified ones are usually found out. However, some castings have individual requirements and need to be inspected again. For example, some castings require a 5 cm shaft to be inserted into the center hole, so you need to take a 5 cm shaft and try it out.
After the above 8 steps, the casting is basically formed. For castings that require high precision, machining is required.
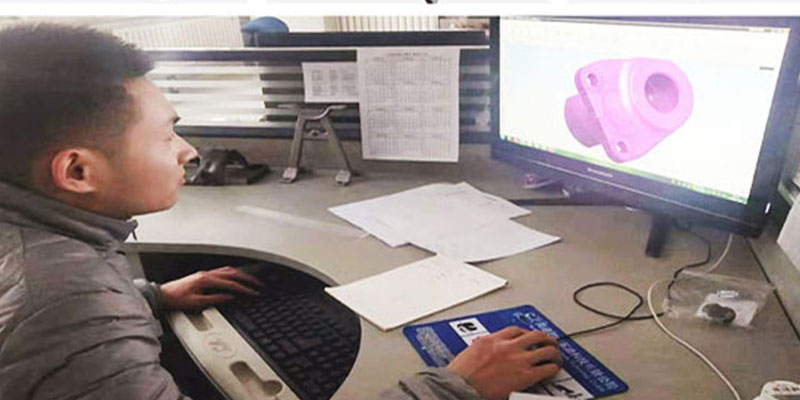
Mold Development And Design ▶ |
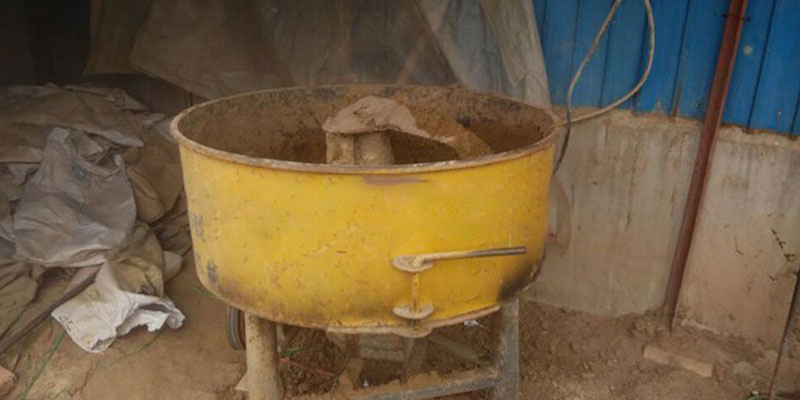
Sand Mxing Stage ▶ |
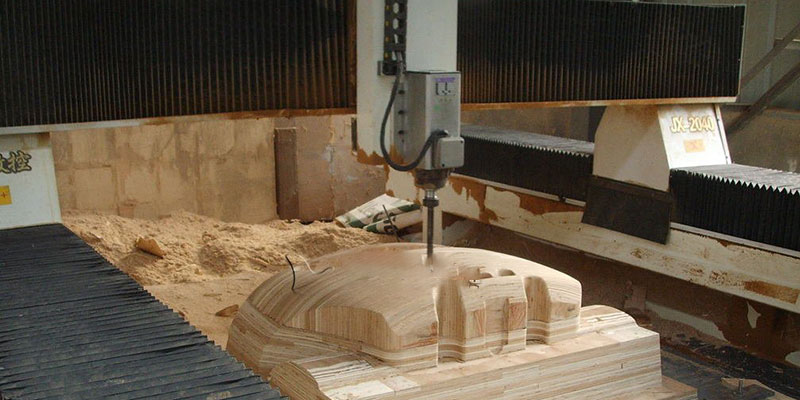
Lost Wax Inspection ▶ |
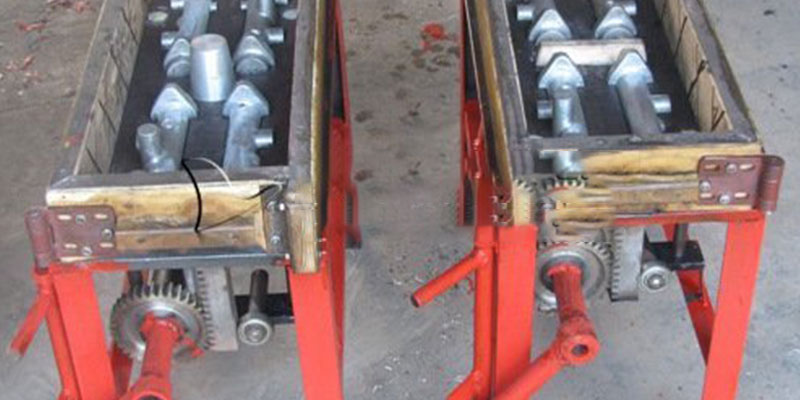
Wax Group Tree▶ |
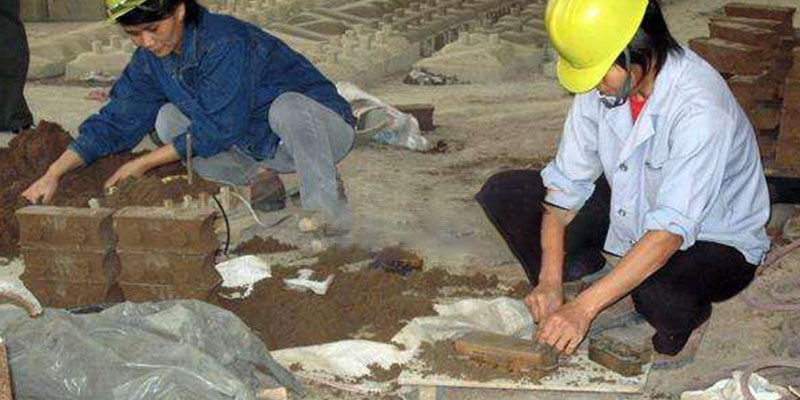
Silica Sol Shell ▶ |
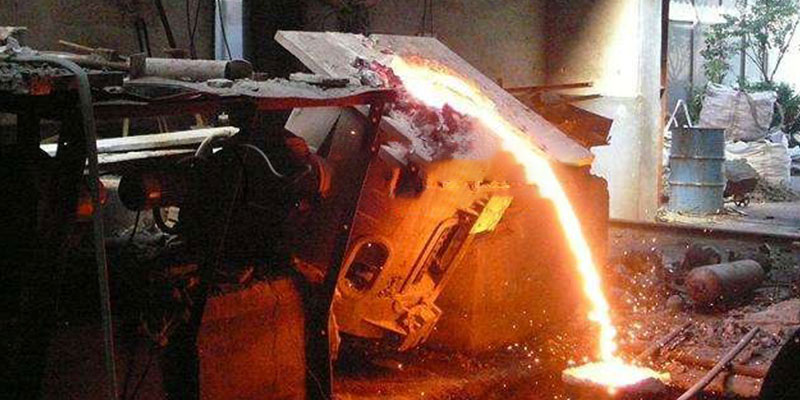
Water Glass Reinforcement▶ |
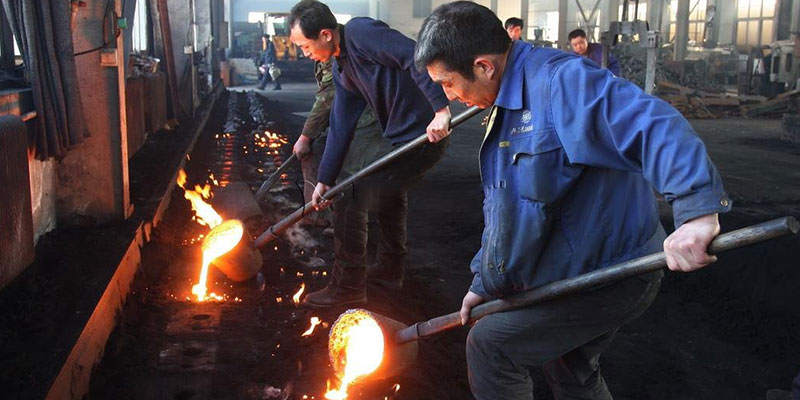
Steam Dewaxing ▶ |
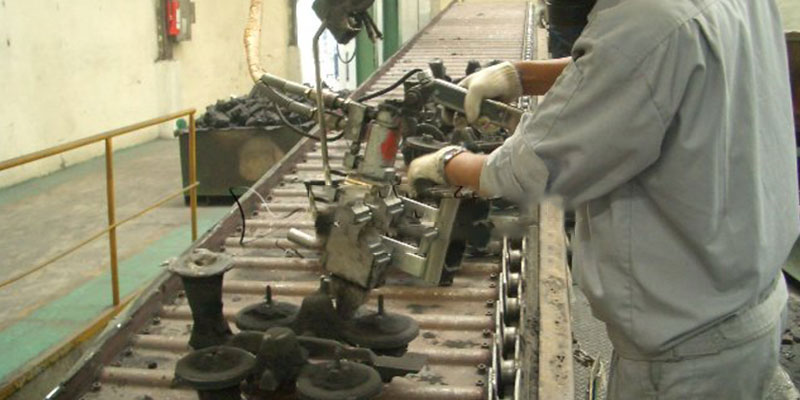
Roasting-Pouring▶ |
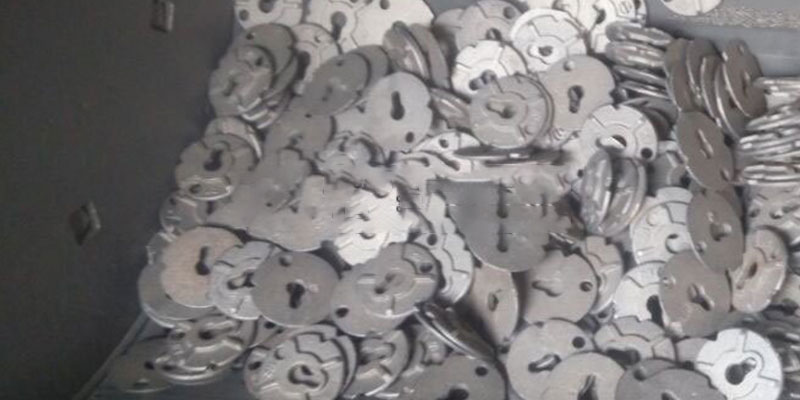
Remove Gate Sanding ▶ |
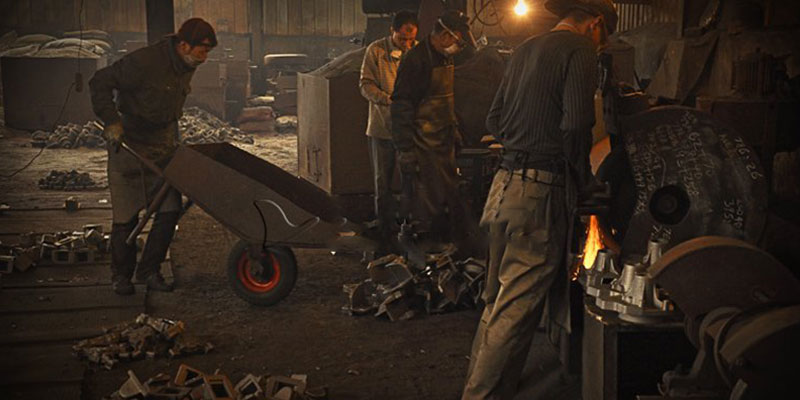
Blank Positive▶ |
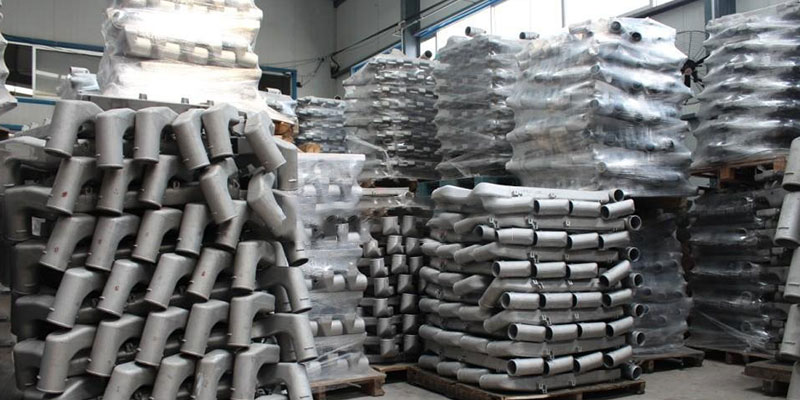
Complete Precision Castings▶ |
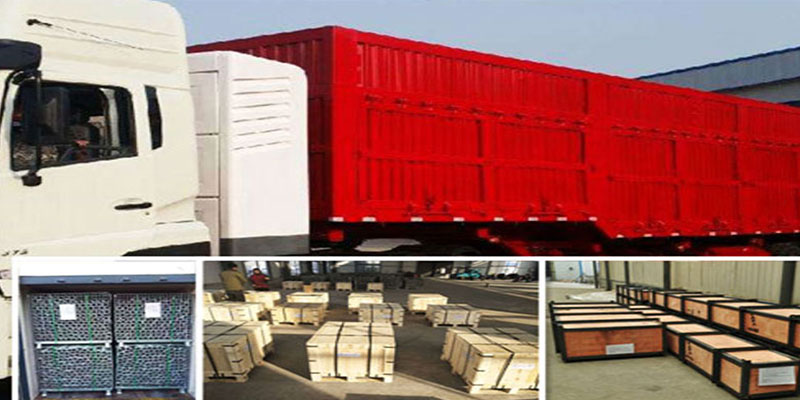
Pack And Ship▶ |
The Minghe Case Studies Of Sand Casting
Minghe Casting fabrication services are available for both design to reality and low to high volume production runs of your die casting parts,sand casting parts,investment casting parts,metal casting parts, lost foam casting parts and more.
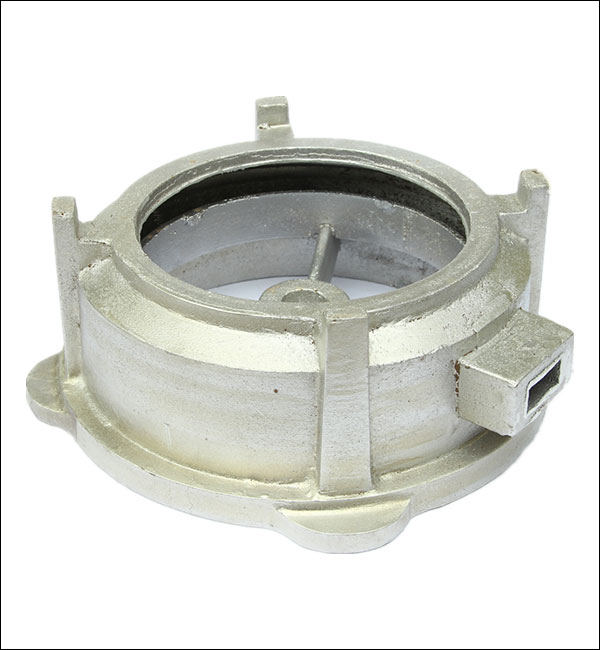
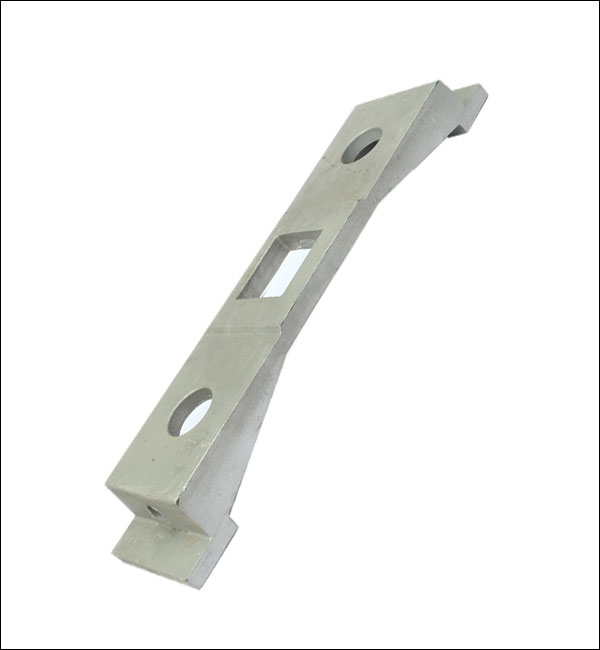
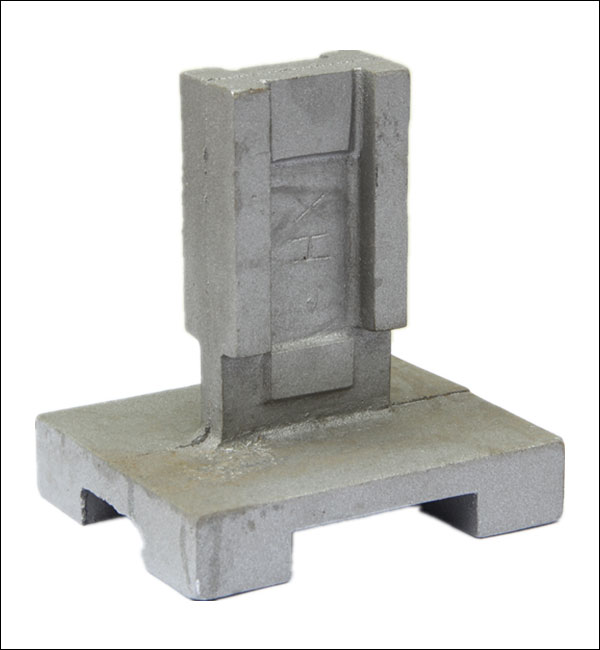
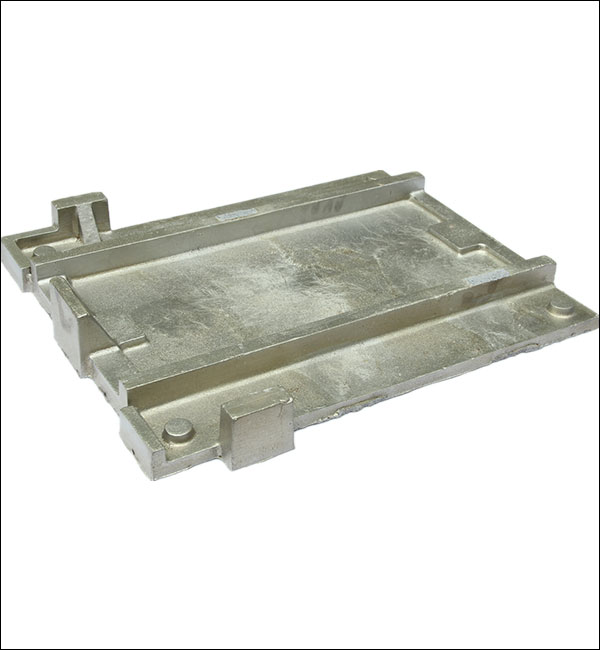
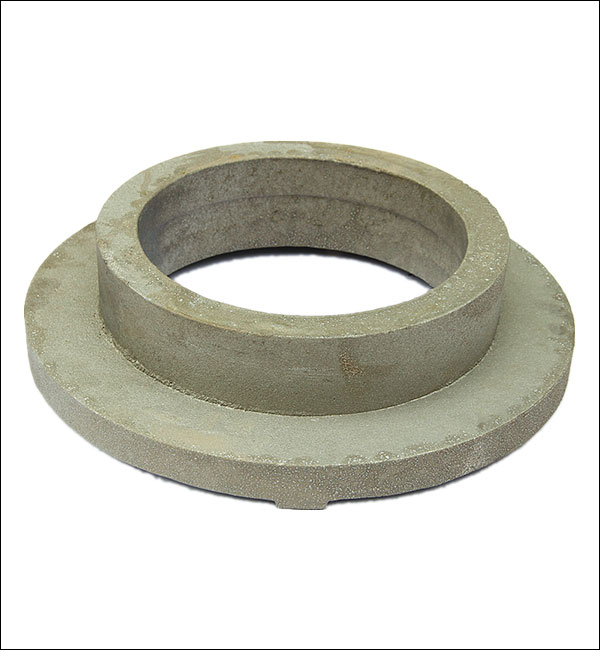
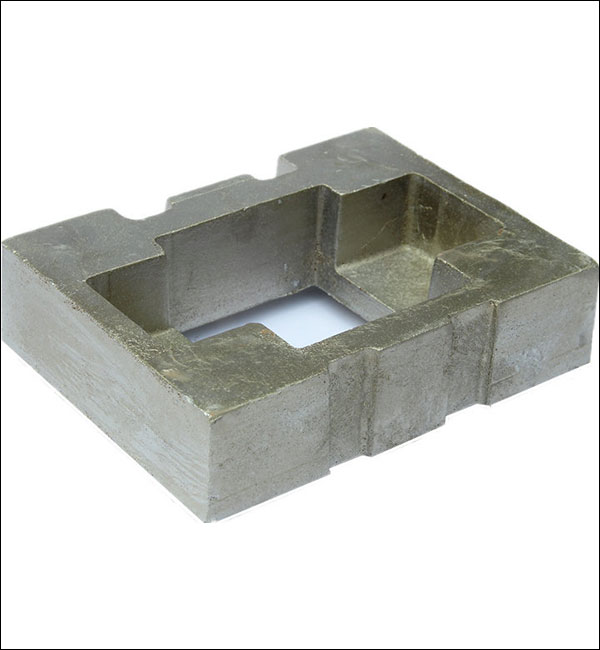
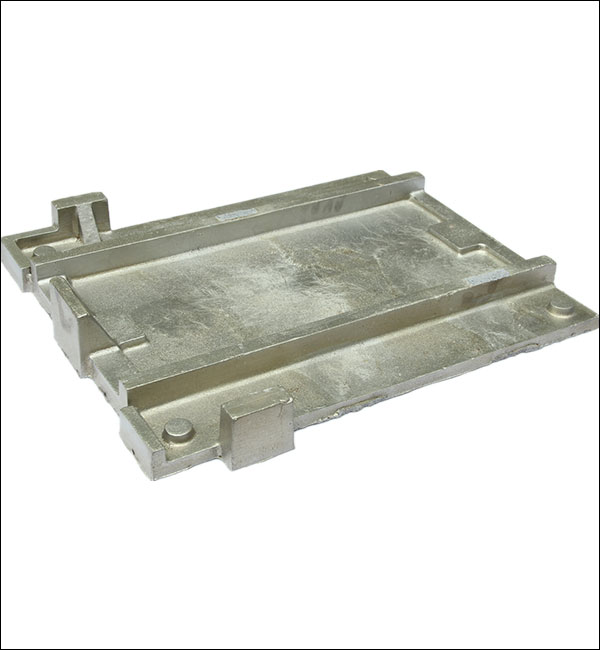
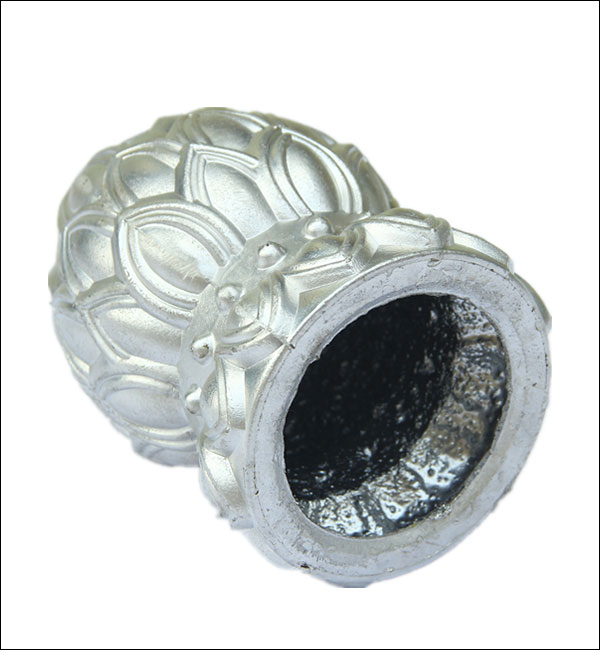
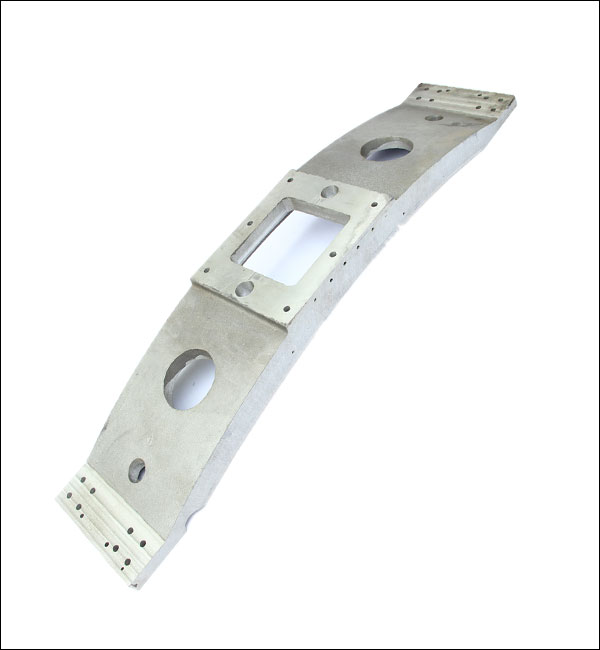

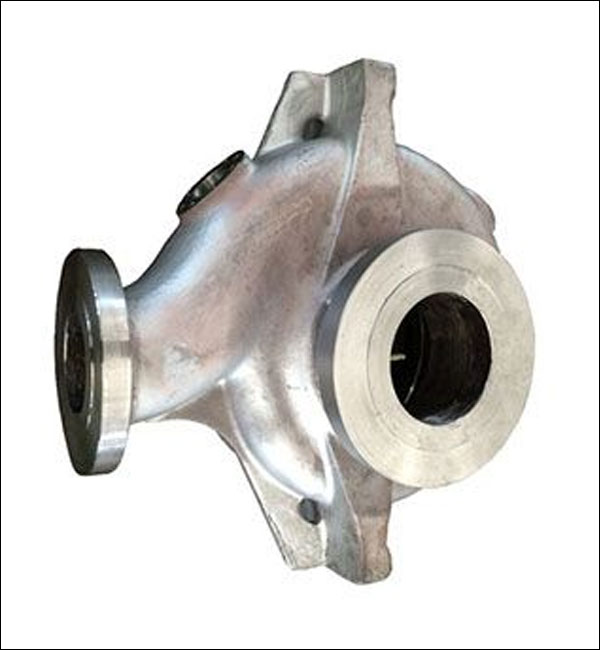
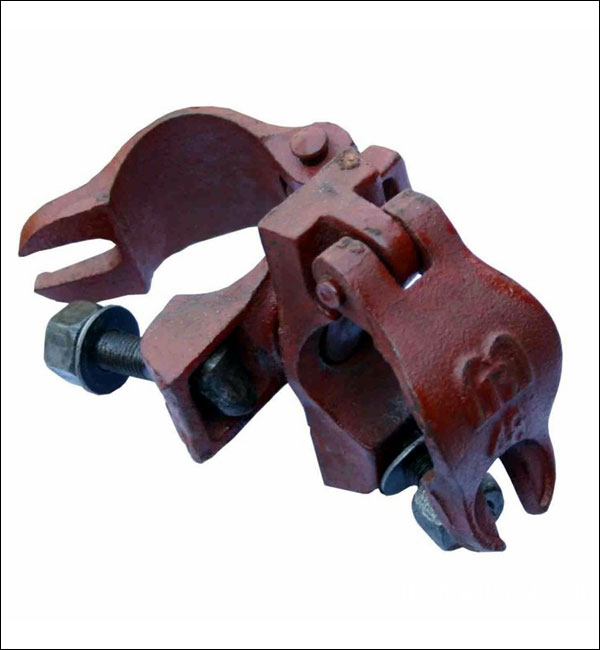
Go To View More Casting Parts Cases Studies >>>
Choose the Best Sand Casting Supplier
Currently, our Sand Casting parts are exported to America, Canada, Australia, United Kingdom, Germany, France, Sout Africa, and many other countries all over the world. We are ISO9001-2015 registered and also certified by SGS.
Our custom Sand Casting fabrication service provides durable and affordable castings that meet your specifications for automotive, medical, aerospace, electronics, food, construction, security, marine, and more industries. Fast to send your inquiry or submit your drawings to get a free quote in the shortest time.Contact us or Email sales@hmminghe.com to see how our people, equipment and tooling can bring the best quality for the best price for your sand casting project.
We Provide Casting Services Include:
Minghe Casting services working with sand casting、metal casting 、investment casting lost foam casting, and more.

Sand Casting
Sand Casting is a traditional casting process that uses sand as the main modeling material to make molds. Gravity casting is generally used for sand molds, and low-pressure casting, centrifugal casting and other processes can also be used when there are special requirements. Sand casting has a wide range of adaptability, small pieces, large pieces, simple pieces, complex pieces, single pieces, and large quantities can be used.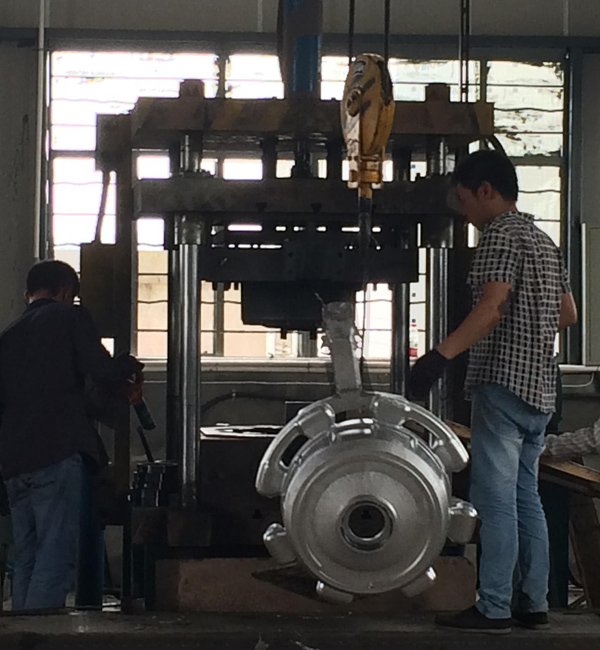
Permanent Mold Casting
Permanent Mold Casting have a long life and high production efficiency, not only have good dimensional accuracy and smooth surface, but also have higher strength than sand castings and are less likely to be damaged when the same molten metal is poured. Therefore, in the mass production of medium and small non-ferrous metal castings, as long as the melting point of the casting material is not too high, metal casting is generally preferred.
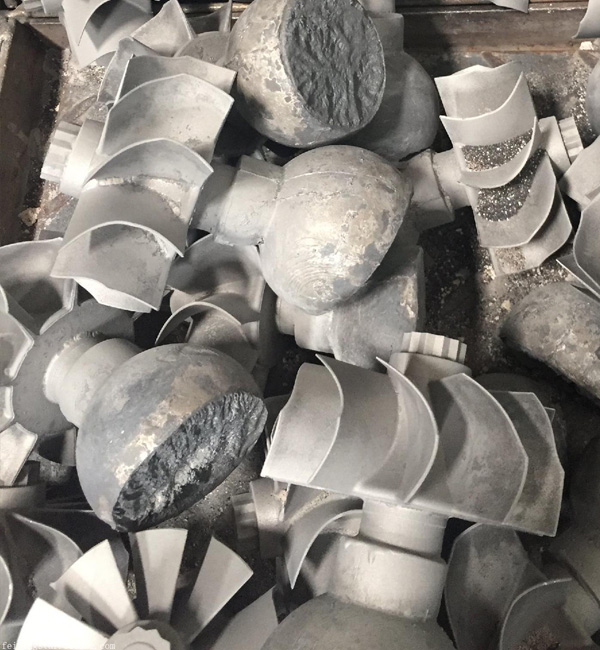
Investment Casting
The biggest advantage of investment casting is that because investment castings have high dimensional accuracy and surface finish, they can reduce machining work, but leave a little machining allowance on the parts with higher requirements. It can be seen that the use of investment casting method can save a lot of machine tool equipment and processing man-hours, and greatly save metal raw materials.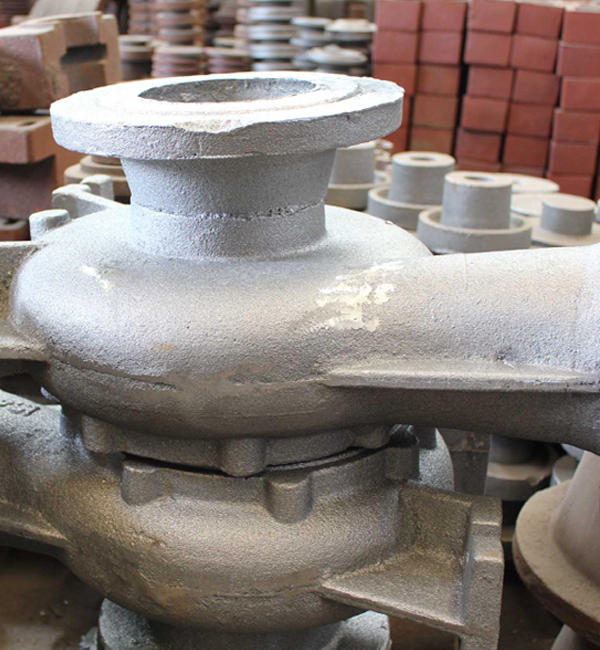
Lost Foam Casting
Lost foam casting is to combine paraffin wax or foam models similar to the casting size and shape into model clusters. After brushing and drying refractory coatings, they are buried in dry quartz sand for vibration modeling, and poured under negative pressure to gasify the model. , The liquid metal occupies the position of the model and forms a new casting method after solidification and cooling.

Die Casting
Die casting is a metal casting process, which is characterized by applying high pressure to the molten metal using the cavity of the mold. Molds are usually made of higher-strength alloys, and this process is somewhat similar to injection molding. Most die castings are iron-free, such as zinc, copper, aluminum, magnesium, lead, tin, and lead-tin alloys and their alloys. Minghe has been China's top die casting service since 1995.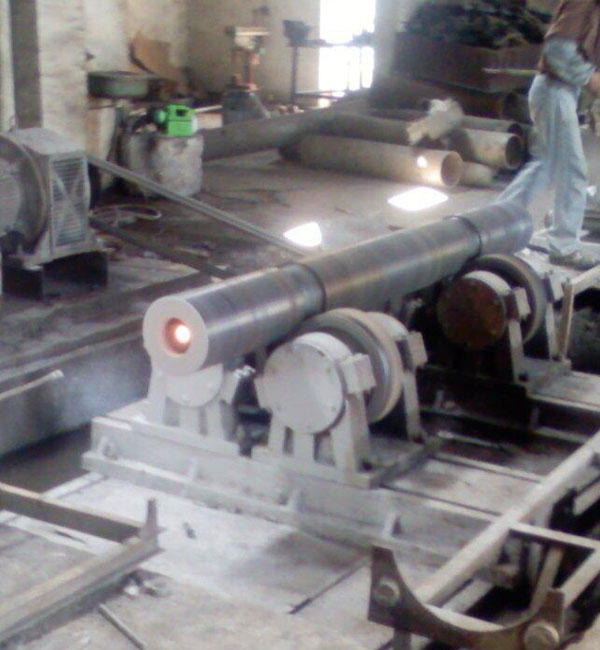
Centrifugal Casting
Centrifugal Casting is a technique and method of injecting liquid metal into a high-speed rotating mold, so that the liquid metal is centrifugal motion to fill the mold and form a casting. Due to the centrifugal movement, the liquid metal can fill the mold well in the radial direction and form the free surface of the casting; it affects the crystallization process of the metal, thereby improving the mechanical and physical properties of the casting.
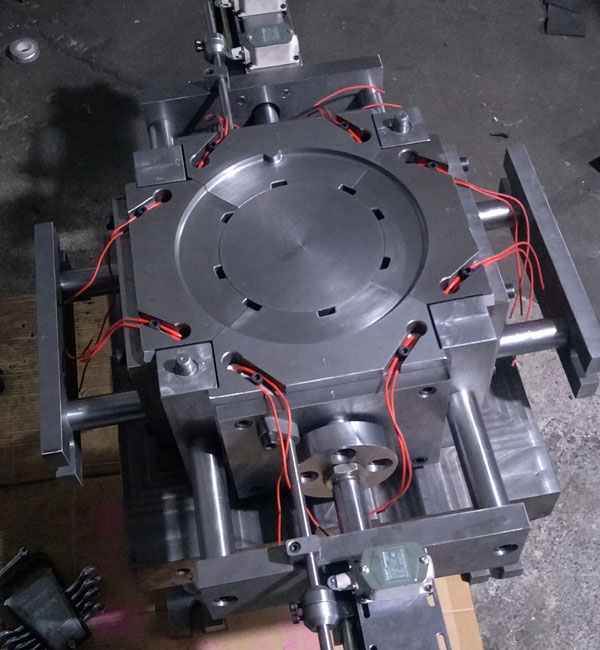
Low Pressure Casting
Low Pressure Casting means that the mold is generally placed above a sealed crucible, and compressed air is introduced into the crucible to cause a low pressure (0.06~0.15MPa) on the surface of the molten metal, so that the molten metal rises from the riser pipe to fill the mold and control Solidified casting method. This casting method has good feeding and dense structure, easy to cast large thin-walled complex castings, no risers, and a metal recovery rate of 95%. No pollution, easy to realize automation.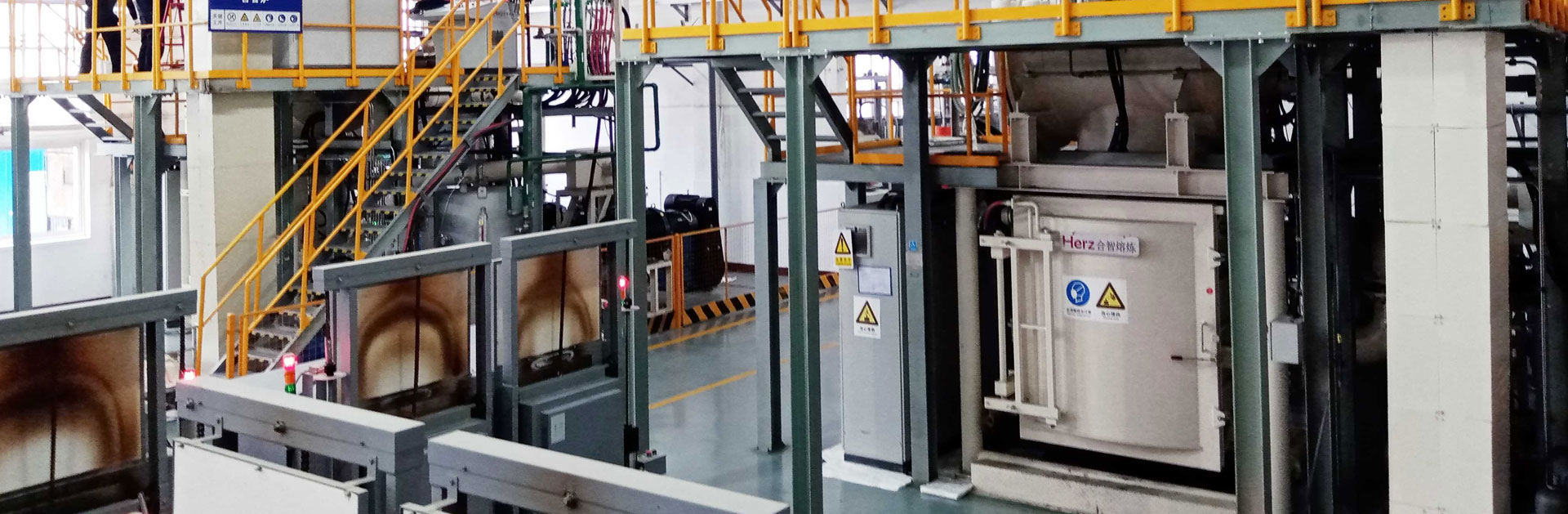